Flooding high school utility room saved with epoxy and grout
Alameda High Basement
Alameda High School was scheduled for a complete restoration, part of which was an important waterproofing scope in the basement, which was scheduled to contain key electrical and mechanical equipment. The problem—due to its location close to the bay, the low elevation, and the fact that the basement was 15’ below grade—made it very susceptible to flooding during any rain event that impacted the already saturated water table. Urban Waterproofing was hired to install waterproofing repairs designed by Terracon to keep the basement and the electrical and mechanical equipment inside it dry and functional for the school. This was key because we had to employ a variety of waterproofing repairs—grout injection, spall repair, and waterproof membrane coating—to resolve a very challenging leak.
In this case, the basement walls and floor were under tremendous hydrostatic pressure from the surrounding soil. Like most basements, it was impractical to try to excavate around the basement walls and impossible to dig out underneath the floor to apply waterproofing on the positive side (where the water is coming from). Therefore, negative side repairs are required, consisting of injecting water-reactive chemical grout through the wall to the soil and then applying an epoxy coating to the walls. A belt and suspender approach.
You want to keep the water away from the walls and prevent it from migrating through to make sure the reinforcing steel in the walls doesn’t corrode, lose structural integrity, and cause the walls to crack and spall. Water getting into these key mechanical areas can also cause damage to mechanical equipment and, where large electrical panels are placed, a safety hazard.
