EIFS reintegration keeps elderly care residents dry and mold free
Sunrise Assisted Living
A national elderly care facility had a location in Sunnyvale and was suffering from water intrusion and coating failures at a number of their windows and building components. Urban was hired to install a custom repair to re-waterproof and integrate these elements into the building envelope waterproofing, saving very expensive window and flashing replacements.
Leaks at windows and other parts of the wall can allow water into the wall cavities, causing the water to harbor and eventually grow mold in the dark, damp conditions. This presents an obvious health hazard but also a tremendous logistical challenge if you have to relocate sensitive residents while remediating water and mold damage in their rooms.
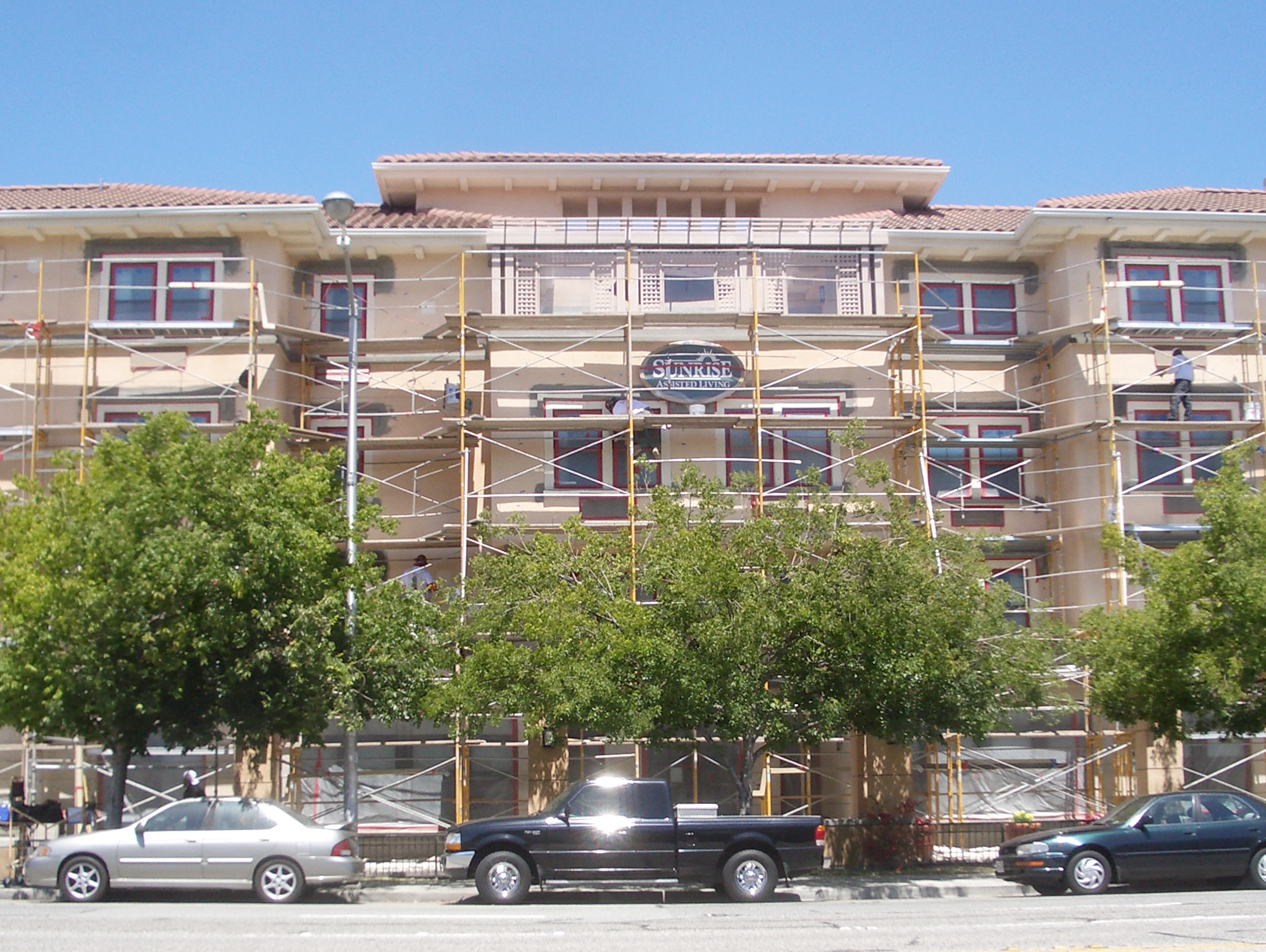
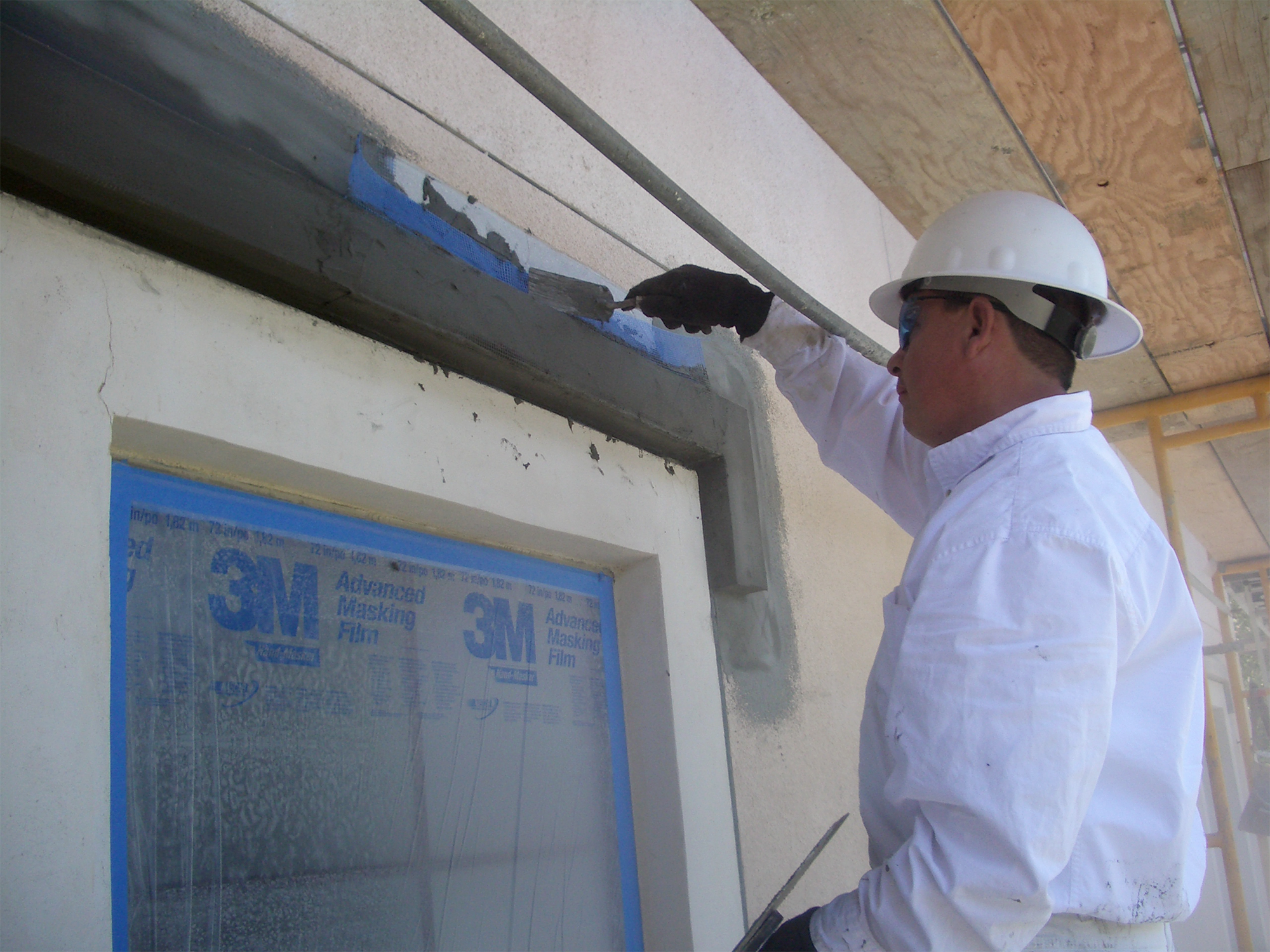
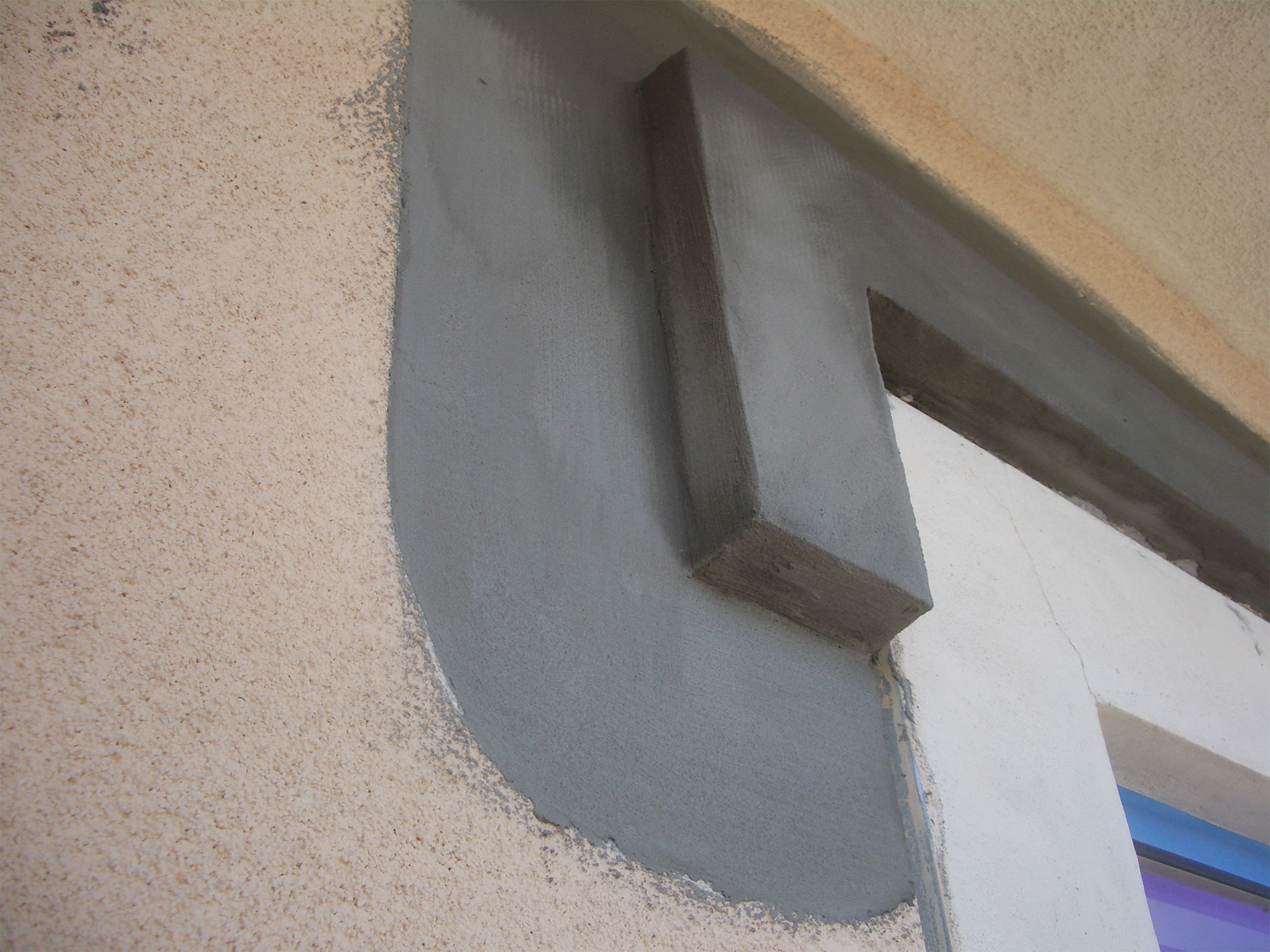
