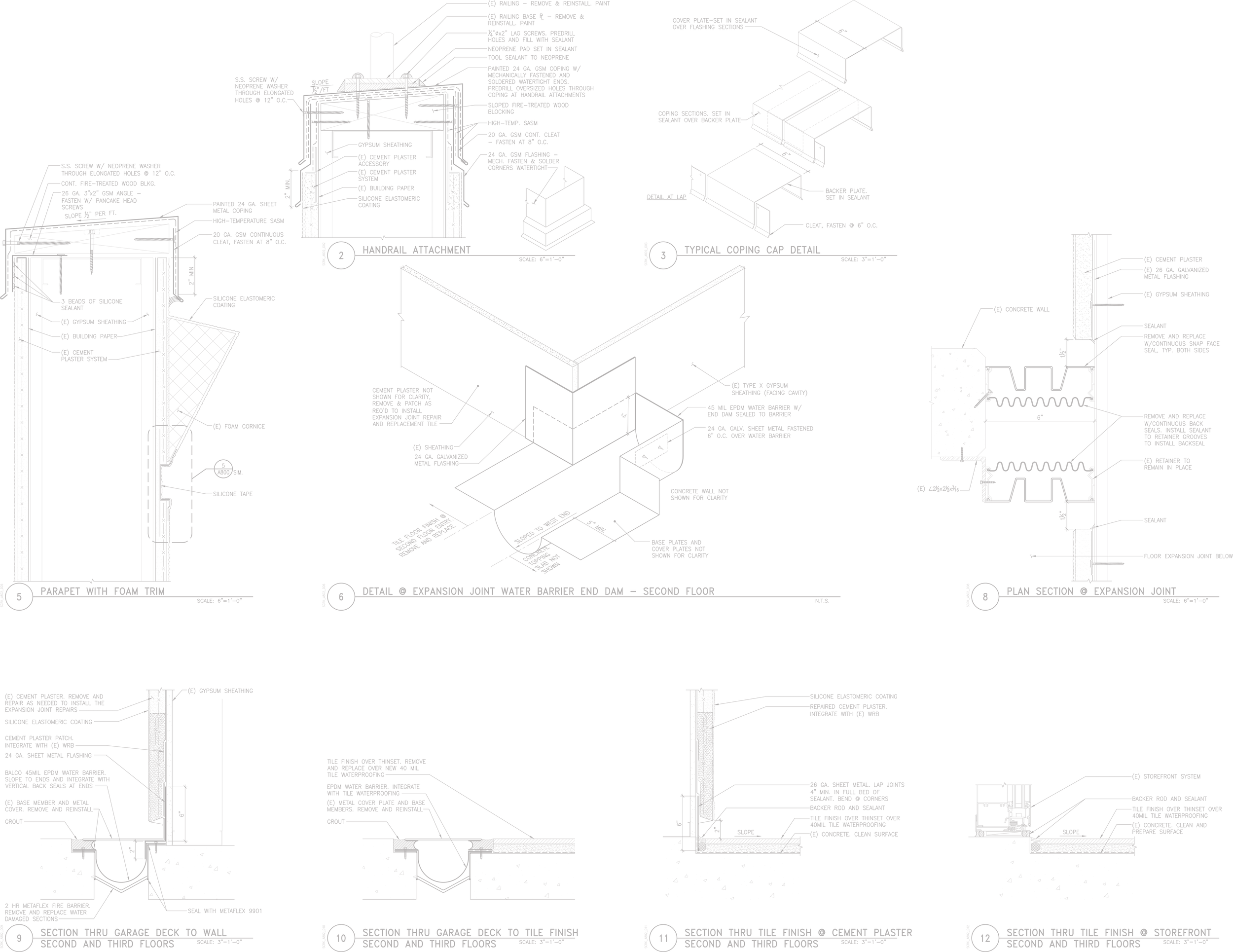
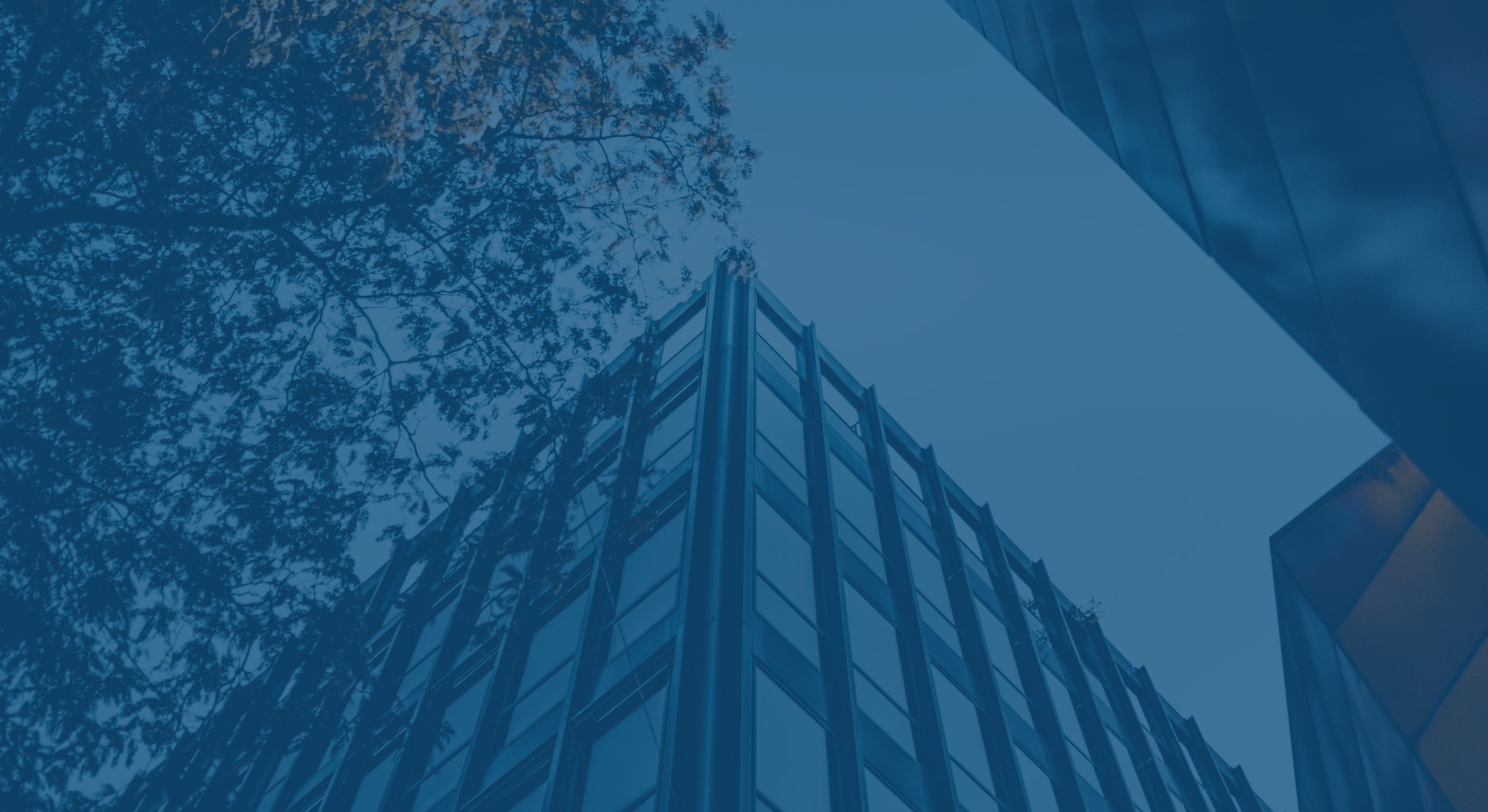
Types Of Buildings We Work On
SUCCESS STORIES
Amazing clients allow us to produce work we’re proud of
Frequently
Asked Questions
-
It is a good idea to perform an overall condition assessment of building exteriors every 6 to 8 years to forecast capital budgets for exterior repair budgets.
-
The functional life expectancy of urethane sealant is 5 to 8 years, depending on UV exposure. The life expectancy of silicone sealant can be 15 to 20 years or longer.
-
Typically, urethane deck coatings last 5 to 7 years, depending on the amount of traffic.
Most deck coating manufacturers offer a “5+5” material warranty, which means if a top coat is installed after year 5 of the original installation, they will extend the warranty for an additional 5 years.
-
EIFS stands for Exterior Insulation Finish System.
It is a wall cladding system that places the insulation on the exterior side of the building. The typical assembly consists of adhesive (for adhering insulation board to the wall sheathing), insulation board, reinforcement mesh, and a composite exterior coating system.
Early EIFS systems rely solely on the exterior coating and joint sealant between panels for waterproofing. More recent systems include a weather barrier coating on the wall sheathing to provide a secondary defense against water intrusion.
-
In most cases, concrete spalls or delamination originate from water intrusion into the concrete. When water enters the concrete through cracks or penetrations, it corrodes the reinforcement steel (rebar) in the concrete and causes the steel to corrode. The corrosion causes the steel to expand and exert pressure on the concrete, causing the concrete to delaminate and be “pushed out”.
