Best in class foundation waterproofing to protect interior surfaces
Menlo Corporate Center
A prominent office campus in Redwood City was experiencing water intrusion on the first floor of all six campus buildings, causing costly repairs and inconvenience delays.
During rain events, the office spaces and work areas were out of commission while fans were brought in to dry out the carpets, in addition to the damage to expensive interior office finishes.
This project had an additional complication surrounding their landscape, a key feature of the site that was not on the table for removal. Our team was up for the challenge of preserving the landscaping while preventing water intrusion at the foundation level to avoid future damage and costly repairs.
Due to the size and scope of this project, it is ongoing, with buildings phased in each year for the installation of the membrane.
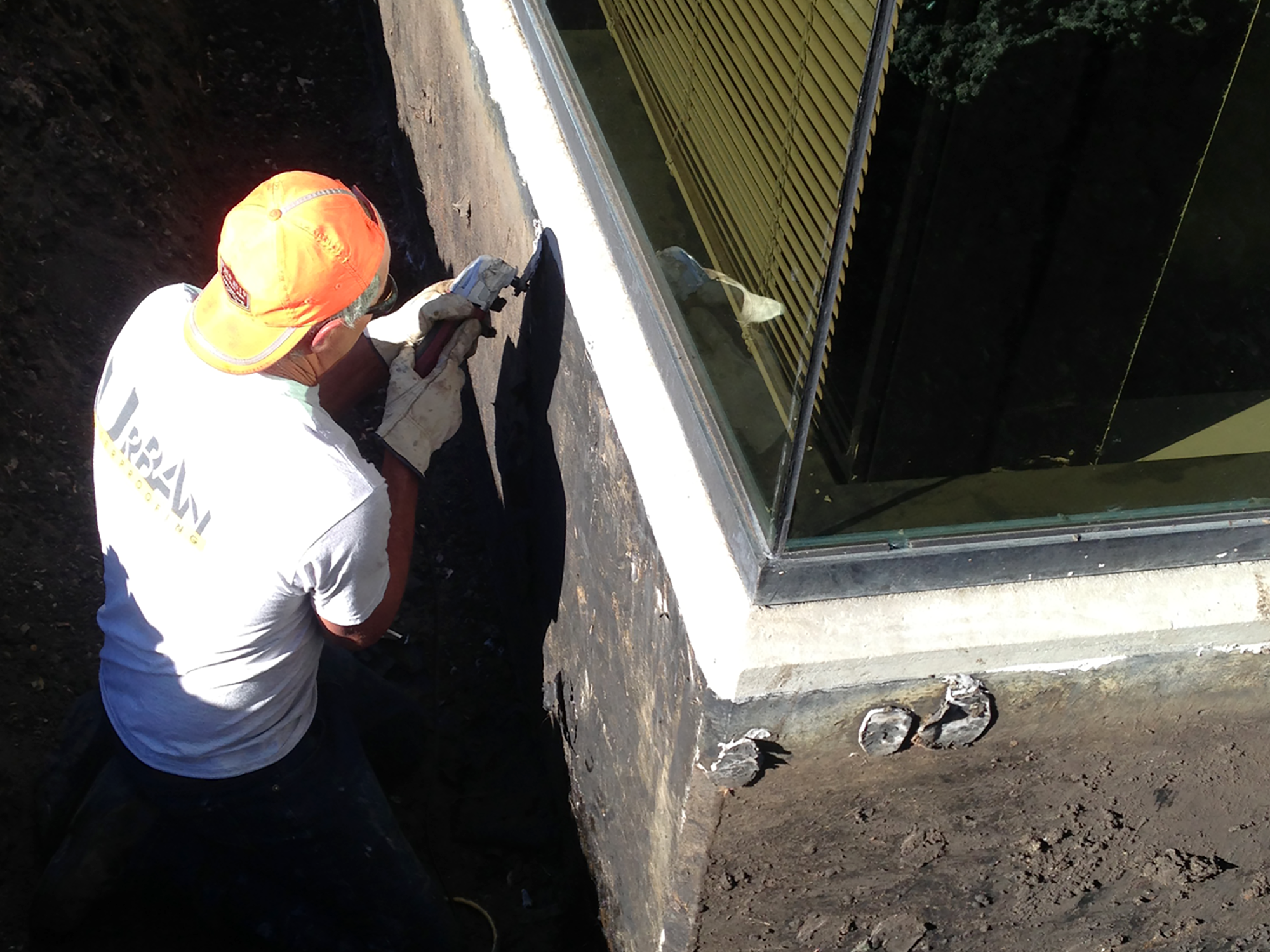
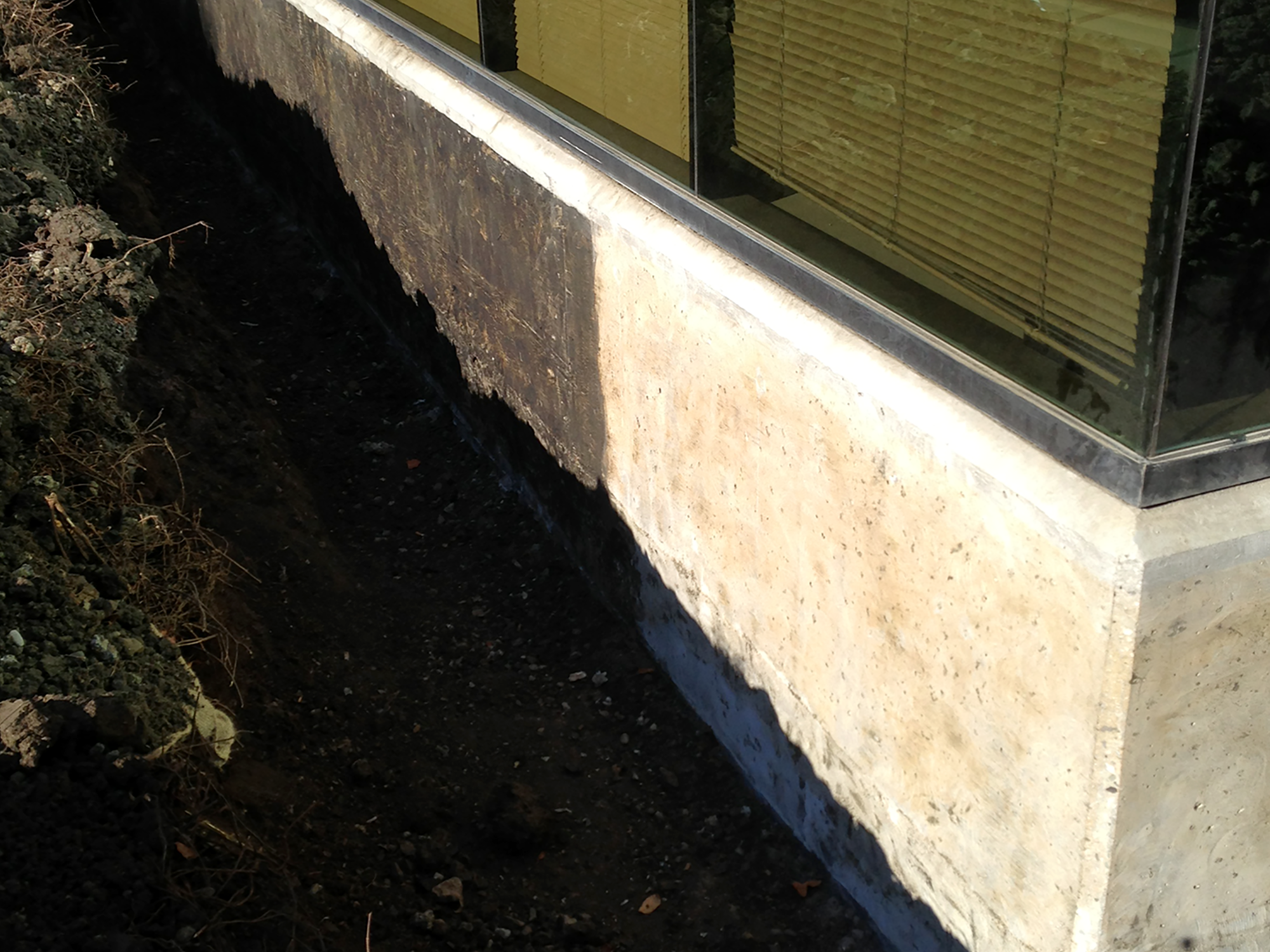
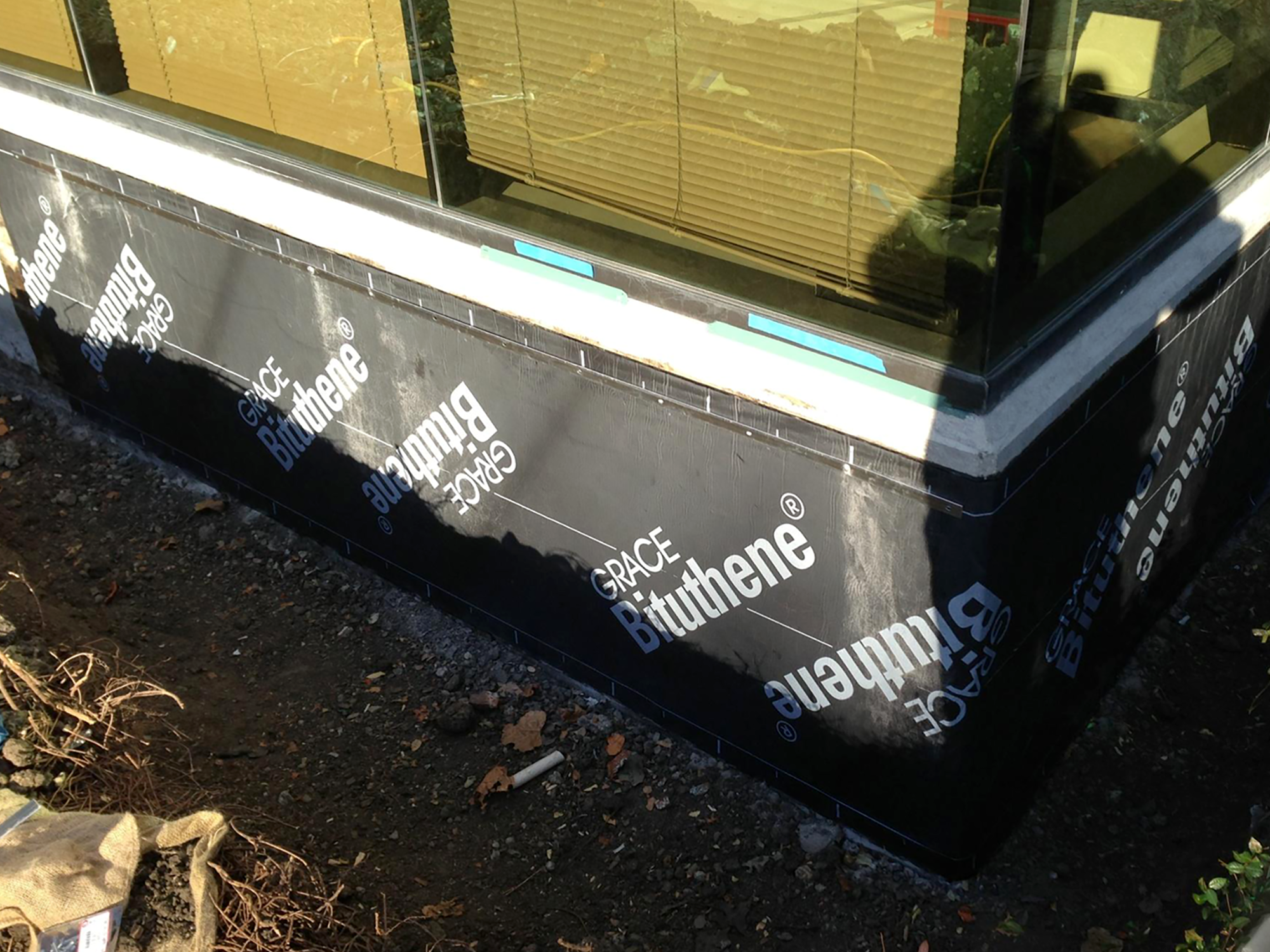
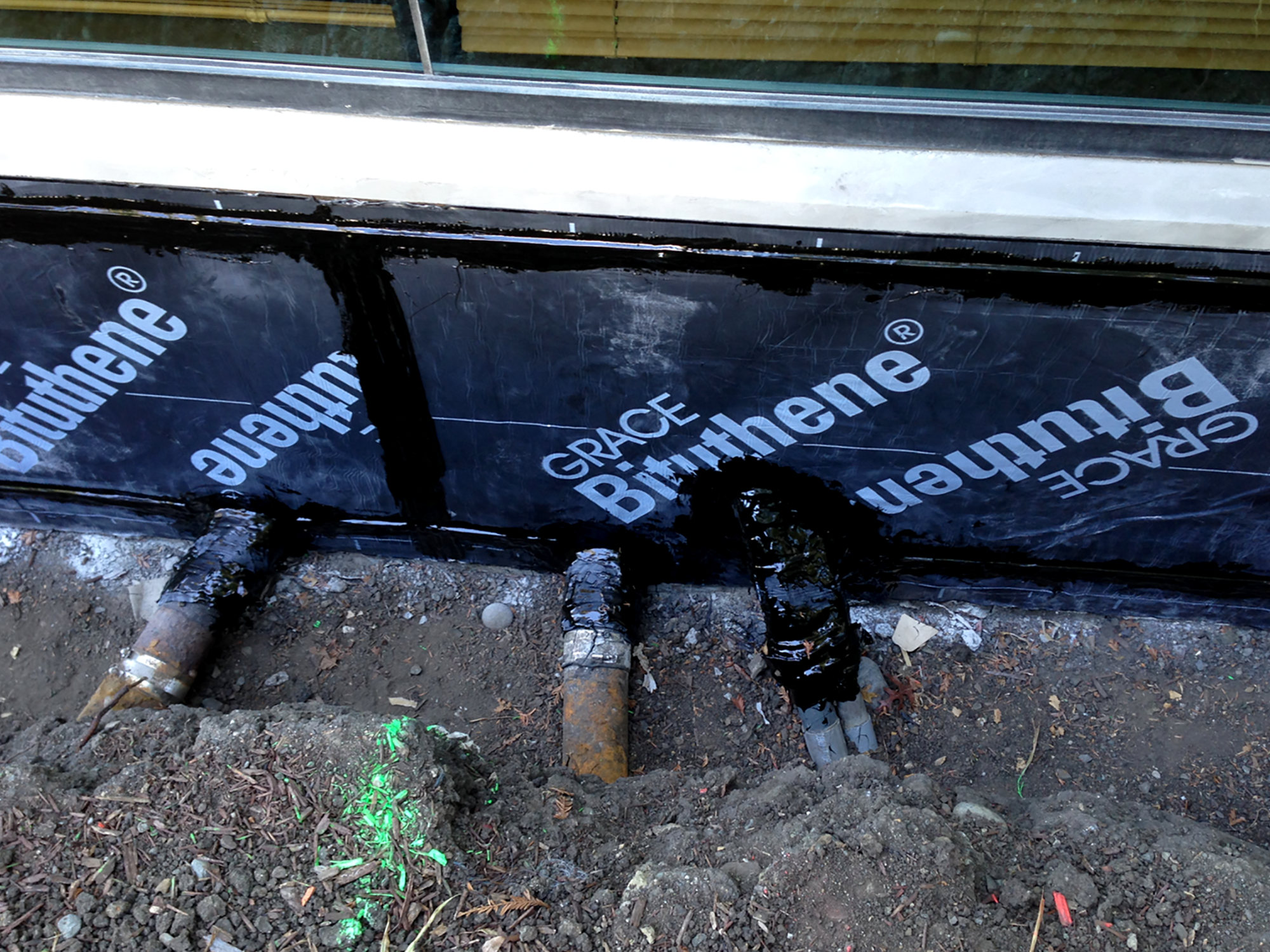
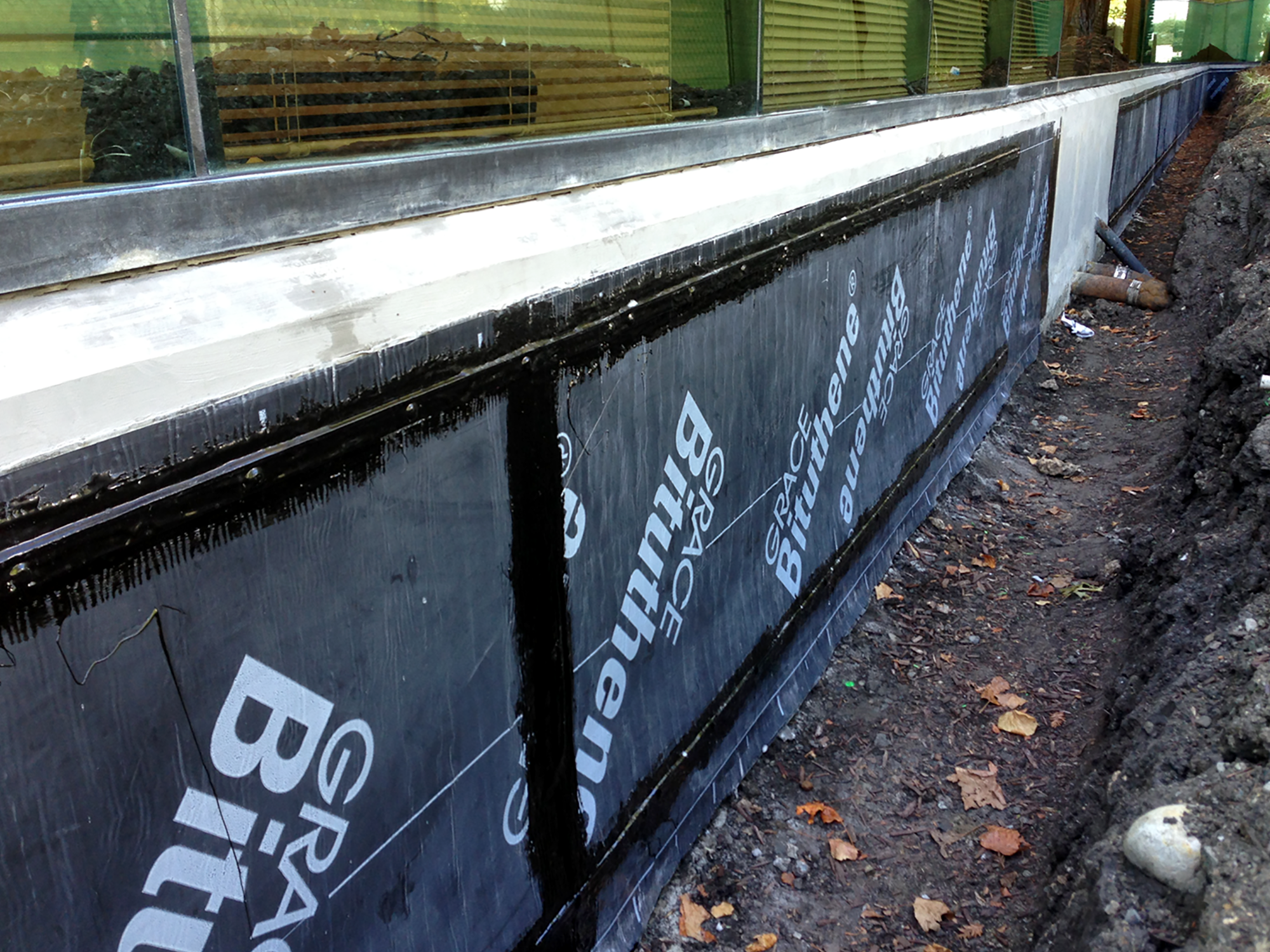
