From failed stucco drainage system to a unique working silicone barrier
2880 Stevens Creek Blvd.
A unique silicone barrier system prevents complete stucco replacement in professional buildings.
A three-story modern office building in San Jose had multiple leak issues with its stucco facade. Poor flashing integration, leaks at windows, and other issues made it a tough choice for the owner: to remove all the stucco and reinstall. This would be a very long, disruptive, and expensive undertaking if you went that route. Fortunately, Simpson Gempertzx and Heger designed a repair that would transform a failed drainage system design into a functioning barrier system, sparing the cost and business disruption of re-doing the stucco.
Stucco and similar drainage systems are great options and provide an aesthetically pleasing look when working well. But drainage systems rely on the meticulous installation of flashing and drainage pathways; missed or out-of-order lapping of the flashing elements can direct water INTO the building instead of away. Water harbored inside the wall cavity can pose health hazards for occupants and damage expensive interior finishes.
The design repair called for custom extruded silicone tape to bridge over all of the reveals in the stucco system. All control joints were caulked. All window perimeters were caulked, and all windows were wet sealed, including butt joints. In addition, new saddle flashings were installed where balcony walls met the building walls. In addition to the walls, a new coping system was installed at the top of the wall / parapet, including new blocking and waterproof membrane below the new custom coping system to top off the new barrier system.
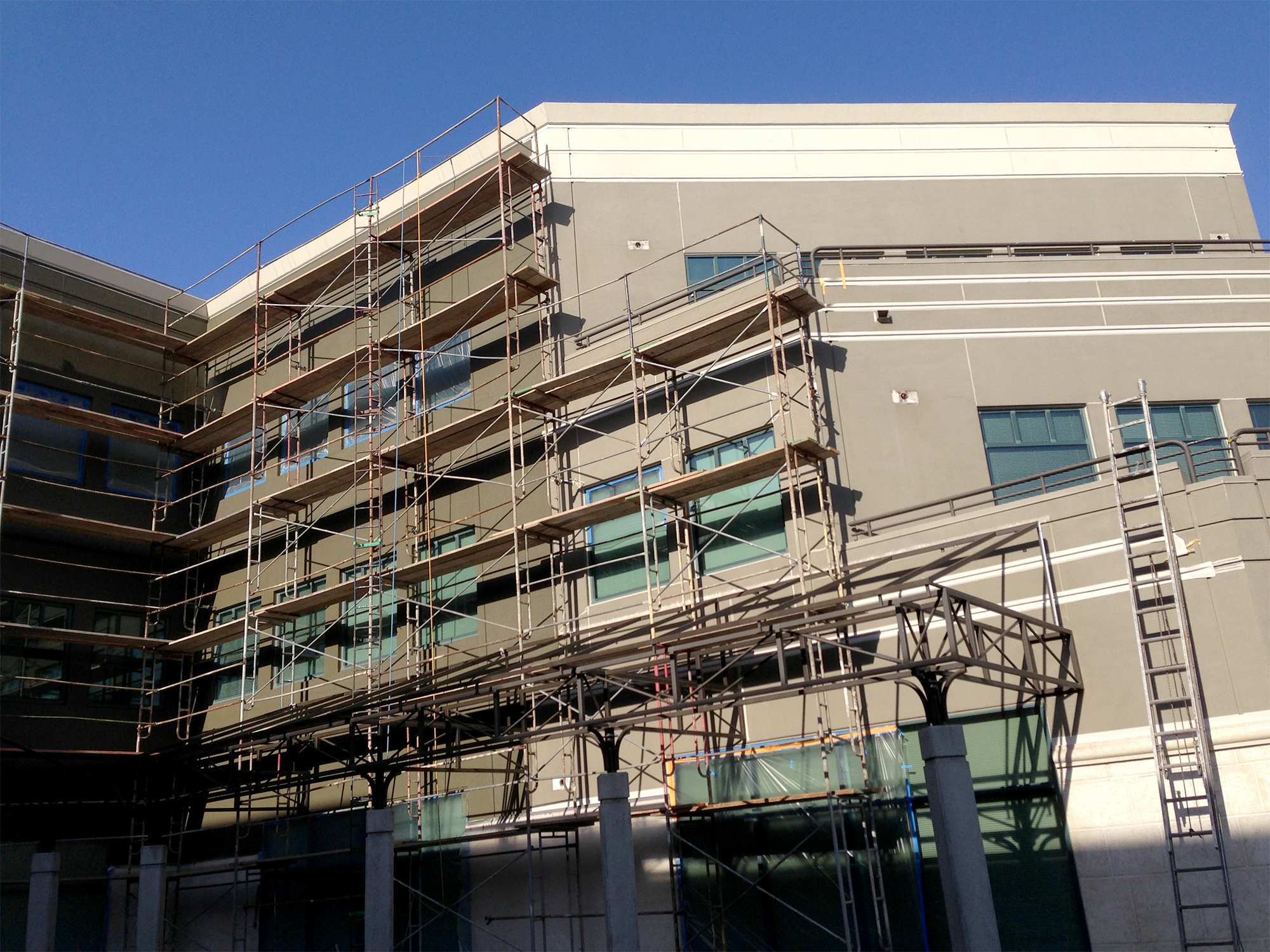
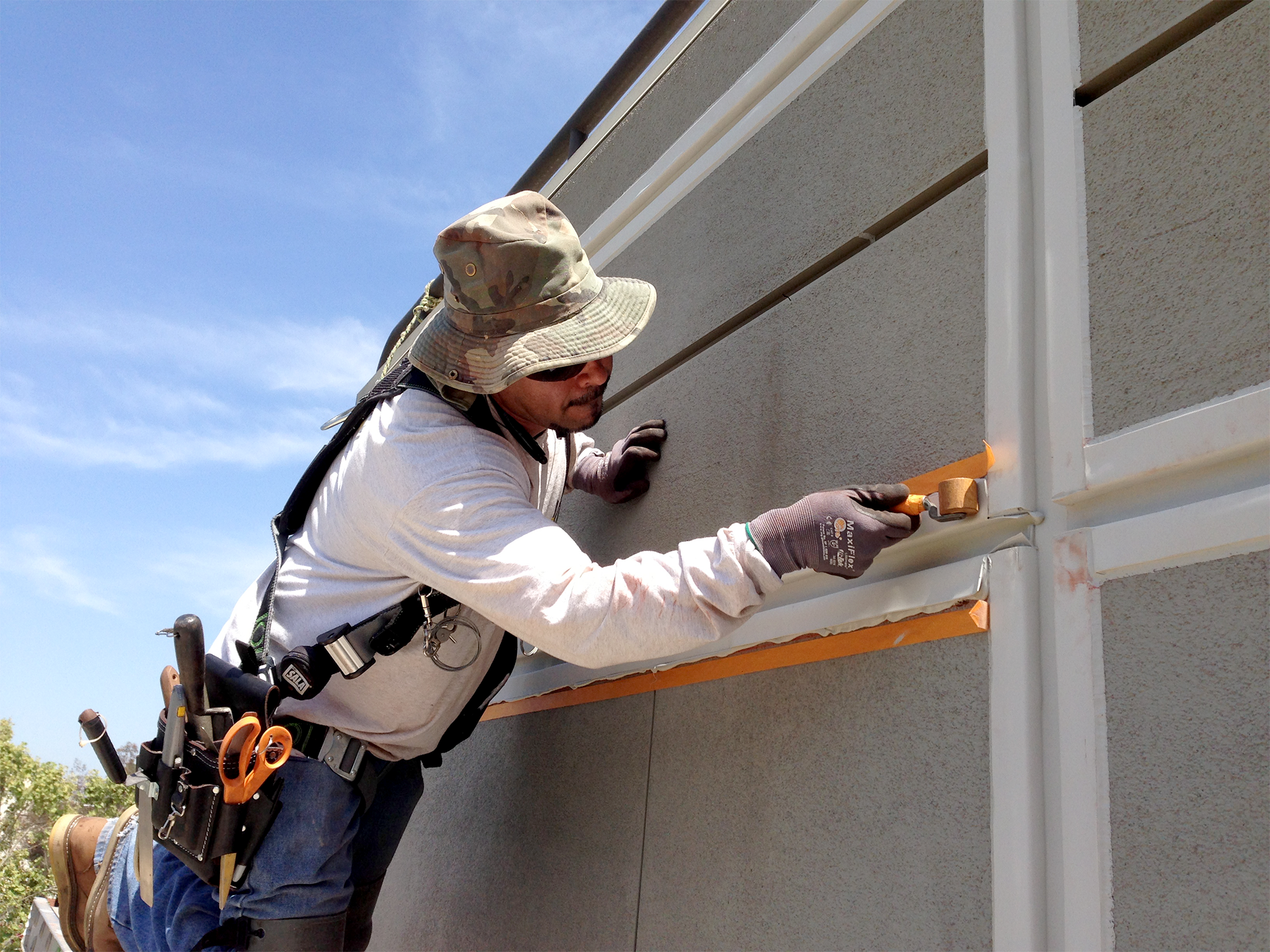
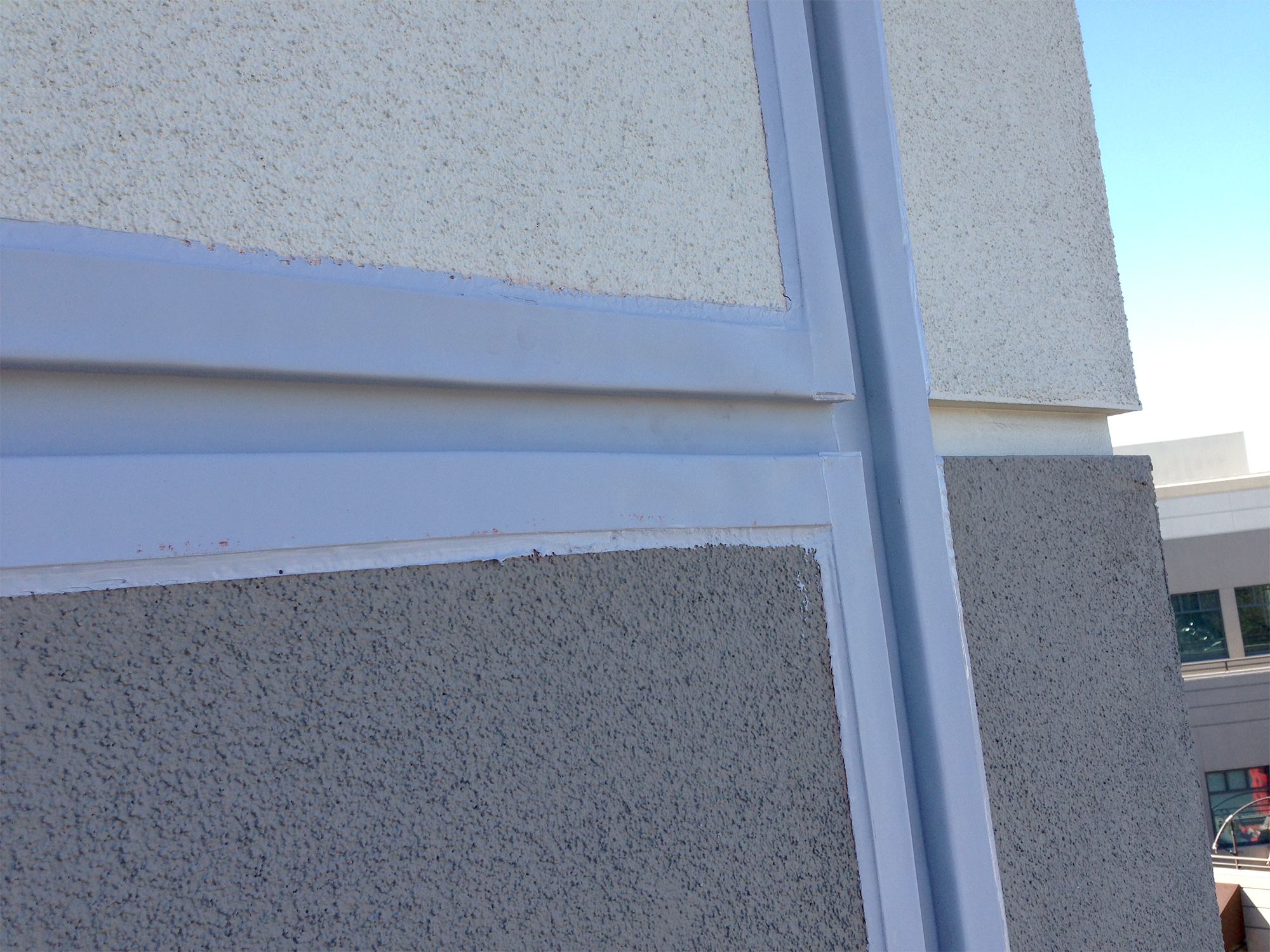
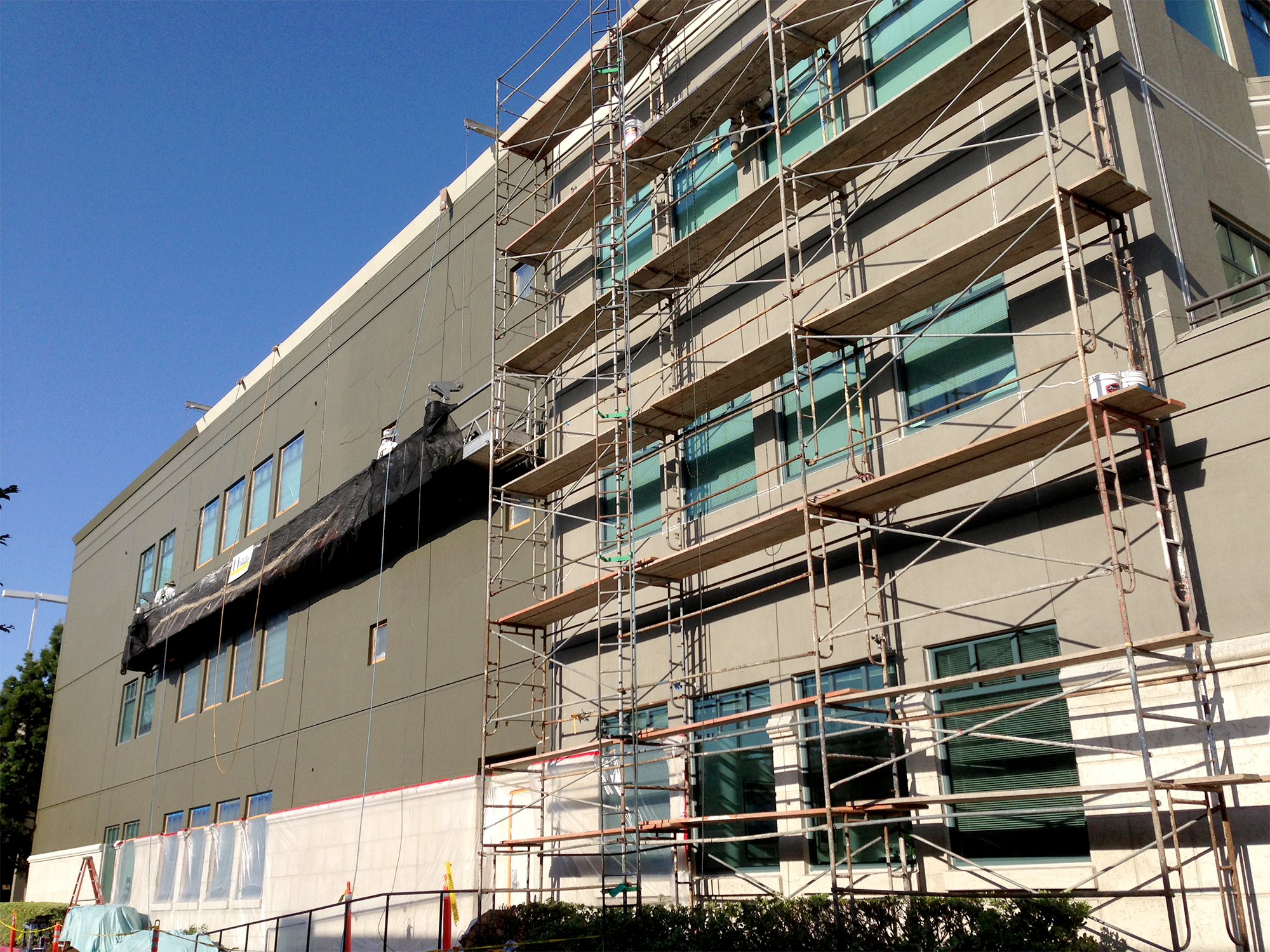