This condition can create a life-safety hazard from falling concrete. (The reason the City of San Francisco enacted the SF Façade Ordinance in 2016) Left untreated, the reinforcement will continue to corrode and eventually compromise the structural integrity of the concrete.
-
The design of most window or curtain wall systems relies on a “drainage system,” which allows water to enter the internal assembly through glazing gaskets and/or window frame joints and weep out via the weep holes.
This design relies on the internal joints between the frame members (especially between the window sill and jamb) to be properly sealed, so the only exit for water is through the weep holes.
However, the internal seal can be compromised due to aging and/or movement. When the internal seal is compromised, water that enters the window/curtain wall assembly can leak through the internal joints into the building. When this occurs, a common way to address it is to convert the “drainage system” into a “barrier system”, which involves wet sealing between glass and frame and sealing all exterior butt joints in the frames, essentially preventing any water from entering the window/curtain wall assembly.
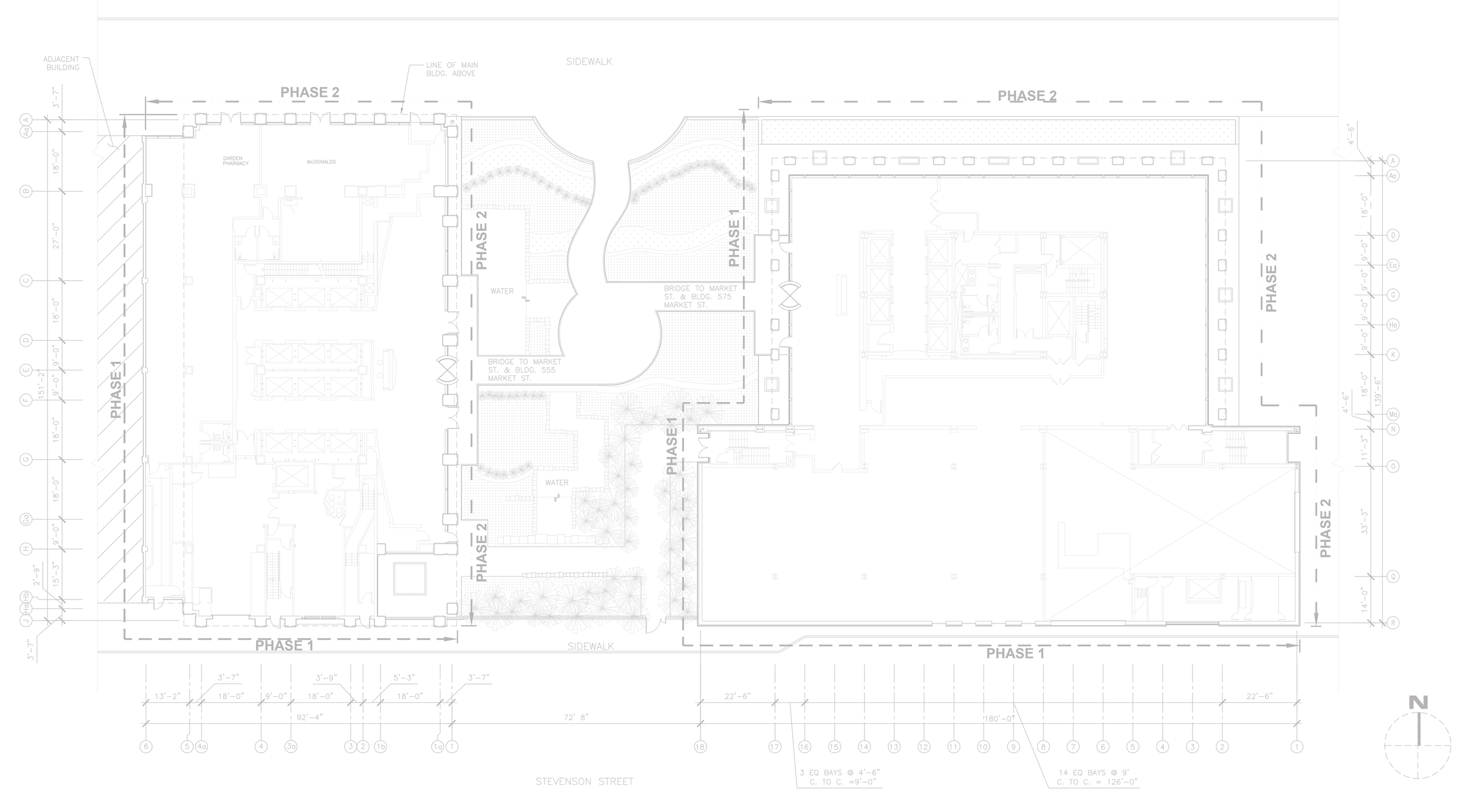