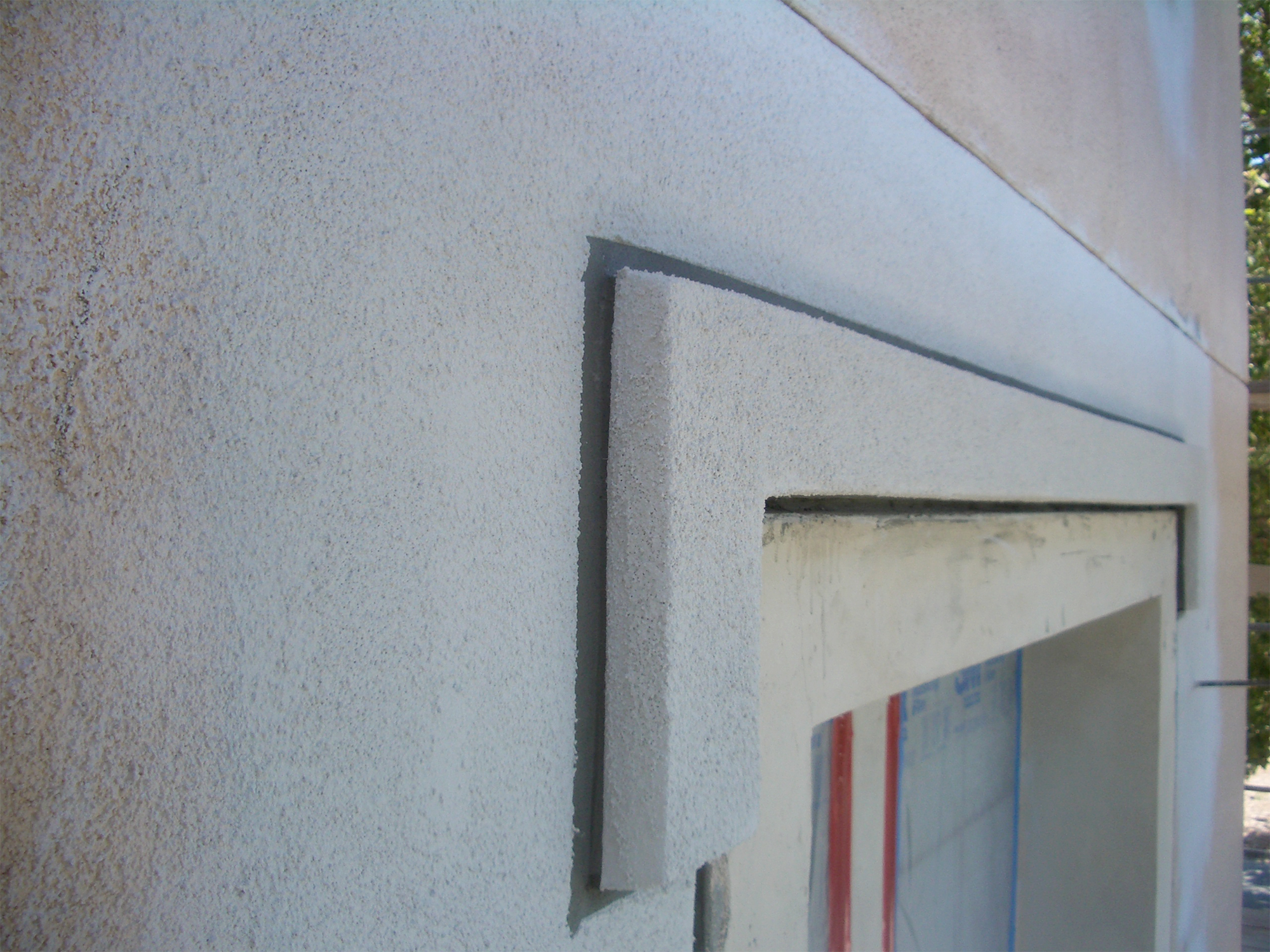
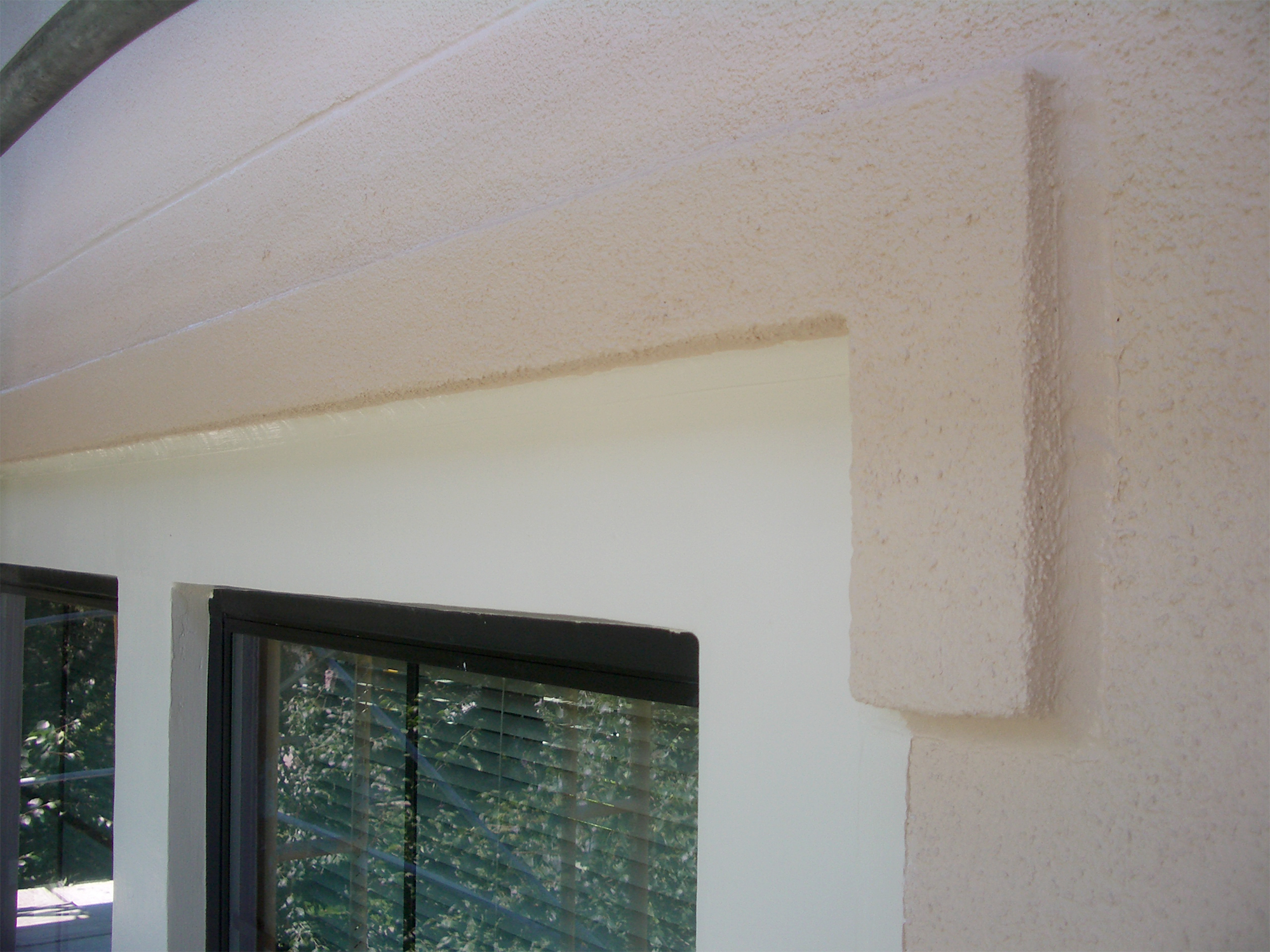
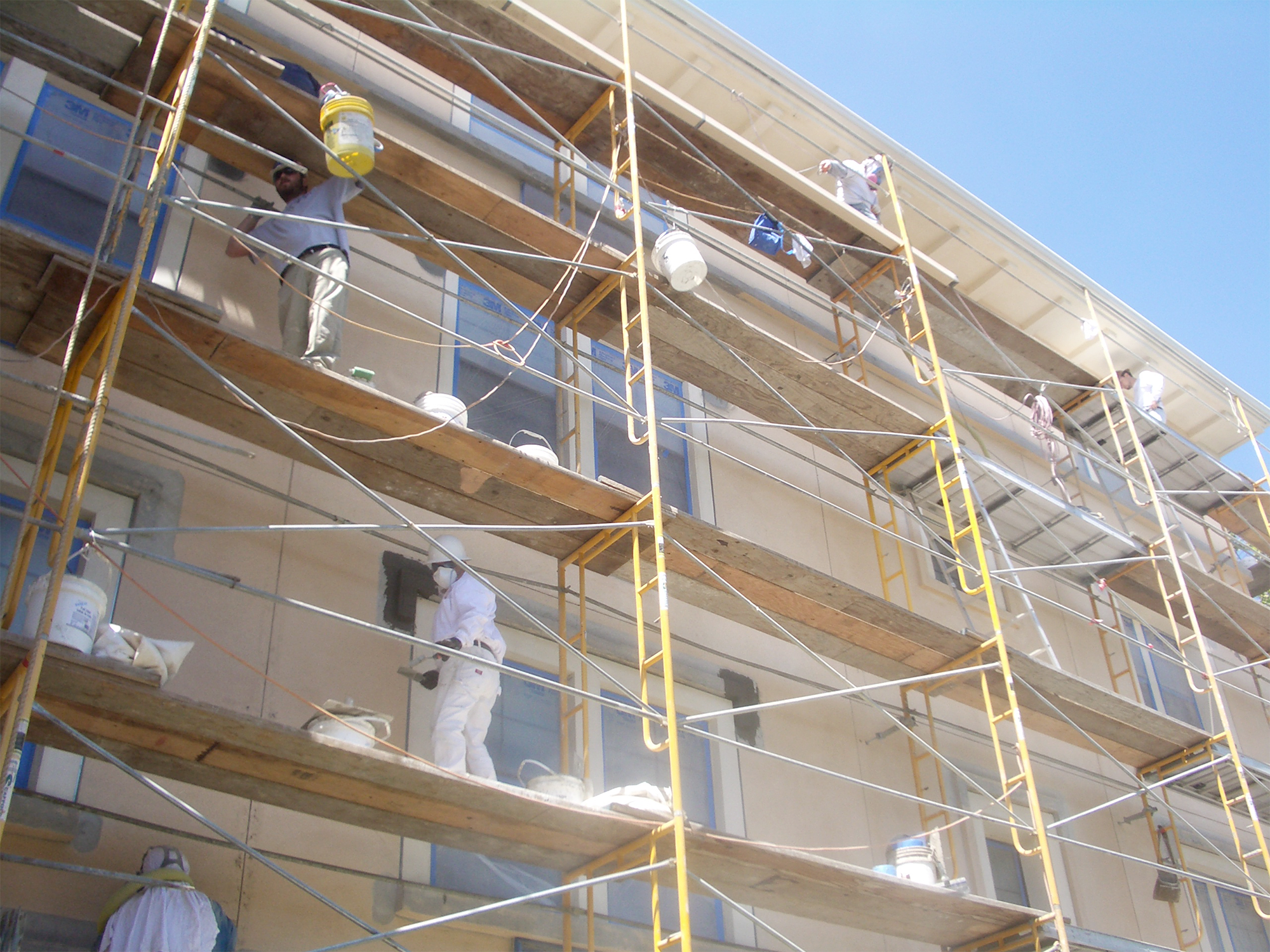
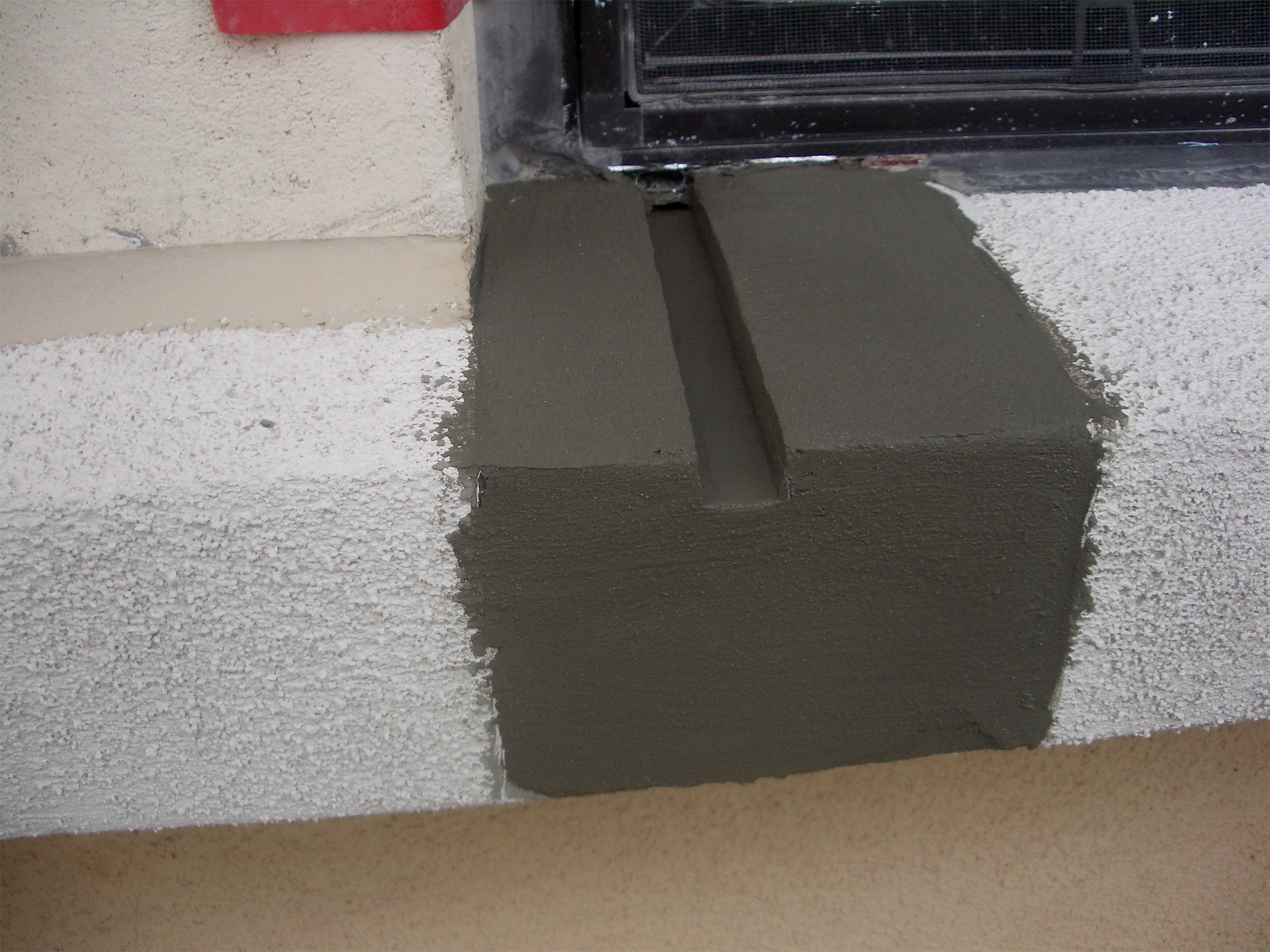
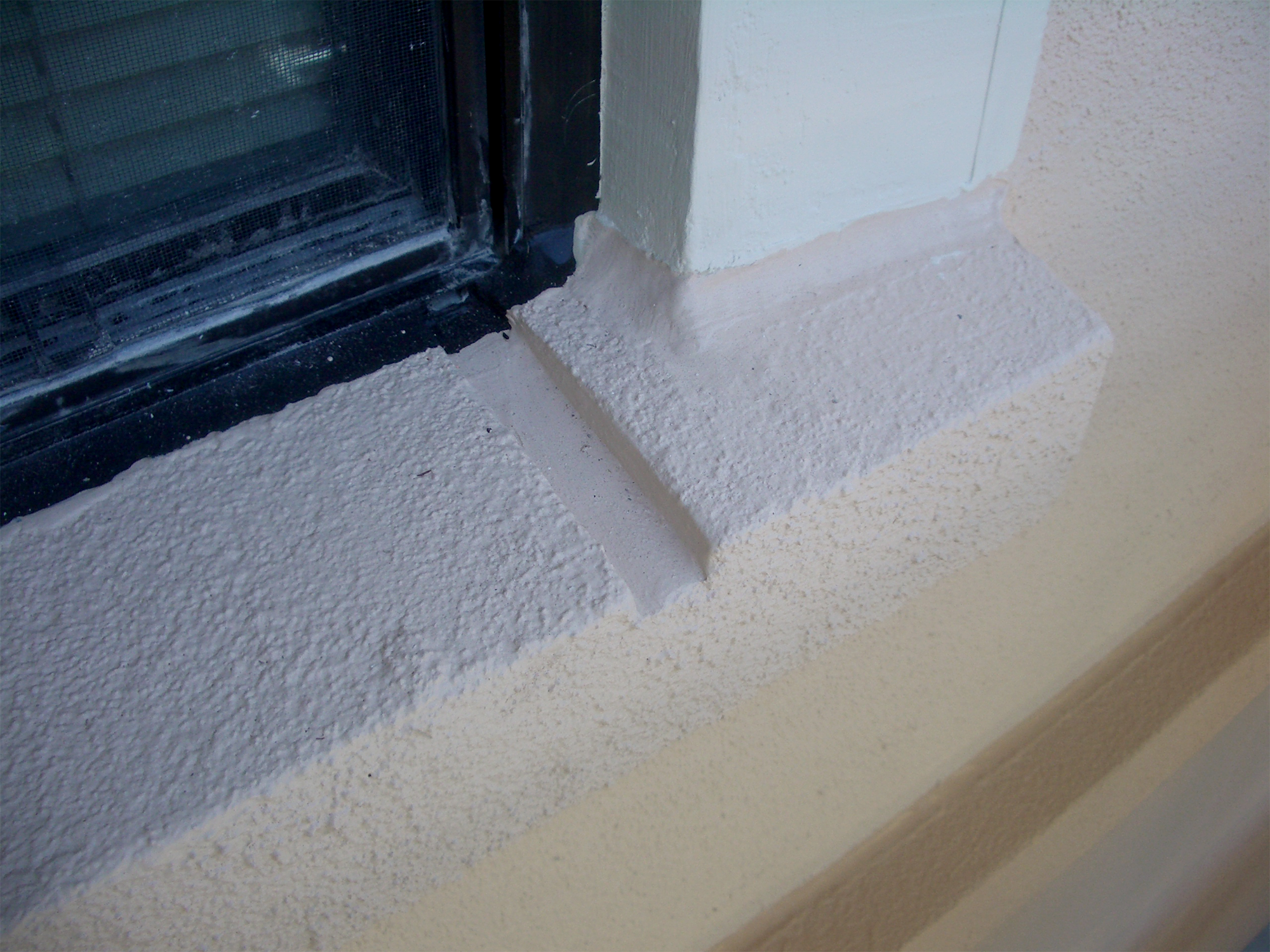
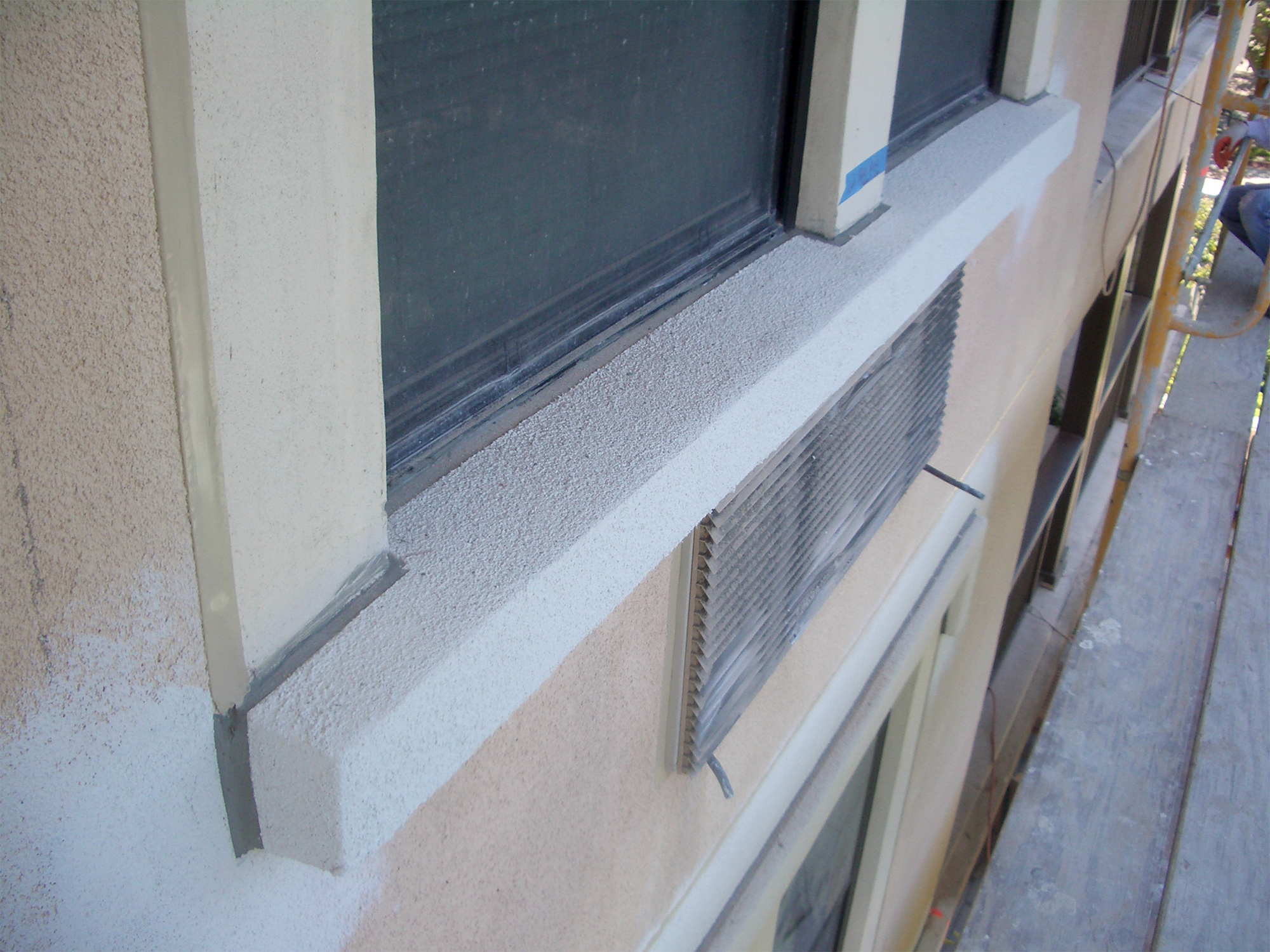
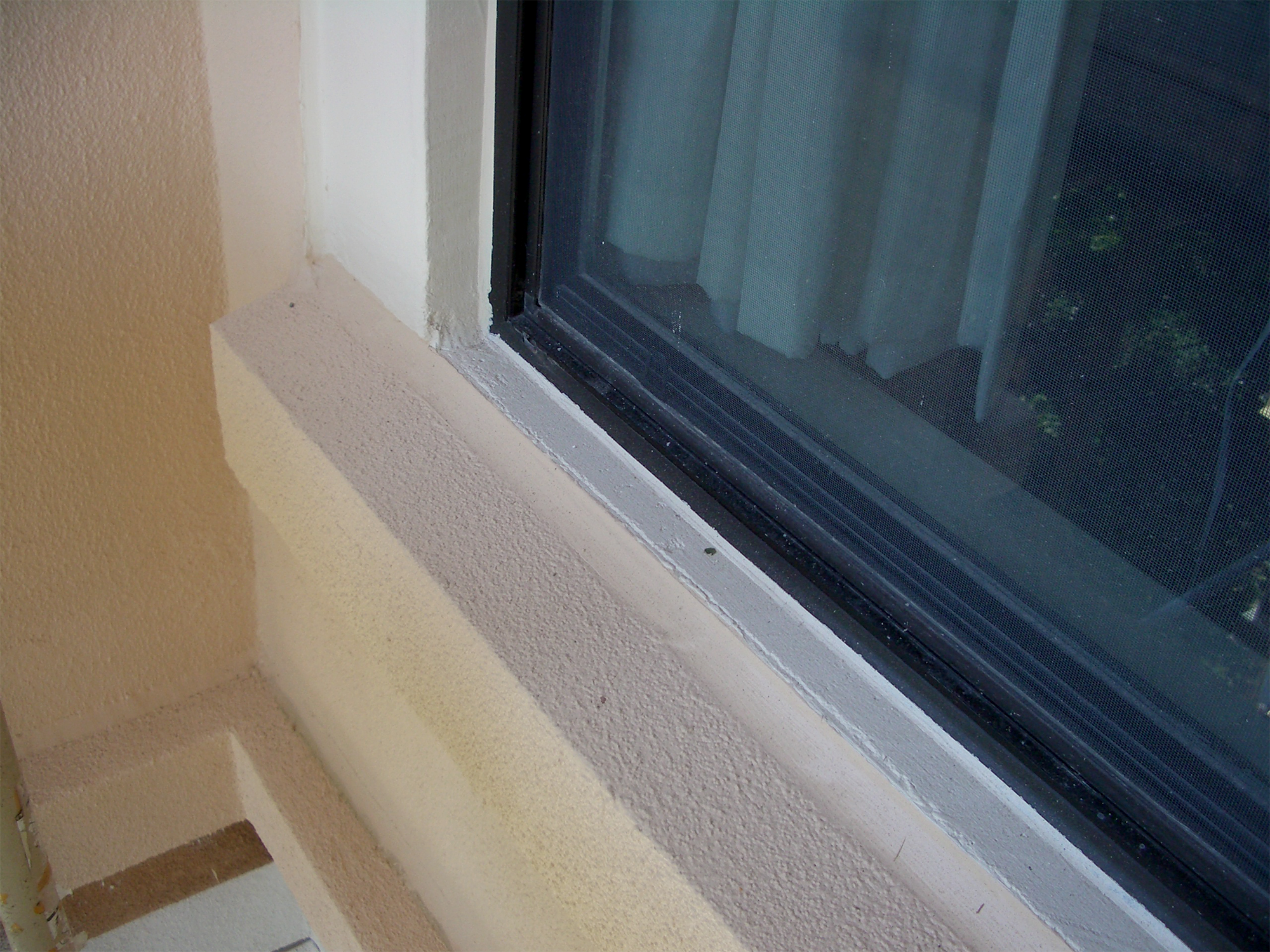
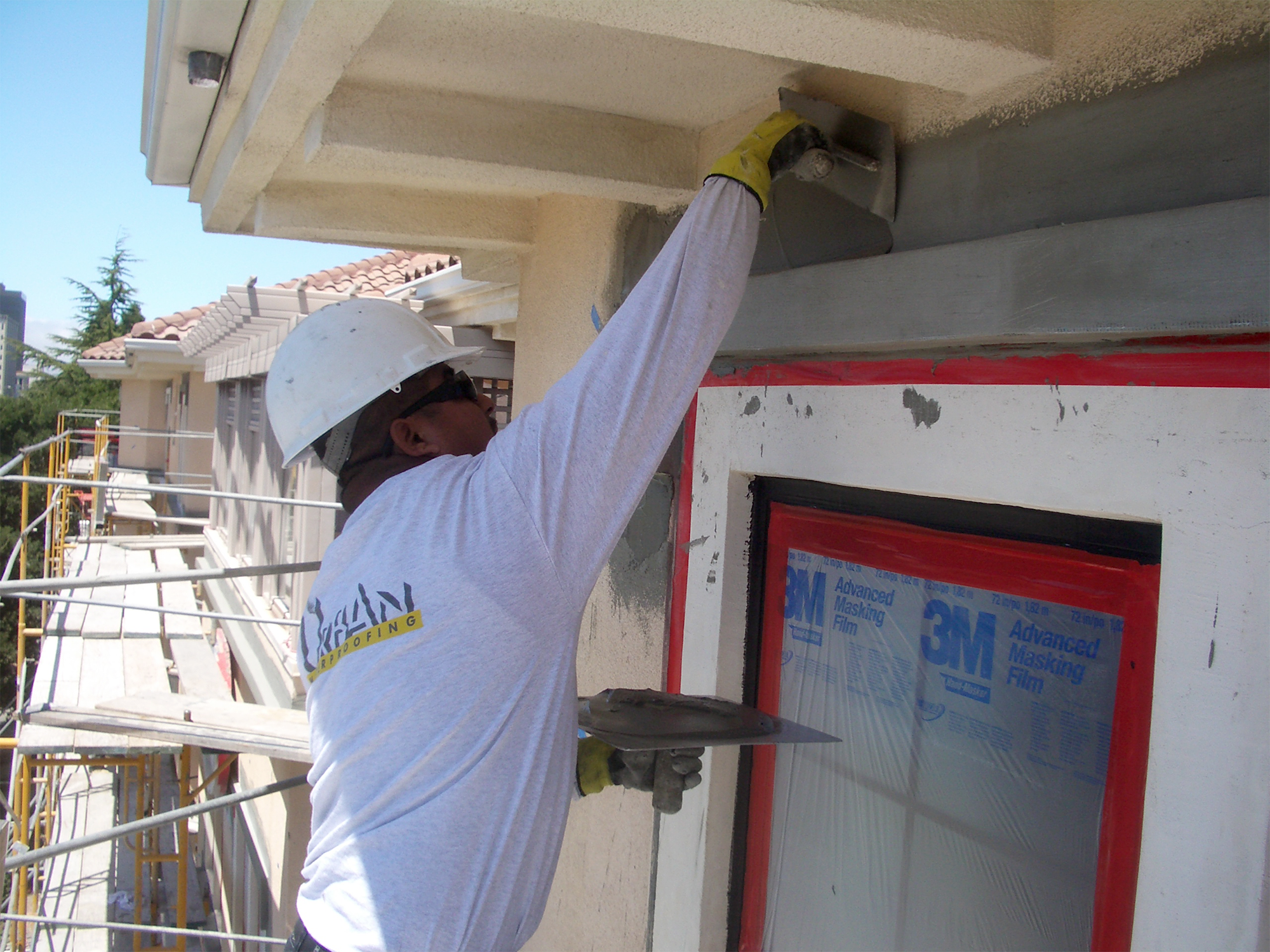
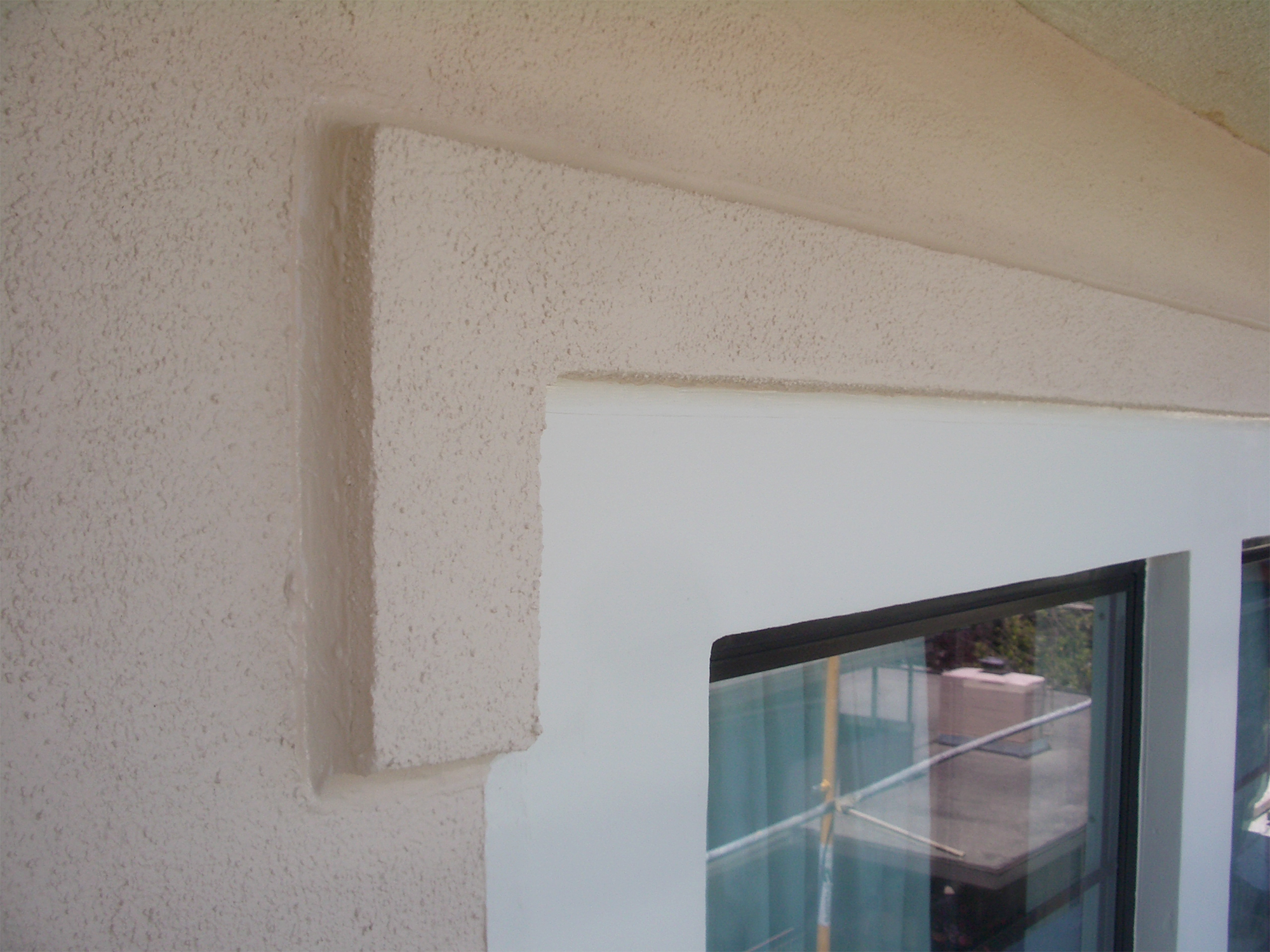
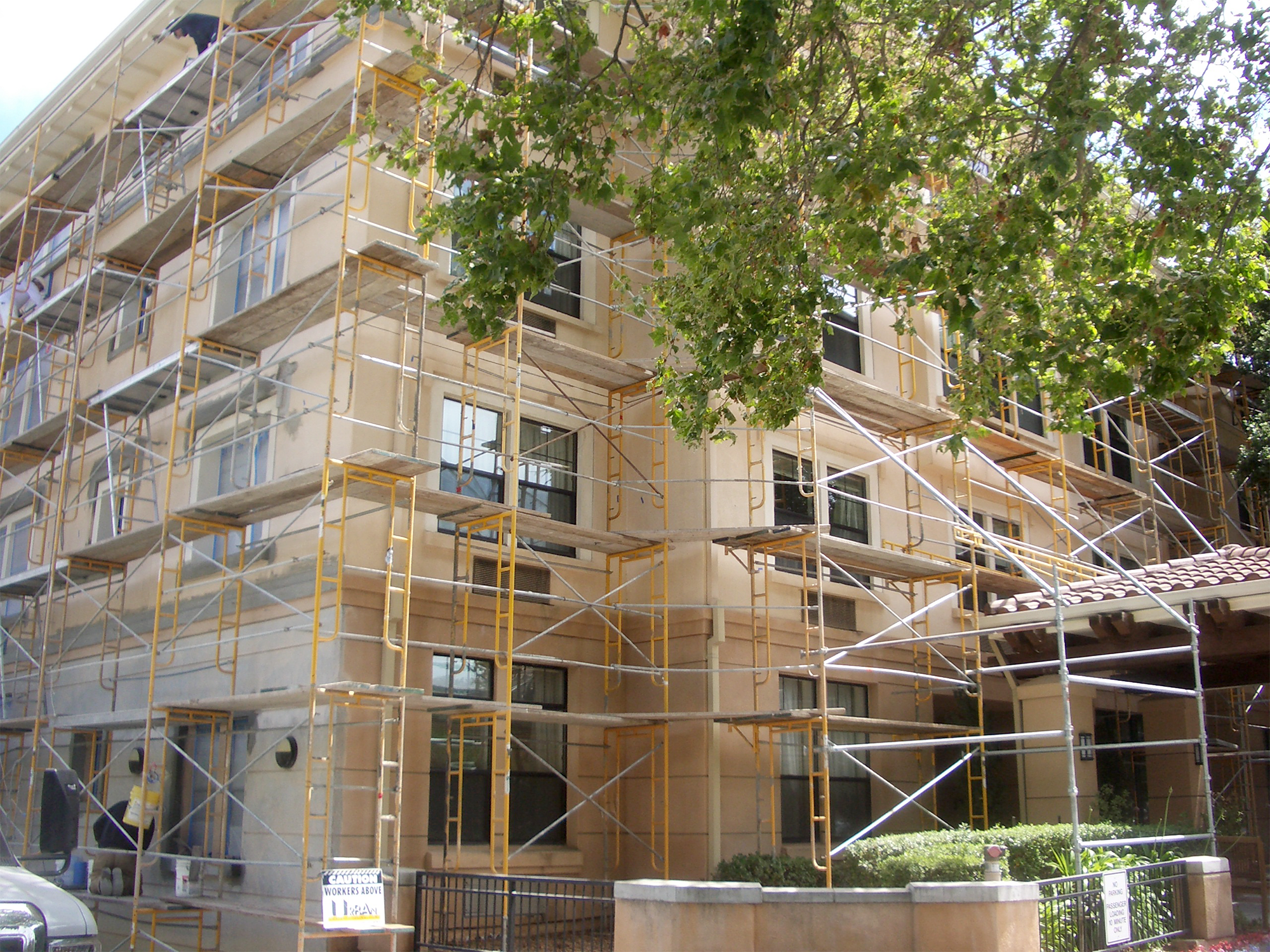
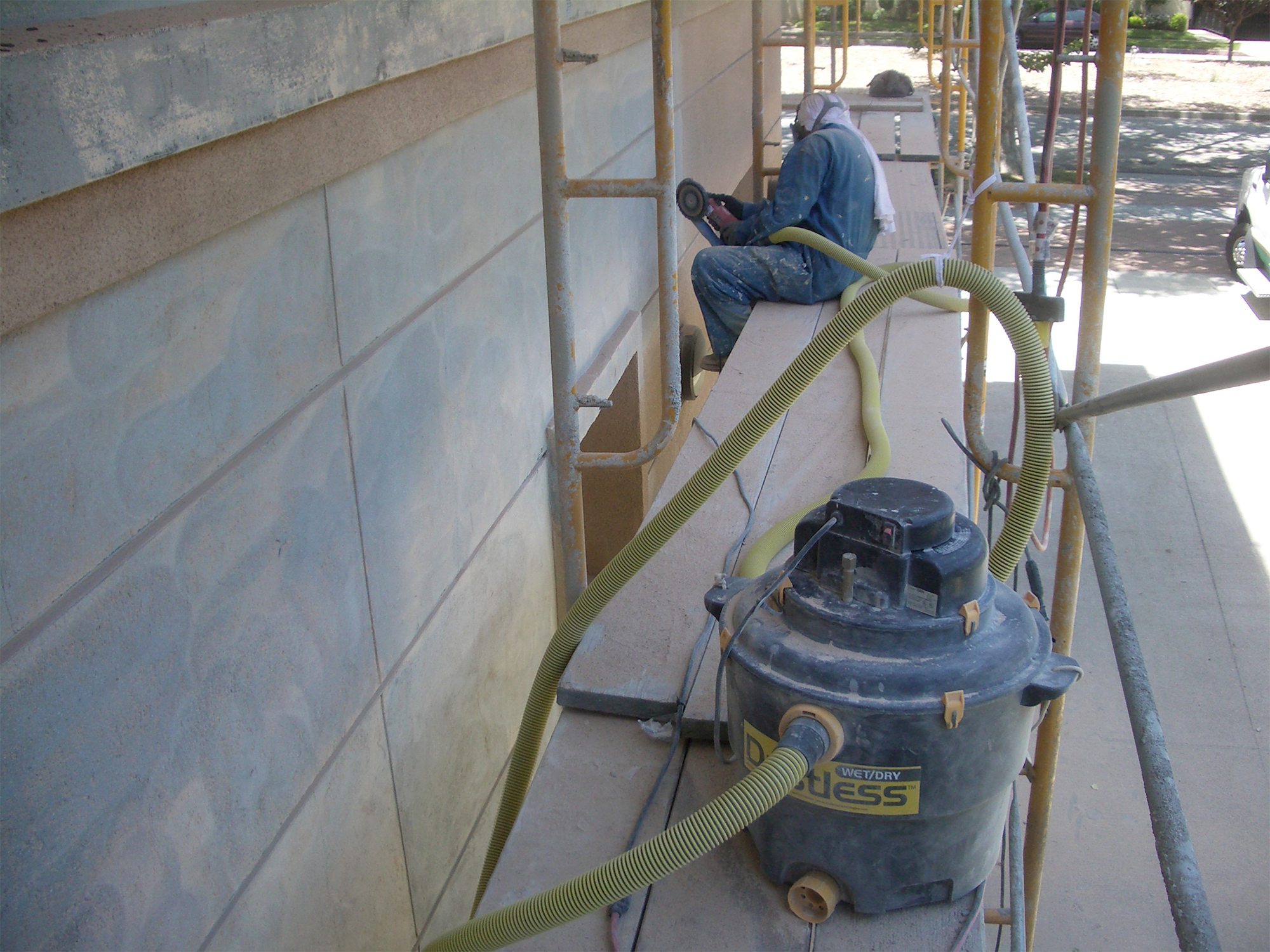