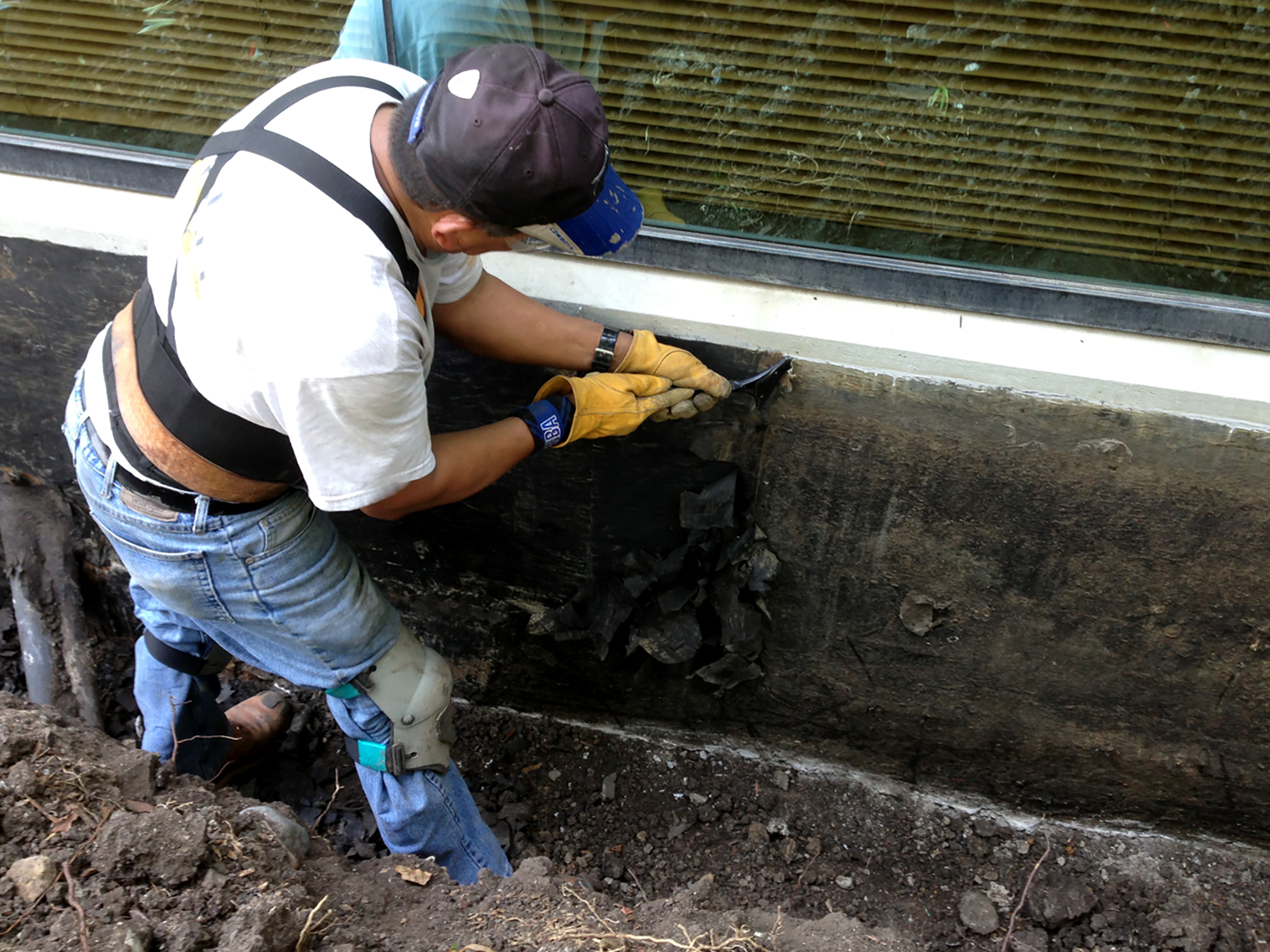
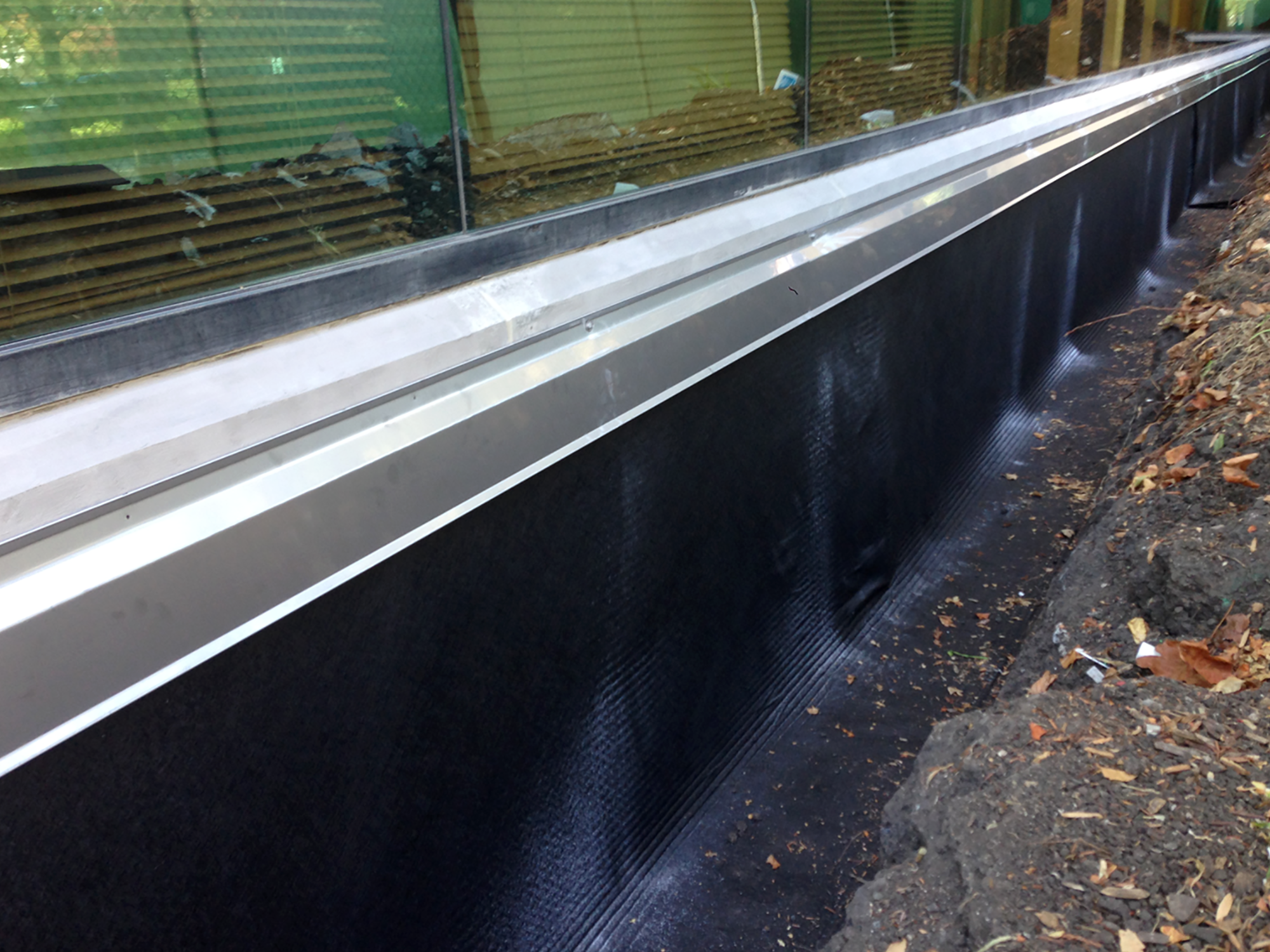
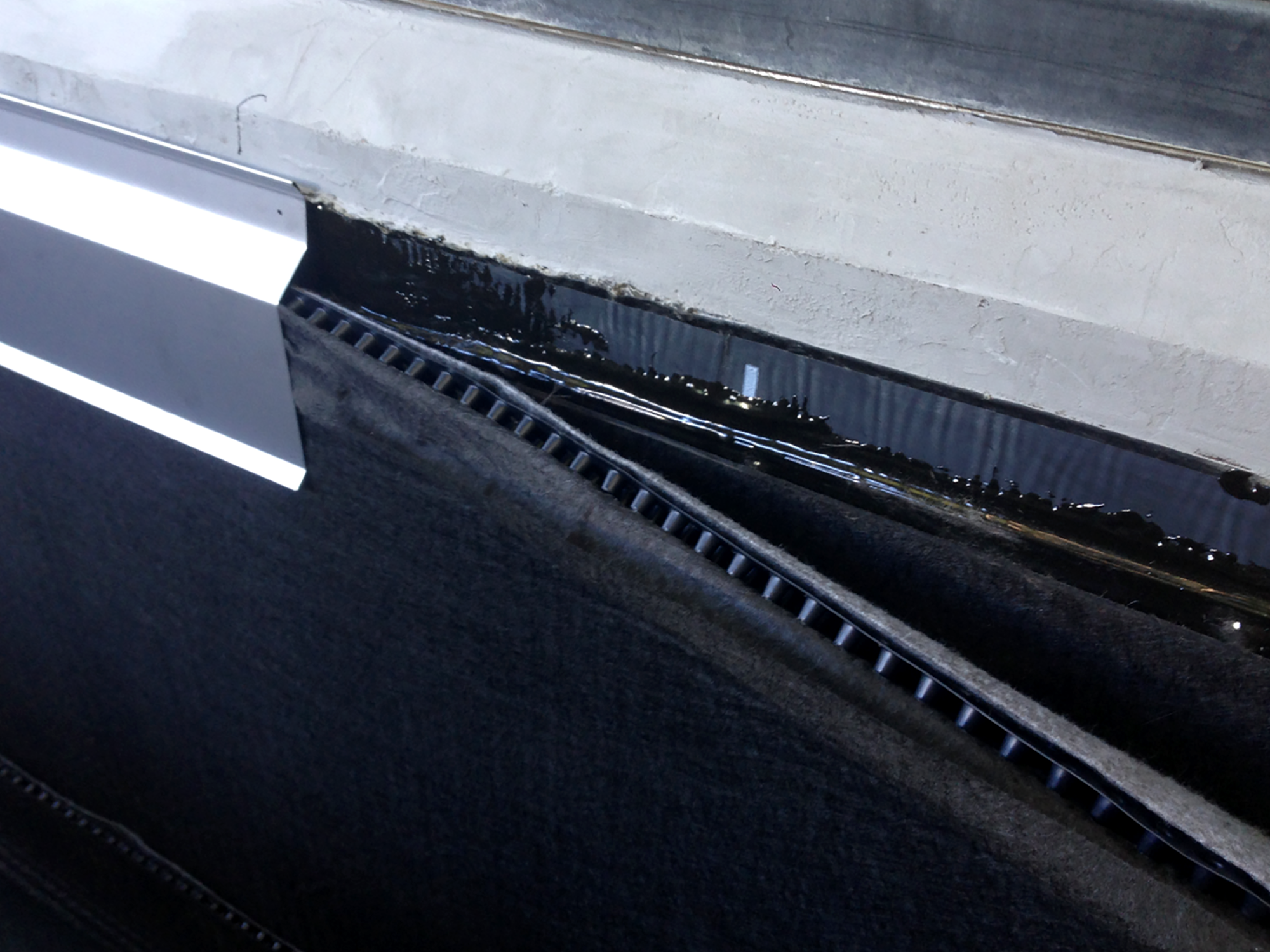
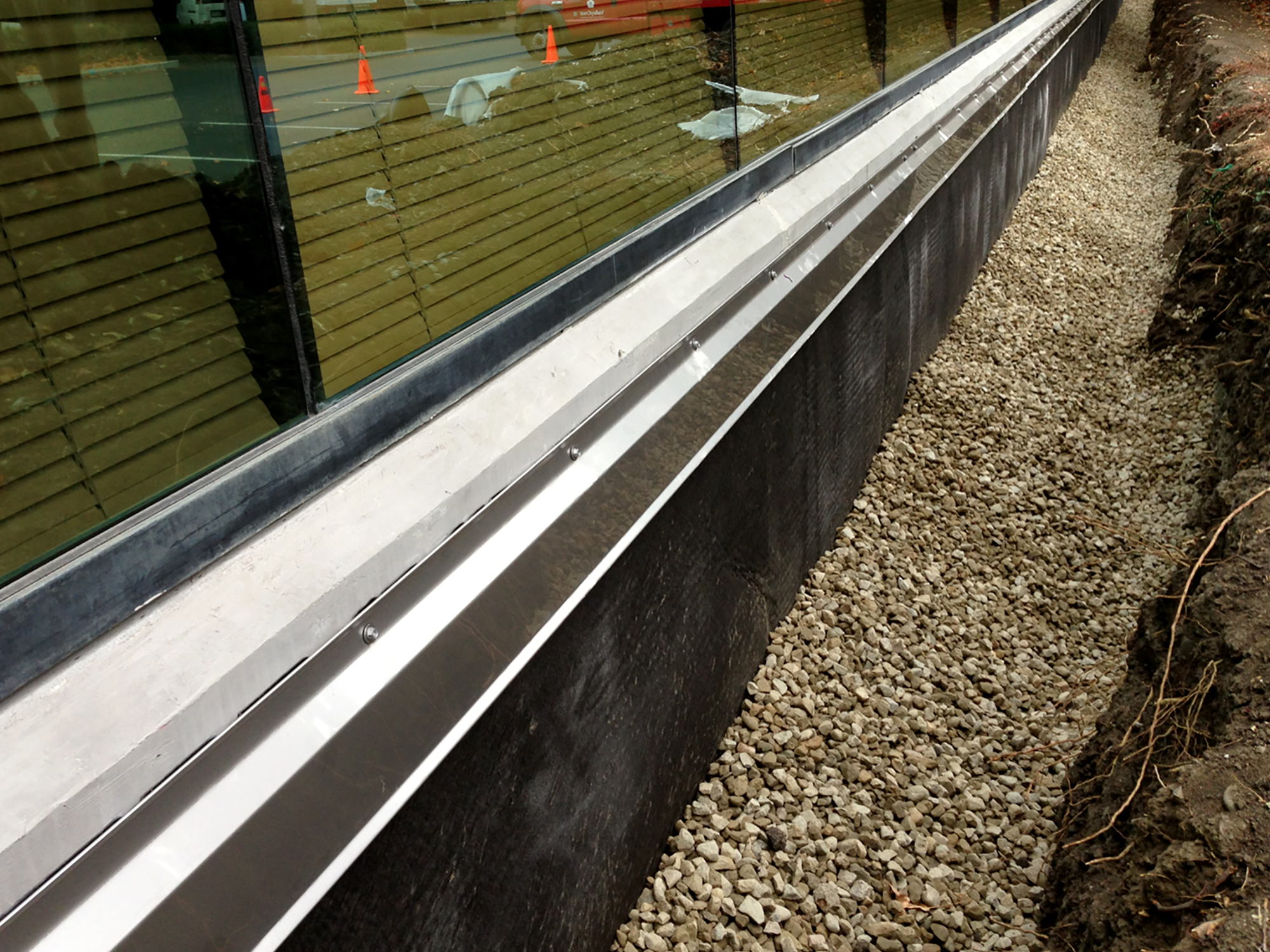
What We Did
Simpson Gumpertz and Heger designed a premium waterproof system consisting of sheet membrane, drainage course, custom flashing, and silicone coating at exposed areas of the wall. Before soil was backfilled and new landscaping installed, new perforated drain pipe and crushed rock were installed in the bottom of the trench to provide drainage, along with pathways to divert water from the walls and daylighting to drains.