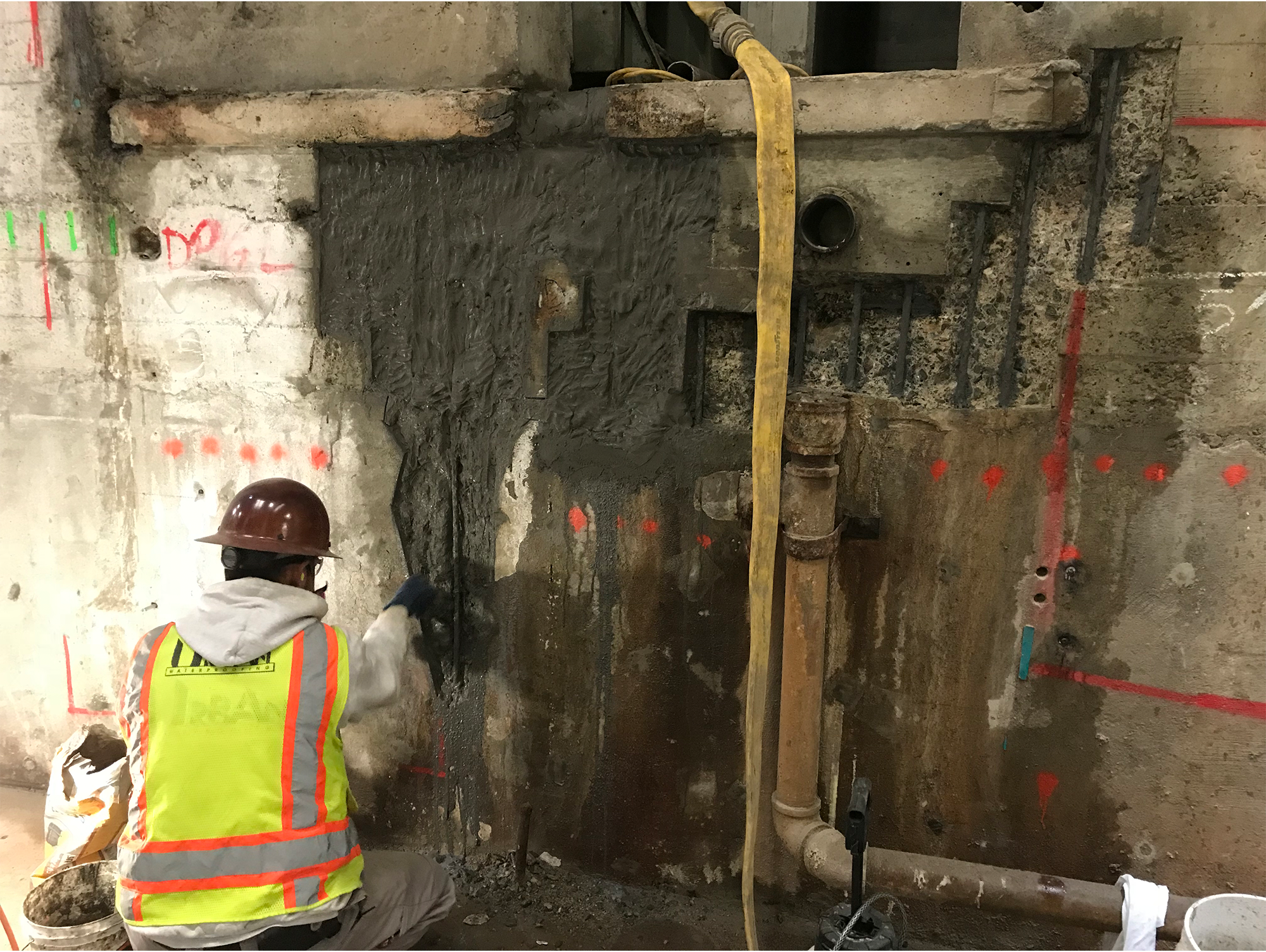
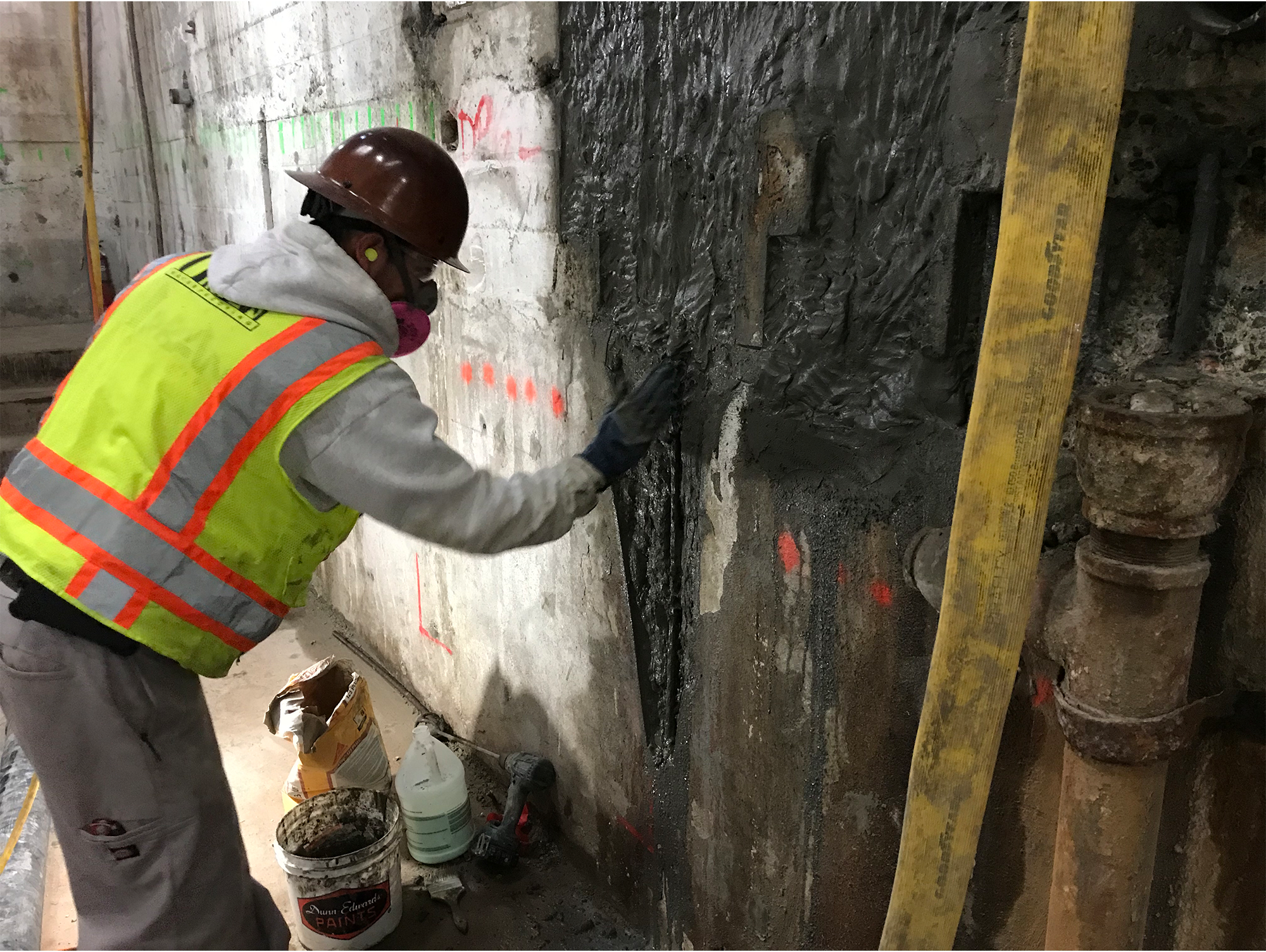
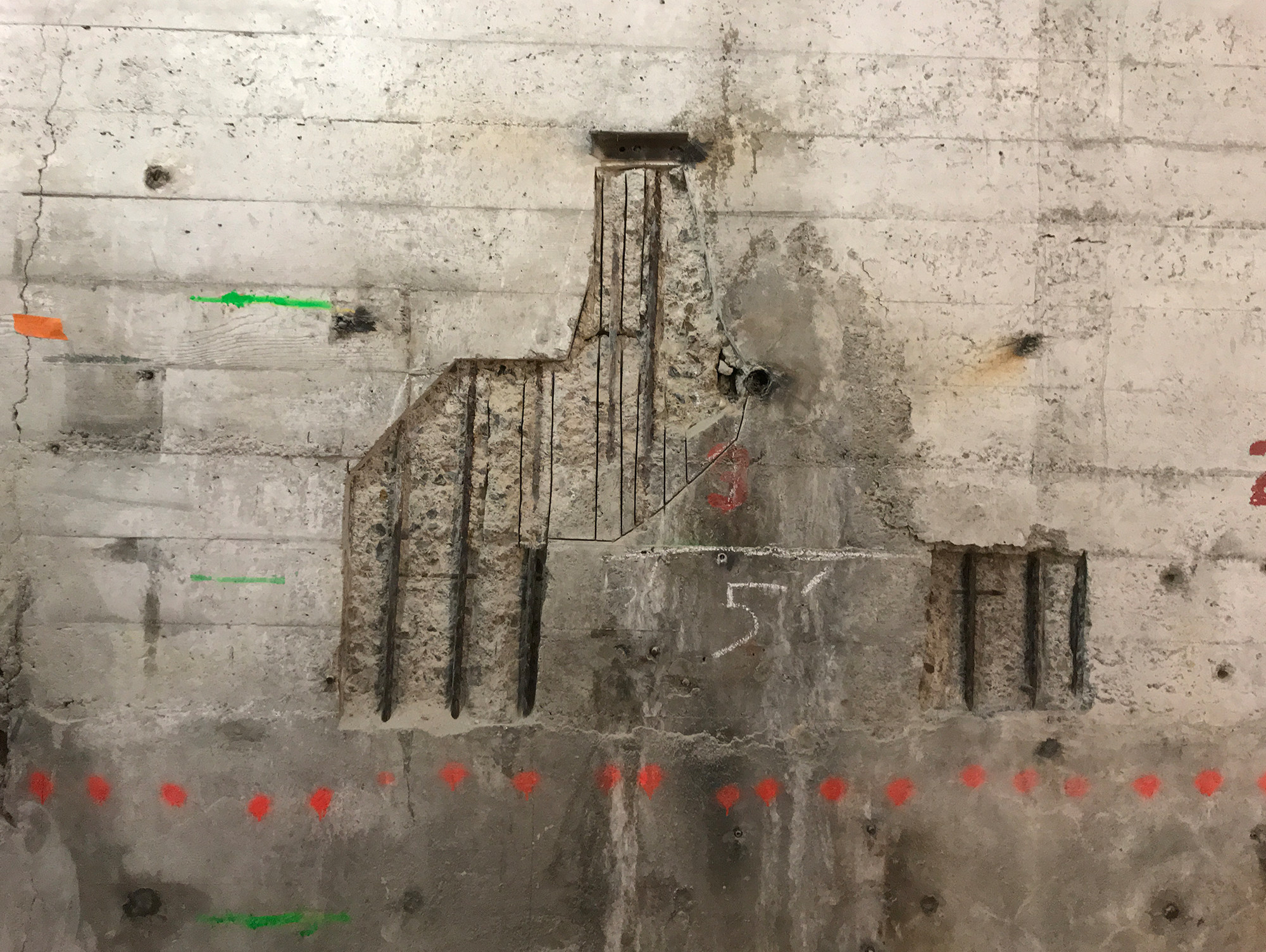
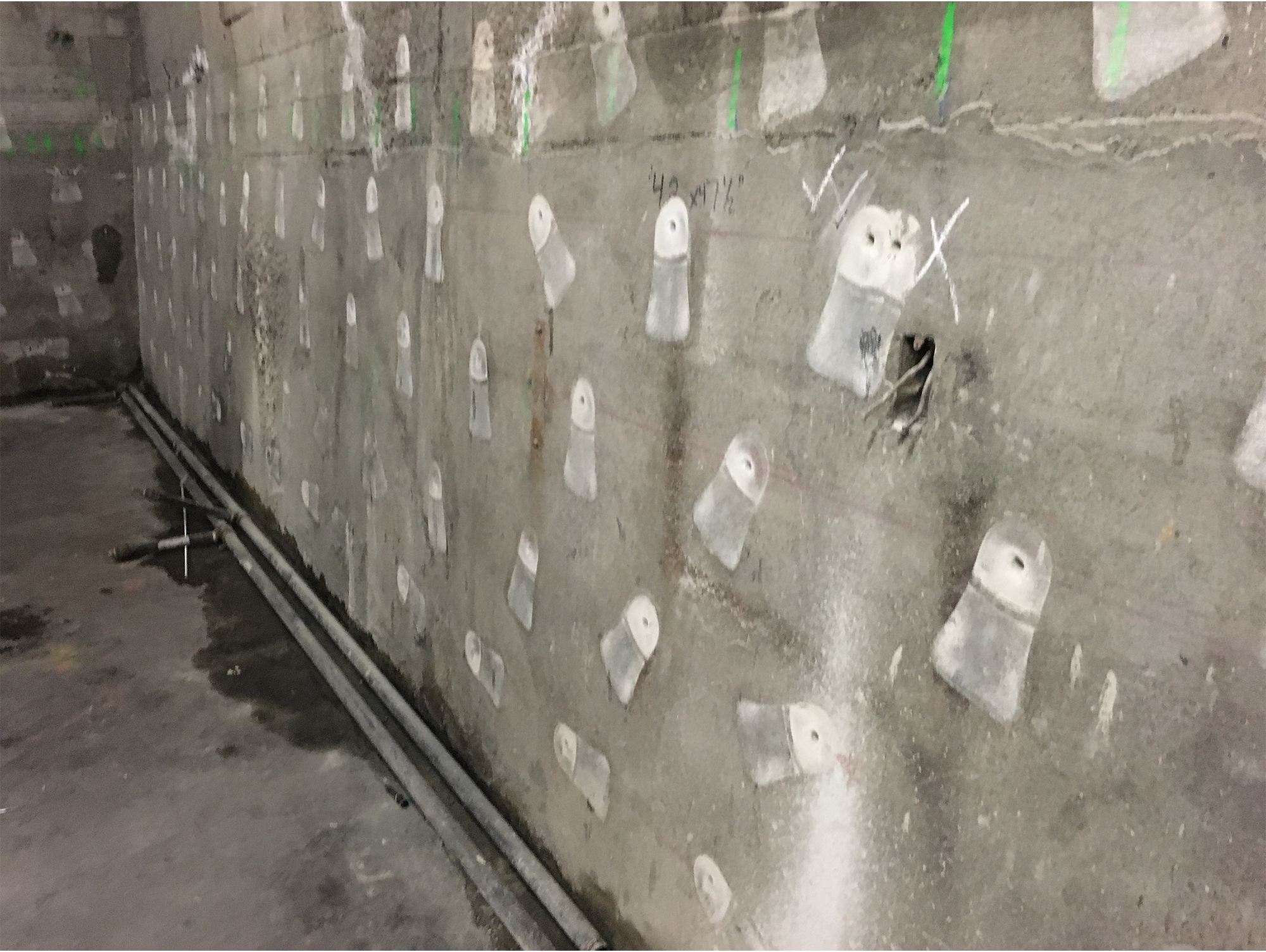
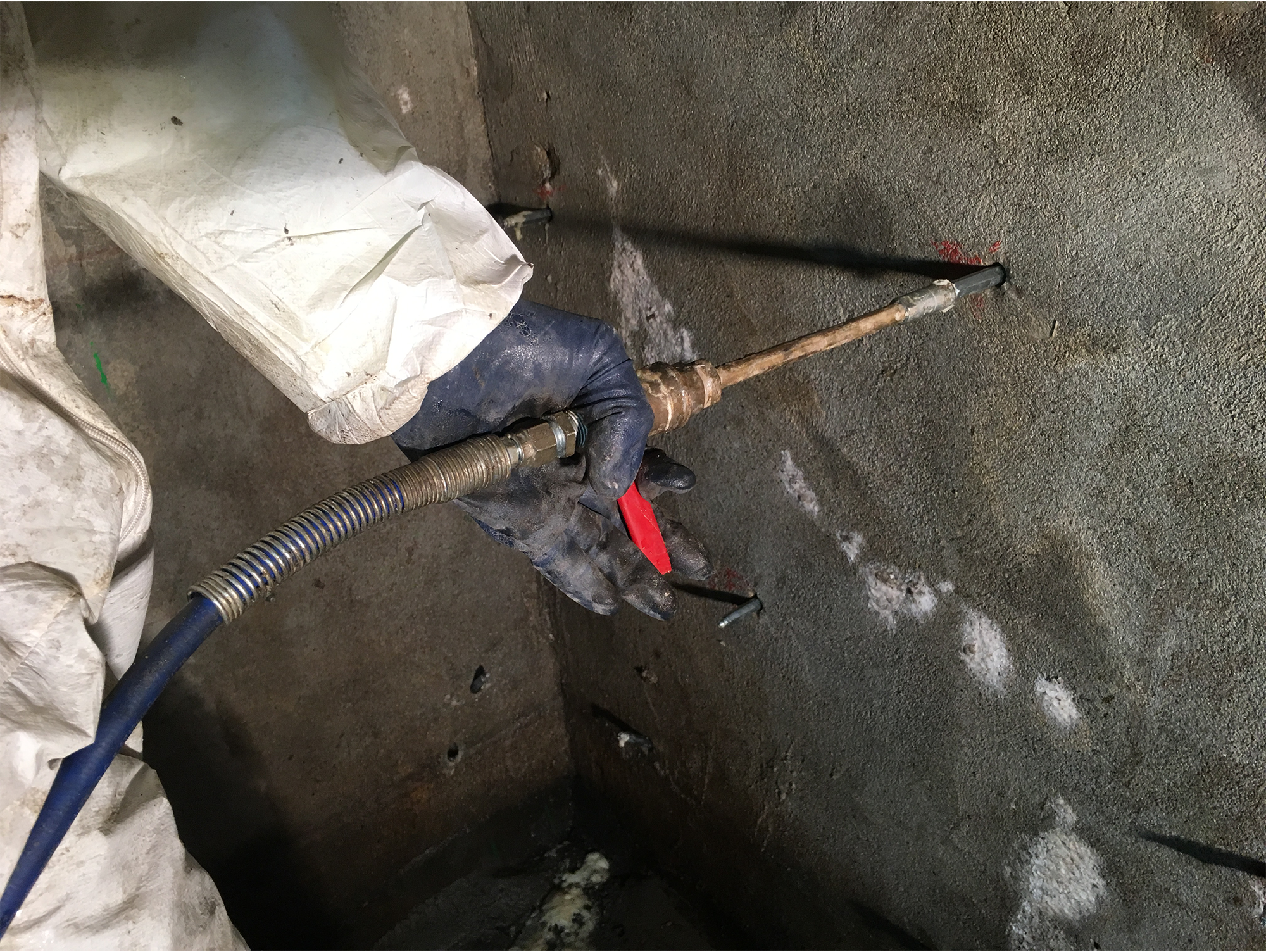
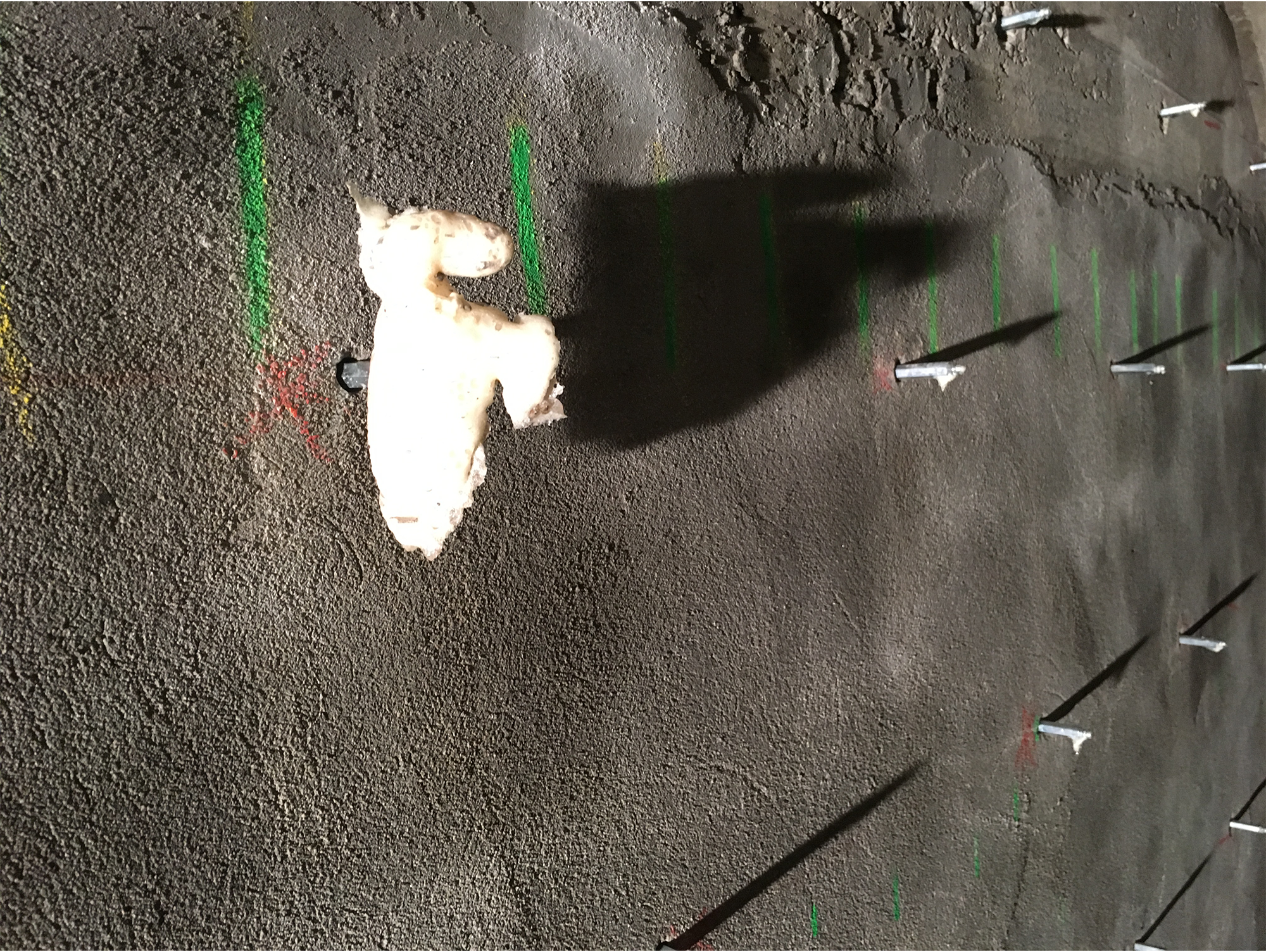
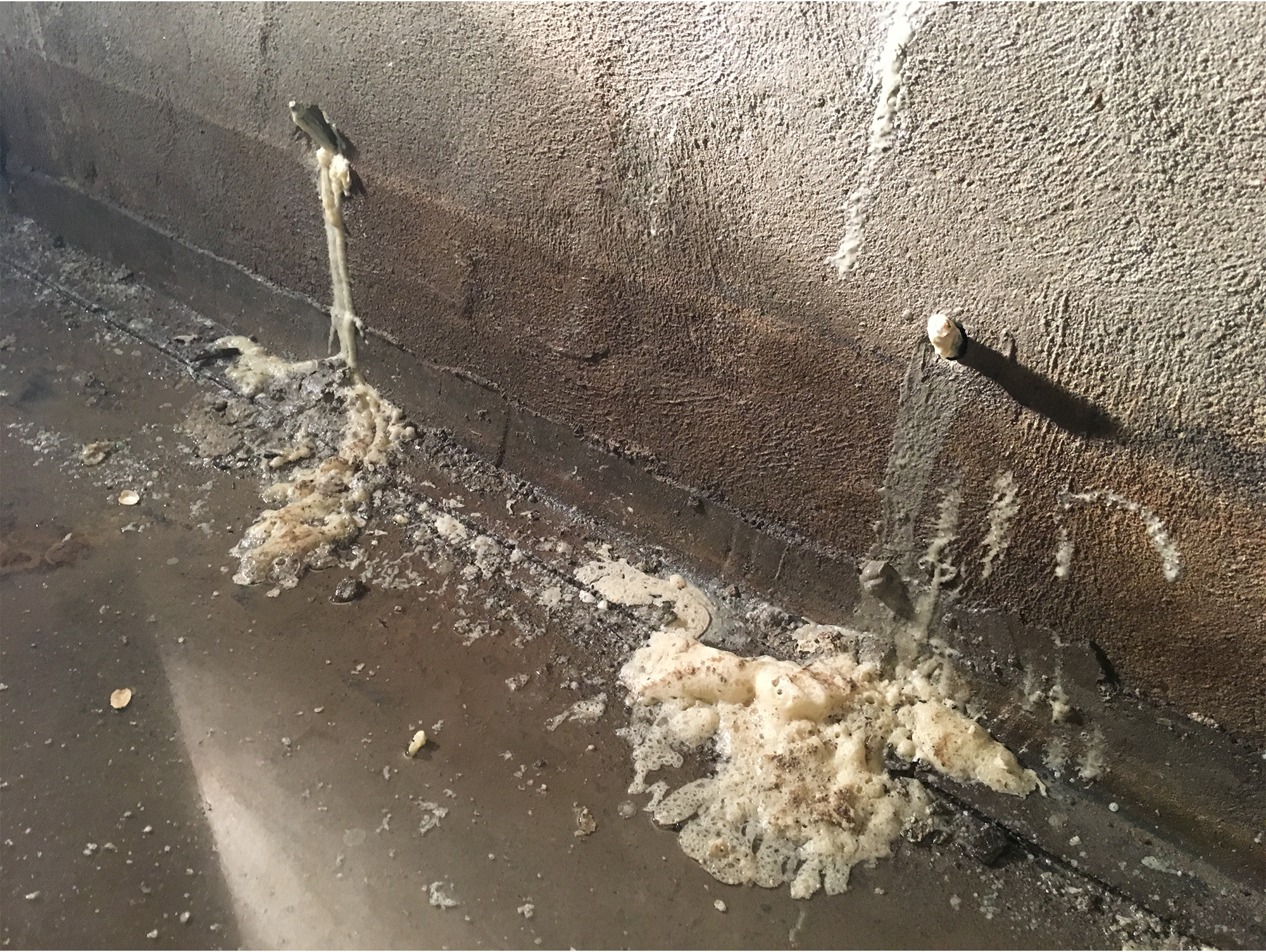

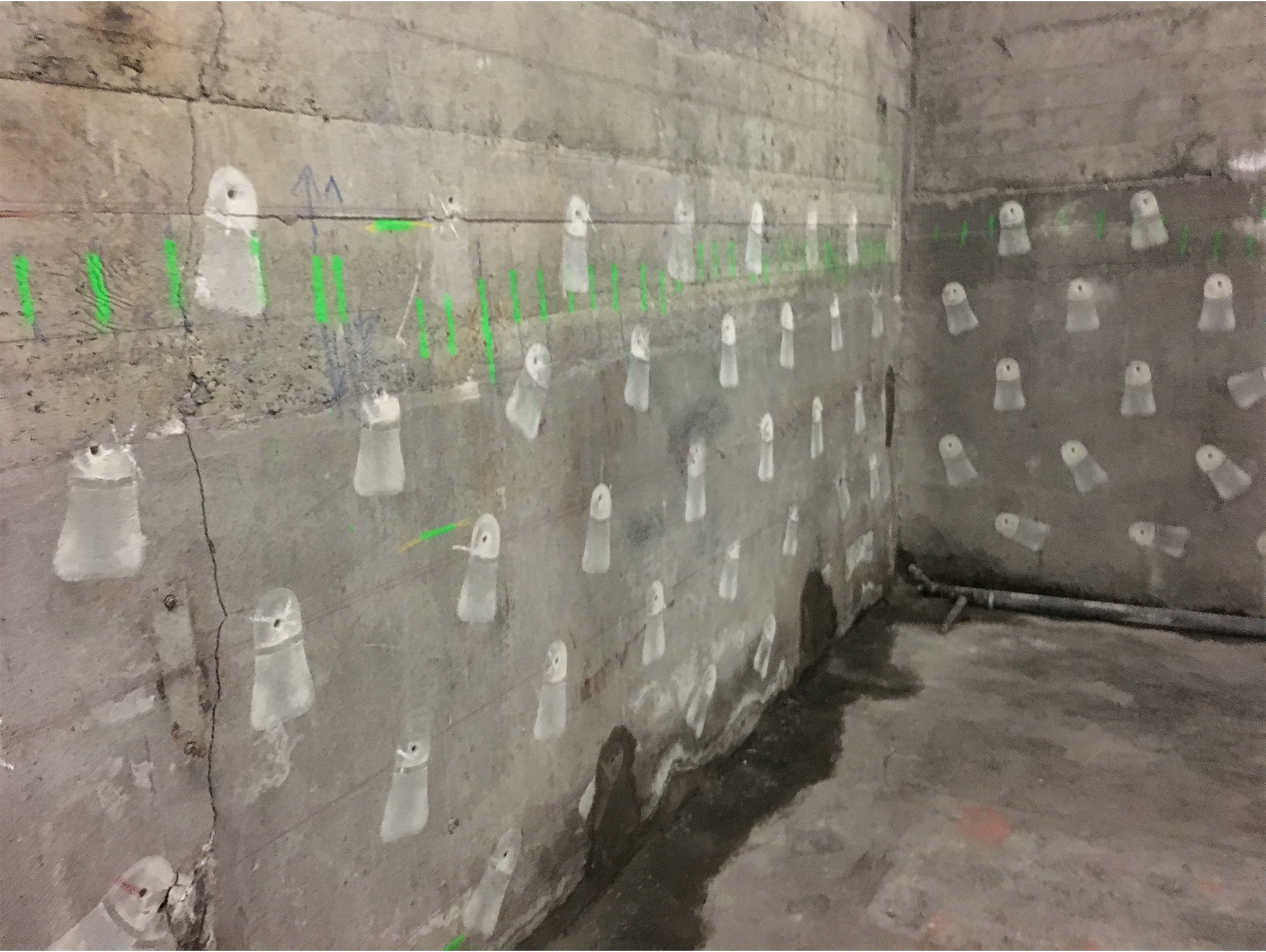
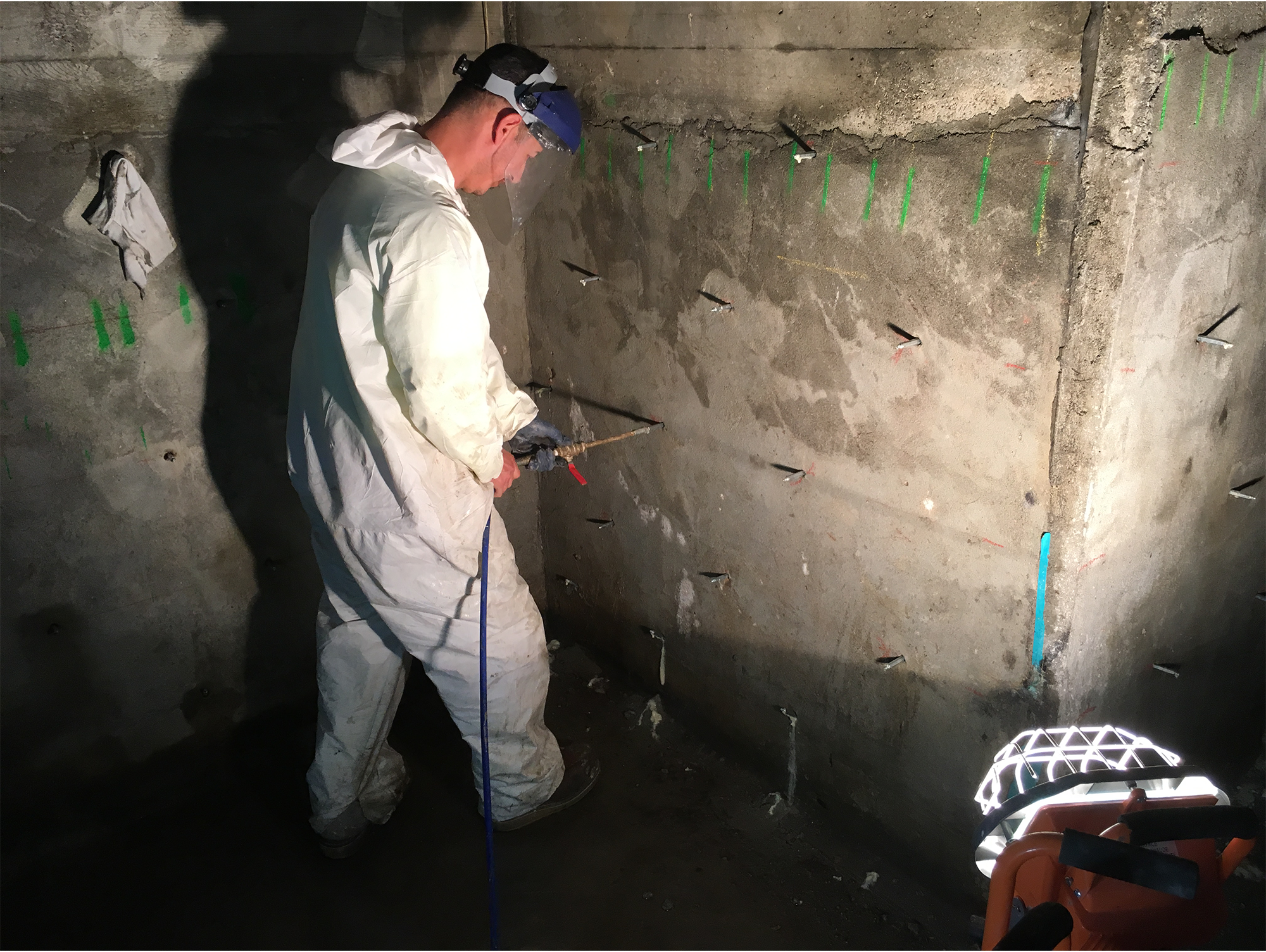
What We Did
Installed and injected nearly 700 ports—almost 280 gallons of DeNeef urethane grout
Applied over 3000 sf of Aquafin SG2 epoxy vapor barrier to walls and floors