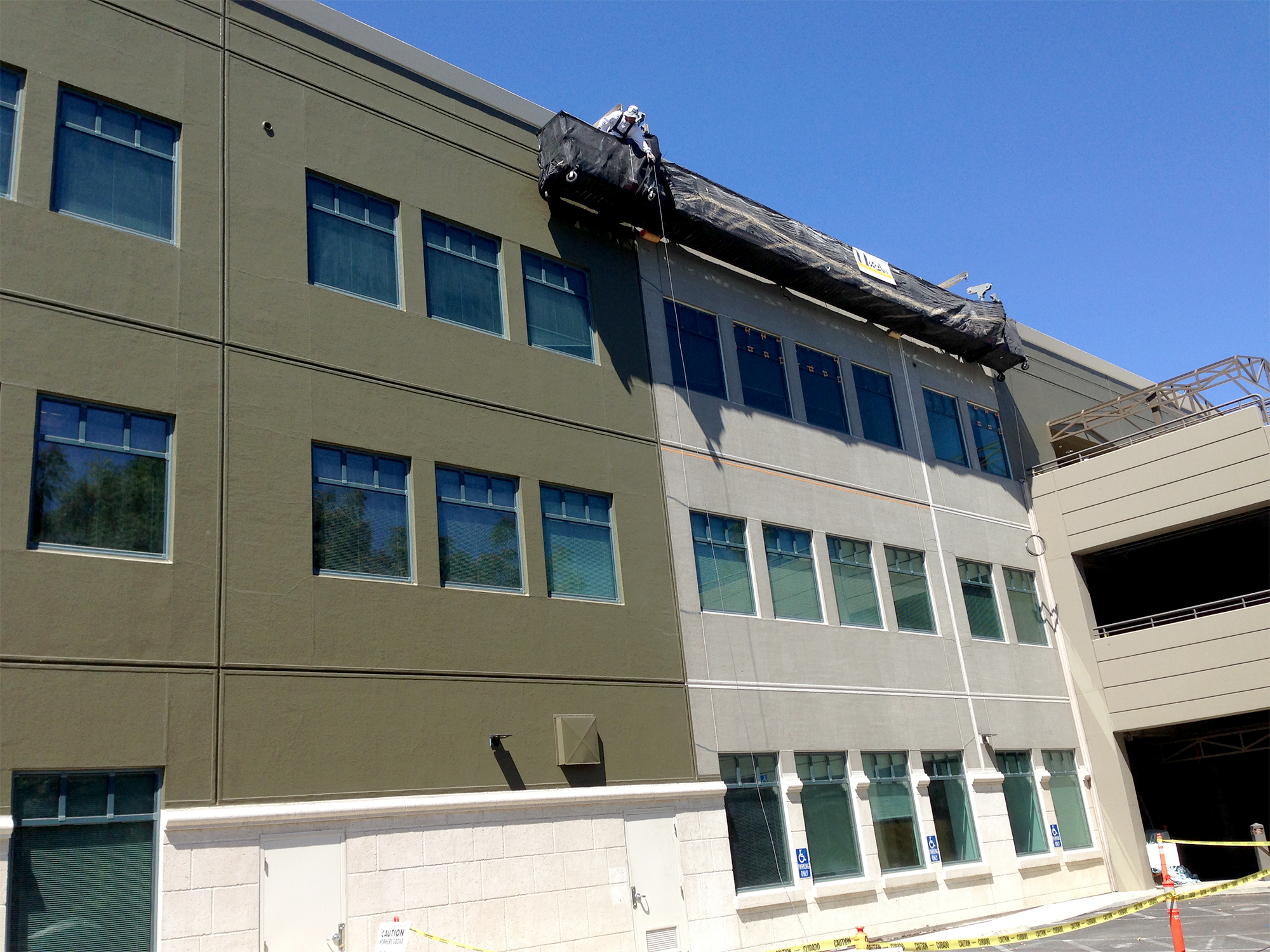
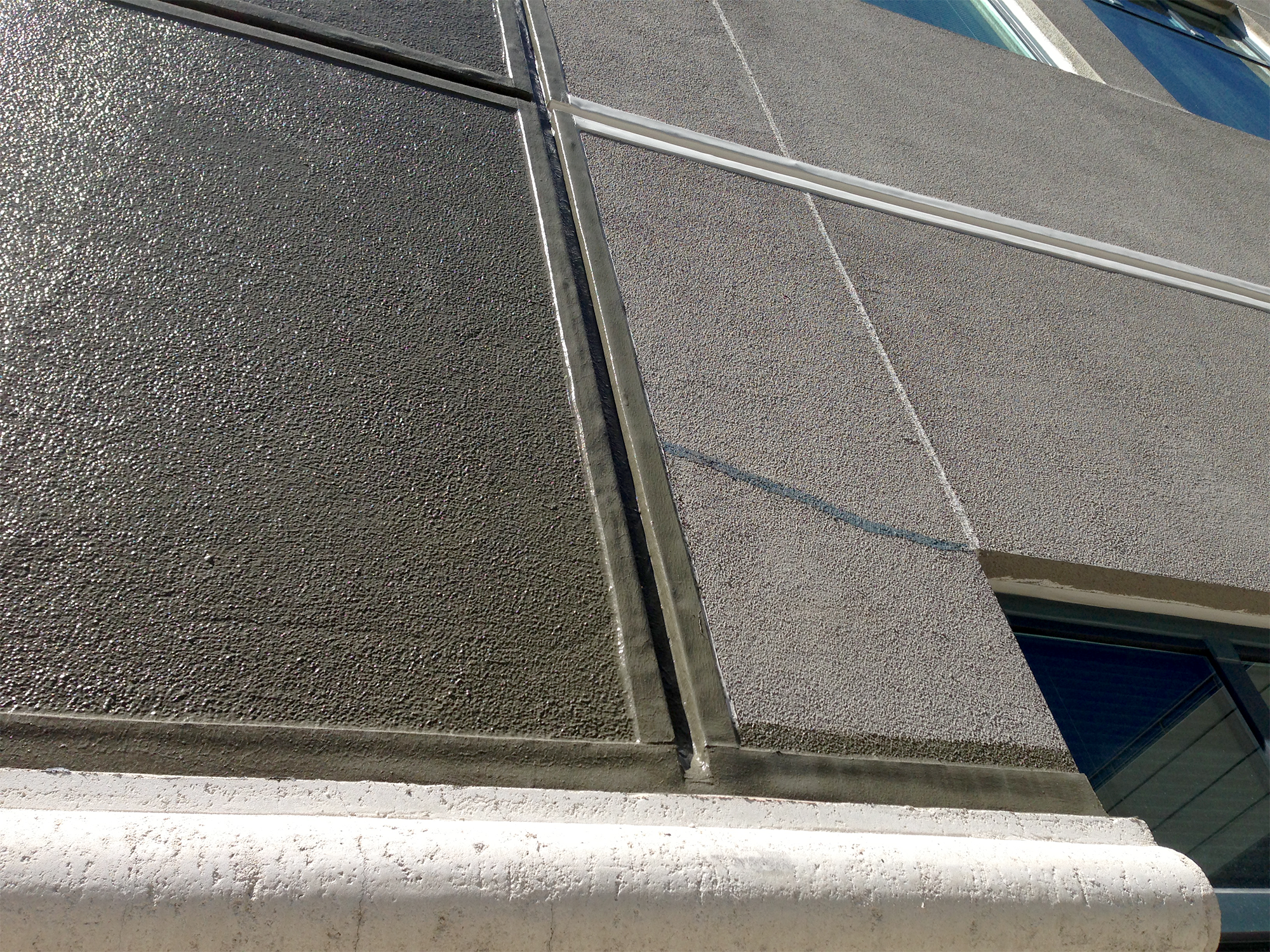
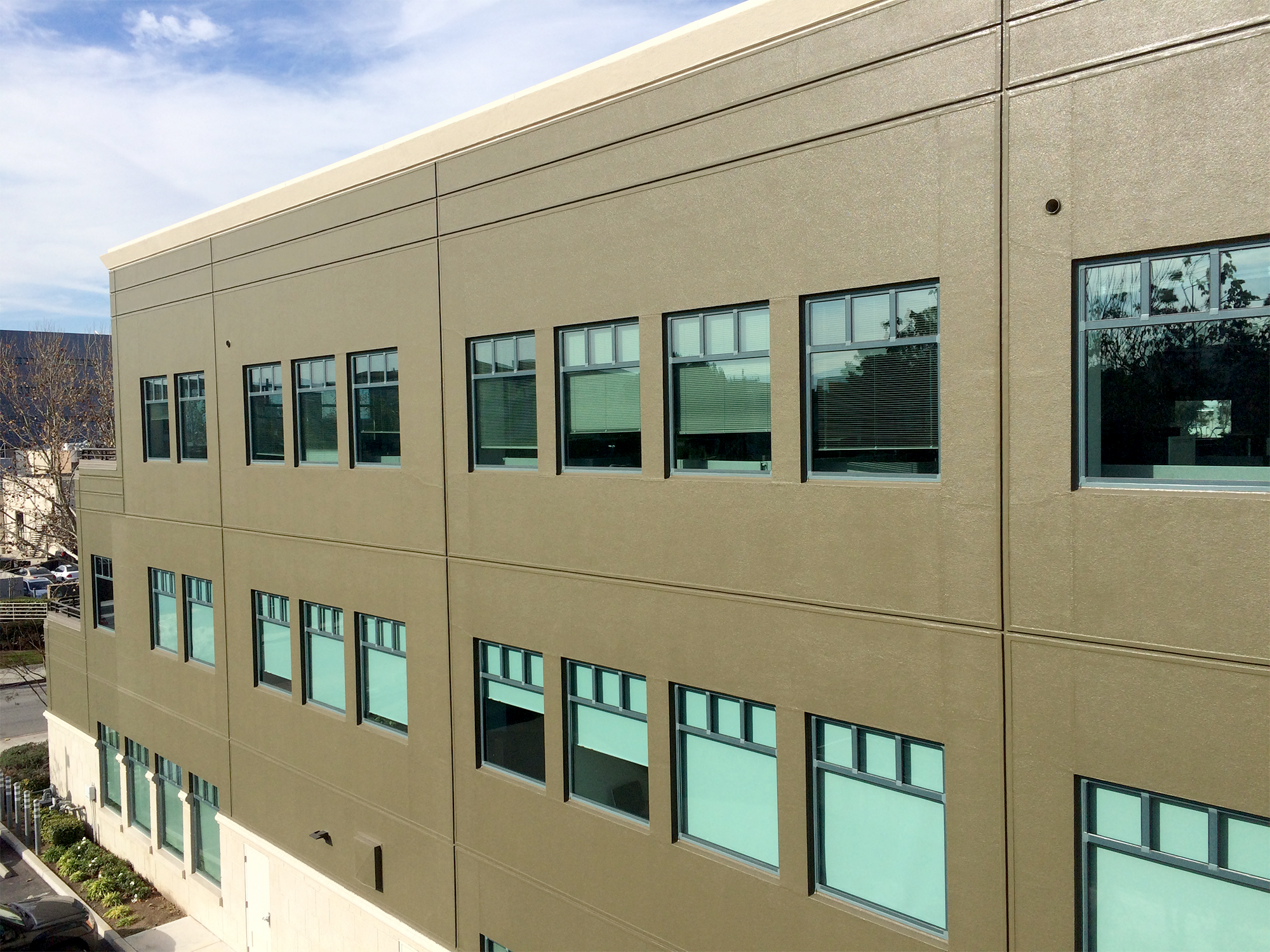
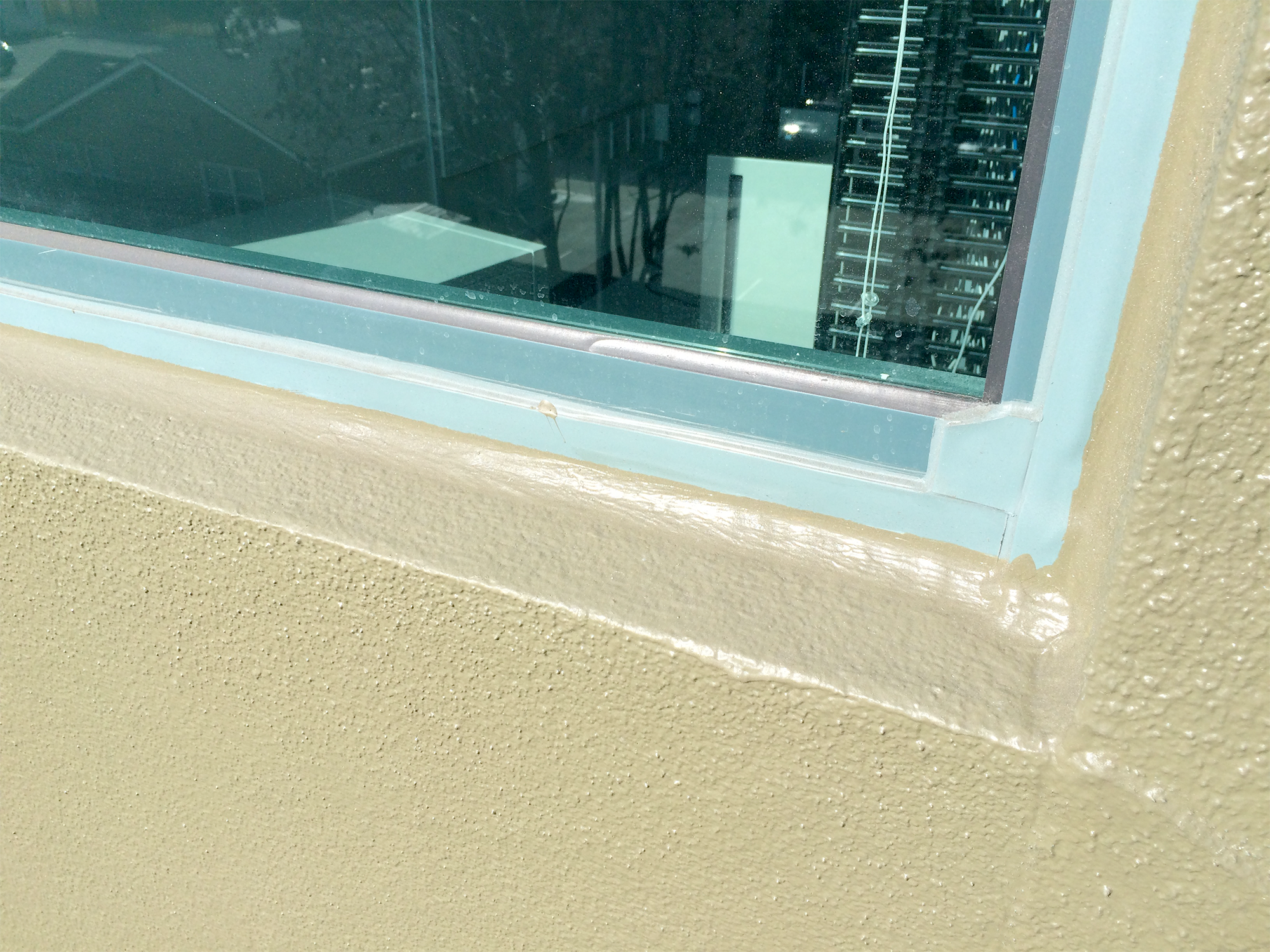
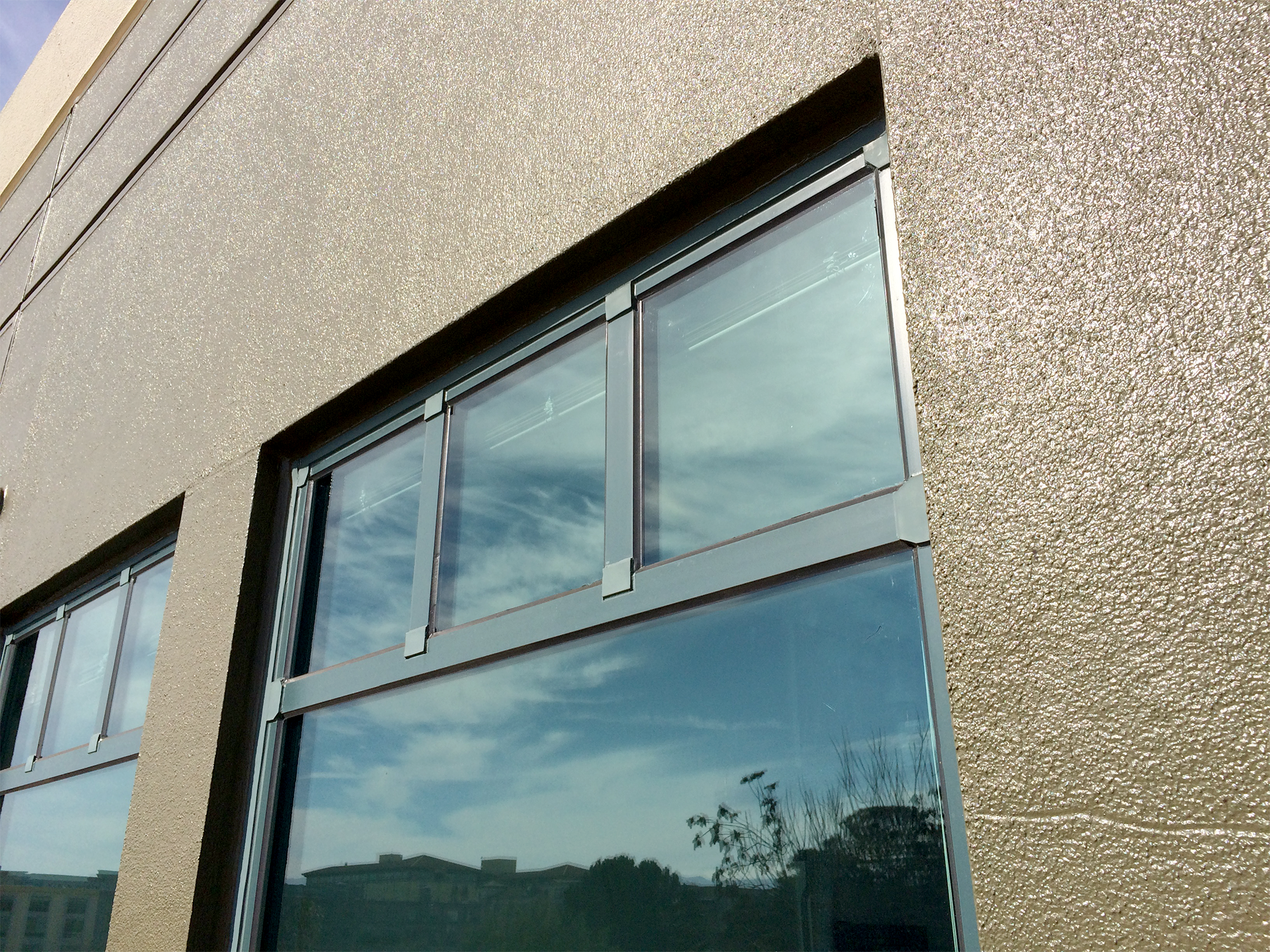
What We Did
Installed a combination of scaffold and swingstage at all elevations and worked while the building was fully occupied.
Recaulked all windows and openings fully—perimeters and wetseals
Installed custom silicone extrusions over building reveals / expansion joints to bridge systemic cracks
Coated walls with Dow All Gaurd silicone elastomeric coating.
Repaired cracking in stucco panels
coated the entire building with a Dow All Guard silicone elastomeric coating.
Project Details
The filed of the stucco was generally not the problem; it was everywhere the stucco started and stopped. To remedy this, all of those locations were bridged by custom-fabricated silicone extrusions. This ensured that no water would bypass these areas. With the thickness of the silicone tape and two coats of elastomeric, that is a repair designed to last a VERY long time.
All windows need to be fully waterproofed, too. Existing sealant on the window perimeters was removed, and joint cavities were grounded and prepared for new silicone sealant. Old, tired window gaskets were cut out and new silicone wetseal installed. This is a twenty-year system. At one of the other failure points, the saddle flashing from the balcony walls to the main wall, 14 new custom saddle flashing pieces were fabricated and installed, with the stucco removed first to allow for proper integration with the wall.
With all vulnerable connection points rebuilt and waterproofed, the walls were finally washed, prepped, and coated with two coats of Dow All Guard silicone elastomeric coating to tie it all together for an impervious, waterproof outer membrane.
Want to know how we can help with your next project?