Excavated a 3'-deep trench and removed the existing failing coating.
Repaired cracks in the foundation
Completely resurfaced 3'-high foundation walls and applied skim coat for pristine new substrate.
Applied Bituthene sheet waterproofing, with termination bars top and bottom, encapsulated in Liquid Membrane
Covered all with Hydroduct 500 drainage course, capping with custom-fabricated stainless steel flashing.
Caulked window perimeter at the base of storefront windows and coated exposed walls with Dow All Guard silicone elastomeric coating.
Project Details
It is critical, if you have bermed landscaping up against a building, to allow for proper drainage of water from rain or irrigation and also have a fully functioning waterproofing system to prevent water intrusion from wet soil pressed against the foundation. Leaks in these areas take a long time to develop and present themselves, and they are often expensive to repair once discovered.
A large laydown area needed to be established for the many yards of soil that were excavated from the bermed landscaping against the wall. All remnants of the membrane had to be removed to prevent future bleed-through. Once the wall was exposed, workers used a combination of hand tools and grinders with facing wheels to remove the existing asphalt membrane.
Once down to bare concrete, the walls were ground again. Cracks were routed and caulked with Dow Corning 795 silicone sealant. After cure, the walls were skimmed over with a cementitious surface filler to provide a perfect substrate for the Bituthene sheet membrane. The walls were primed, and the sheets were applied in 8’ long sections. Bituthene Liquid Membrane was applied at all lap joints, and a special detail stripe and the 34 Liquid Membrane were used to detail conduit and plumbing penetrations.
Sheets were rigorously inspected for wrinkles, fishmouths, or any other imperfections. After all of those were repaired, the sheets were finished at the top and bottom with stainless steel termination bars, which were then encased in more Liquid Membrane. Then, a drainage course of Hydroduct 500 RS was applied and finally covered with asphaltic protection board.
This entire waterproofing, drainage, and protection course was capped with custom-fabricated and field-soldered stainless steel flashing. All sections of stemwall that were to remain exposed above grade were coated with Dow All Gaurd silicone elastomeric coating. The window sills were caulked with DowSil 795 to finally provide a complete, top-of-the line waterproofing system, top to bottom.
Want to know how we can help with your next project?