What We Did
Installed scaffold at all elevations of the 5-story building
Installed new EIFS lamina and topcoat at all window heads and ledges to re-integrate elements back into the wall.
Caulked all windows and ledges to restore waterproofing continuity.
Resurfaced two elevations of the wall where a previous stucco texture coat was systemically failing.
Field designed and installed custom drainage slots at window ledges where windows were set too low to provide drainage from weepholes.
coated the entire building with a Dow All Guard silicone elastomeric coating.
Project Details
Once the building was fully scaffoled and a safety plan to manage residents was in place, demo began to remove the finish coat and the first part of the basecoat at the top of all window head decorative EIFS plant-on elements and at all ledges. These foam plant-on elements were essentially stuck on when the building experienced a remodel, but they were not properly integrated with the existing stucco finish, and over time, cracks developed at all of these locations. Wiss Janney Elstner and Associates designed a repair to apply new EIFS mesh lamina, tying the plant-on pieces up onto the wall so that transition could be caulked and then encapsulated in an elastomeric coating for a flexible, waterproofing bond between the plant-on element and wall.
Each unit had an air conditioning unit that was leaking as well. We installed custom drainage ports and caulked the basin edges that held the AC unit to create a small tub. We had to adjust the angle of the basin / tray to make sure water was directed towards the drain ports.
Two entire elevations had sections of the stucco finish that were failing under simple adhesion tests. At some point, those were possibly refinished with a color coat that was not bonding to the substrate underneath. We had to remove all of that failed coating using grinders with vacuum attachments, then we primed the walls and applied a new texture coat to match.
With the plant resurfaced and integrated with the wall, caulking was applied as an added protective measure, along with new caulking at the complete window perimeters. The walls were coated with Dow Corning All Guard, providing a beautiful and fully waterproof membrane.
Want to know how we can help with your next project?