Repaired numerous concrete spalls in walls
Repaired concrete spalls in the floor and installed CIM 1000 waterproof membrane to detail components in utility trenching
Project Details
The project was on a tight schedule to waterproof a basement that was constantly flooding before new mechanical equipment and a large electrical service panel serving an entire high school were installed. Working around other trades and around a dense matrix of pipes and conduits, the concrete surfaces of the walls and floors were blasted to remove surface contaminants and provide a surface profile for the new waterproofing material. Concurrently, over 700 injection ports were installed. The techs had to scan the wall first to locate the structural steel and map out a grid to best avoid drilling directly into the rebar sections. In order to install a complete repair on the backside of the wall, injection pores are spaced out at regular intervals, creating a generally intact and continuous membrane on the backside of the wall as the injection sections expand with contact with water and connect to each other. Once the plan and grid were created, drilling the hole began, using a 12’ long auger bit to drill through the wall. As drilling commenced, water would shoot out through the drilled hole, an indication of the constant hydrostatic pressure the walls were experiencing.
Fortunately, the epoxy grout NEEDS water to activate, so after the initial release, injection of the ports could begin. With the wall finally injected—about 160 running feet by 5 feet high—we could apply the Aquafin epoxy membrane as a secondary measure to stop the water.
In the course of preparing the work area(s), we discovered a number of locations where prior concrete surface filler patches were coming loose. The patches appeared to be temporary and nothing more than simple surface filler. We removed those patches and prepared for new ones, including the installation of new reinforcing steel to hold the new patches in place.
Finally, with the walls injected and coated with the epoxy vapor barrier, we could apply the same coating to the floors, finishing off the basement and mechanical room with a state-of-the art retrofit waterproof membrane.
Want to know how we can help with your next project?