22 story high-rise sealant joint replacement in high traffic plaza
Market Center
In the heart of SF’s financial district, Market Center consists of a 22-story high-rise and a 7-story sister building, both clad in terra cotta panels. The sealant between every panel and at the window perimeters was original and in need of replacement. In addition, the glaze finish on the terra cotta panels was cracking and spalling in many locations, and the mortar joints between the large granite slabs at the building skirt were loose and falling out. The building was in need of a tuneup for its exterior waterproofing components. This was a very large project, with all elements combined, with the added layer of the safety challenge of performing all work while throngs of pedestrians walked below. A special tool-tie-off procedure was developed for all workers on the swing stage to ensure nothing dropped from the work platform down to pedestrians below.
Extensive building recaulking on this scale is not for everyone. Beside the meticulous craft needed to make sure all caulking elements are installed perfectly to meet performance standards, managing the safety program for a crew of 16 working from 8 swing stages, working 200 feet above a busy sidewalk, takes incredible focus.
The host of repairs were identified and designed by Wiss Janney Elstner and Associates and installed in two phases, spanning over one year, without a significant safety incident. Every inch of the 200,000 lf of sealant was carefully inspected and tested regularly for proper adhesion.
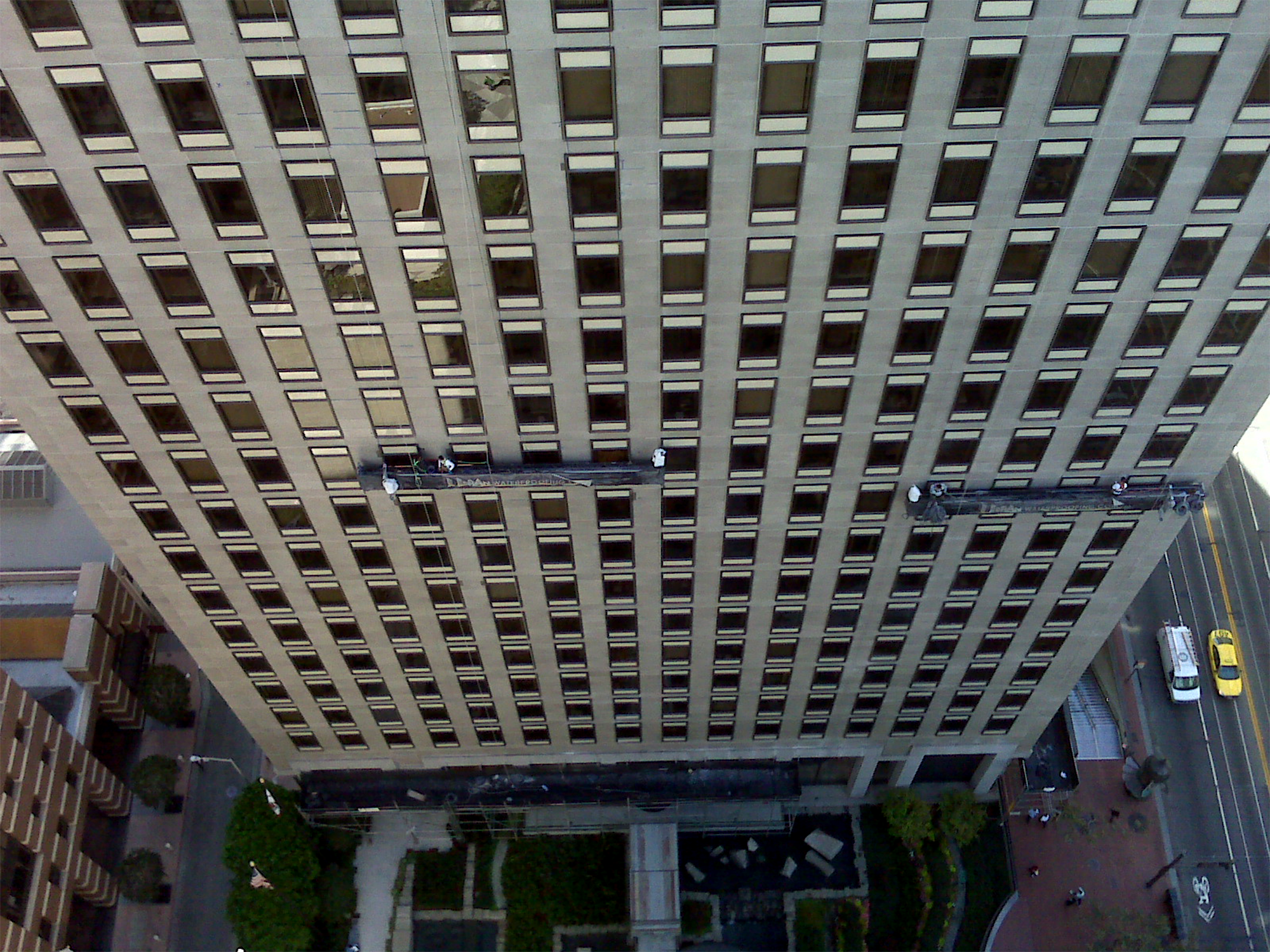
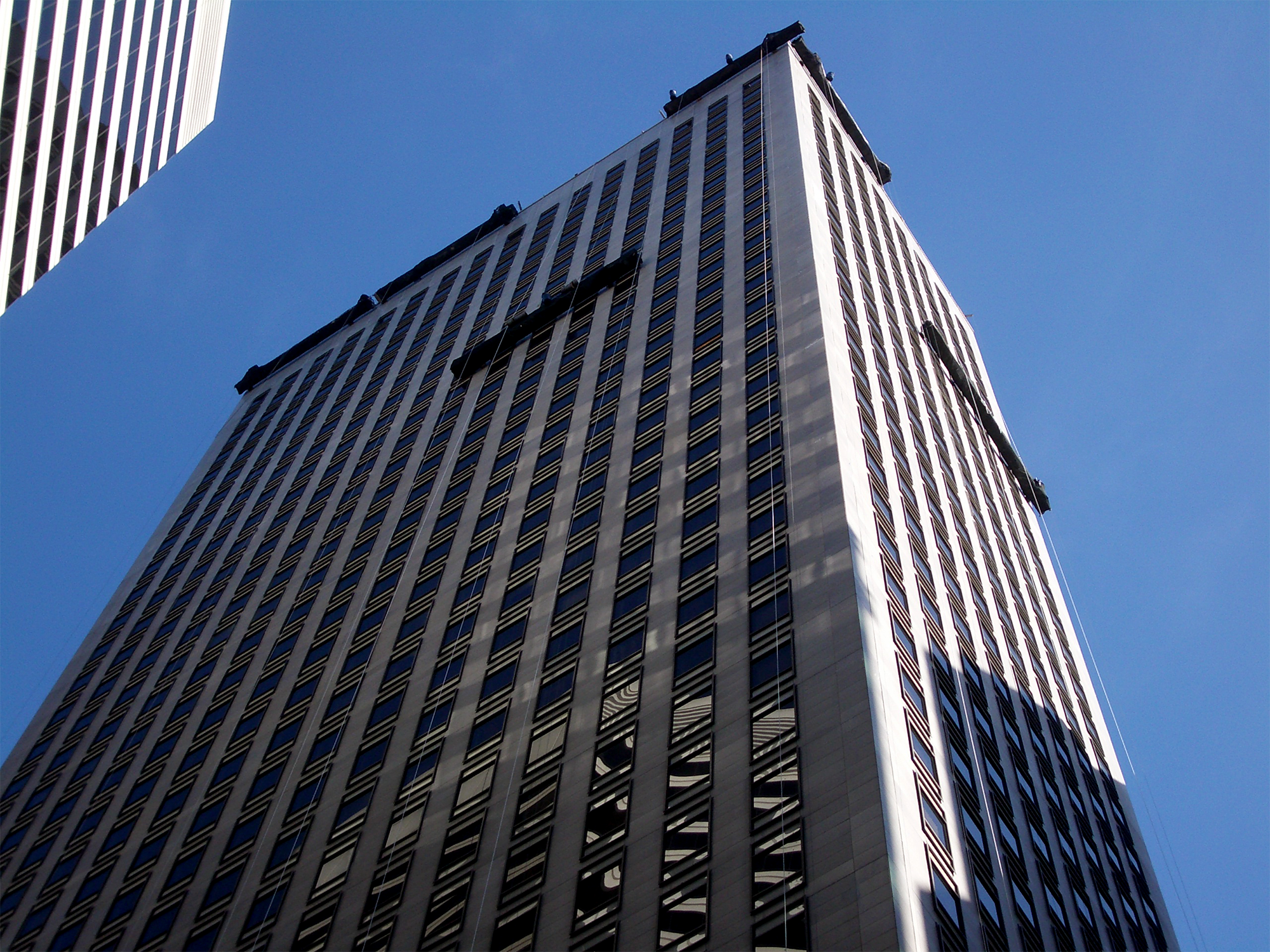
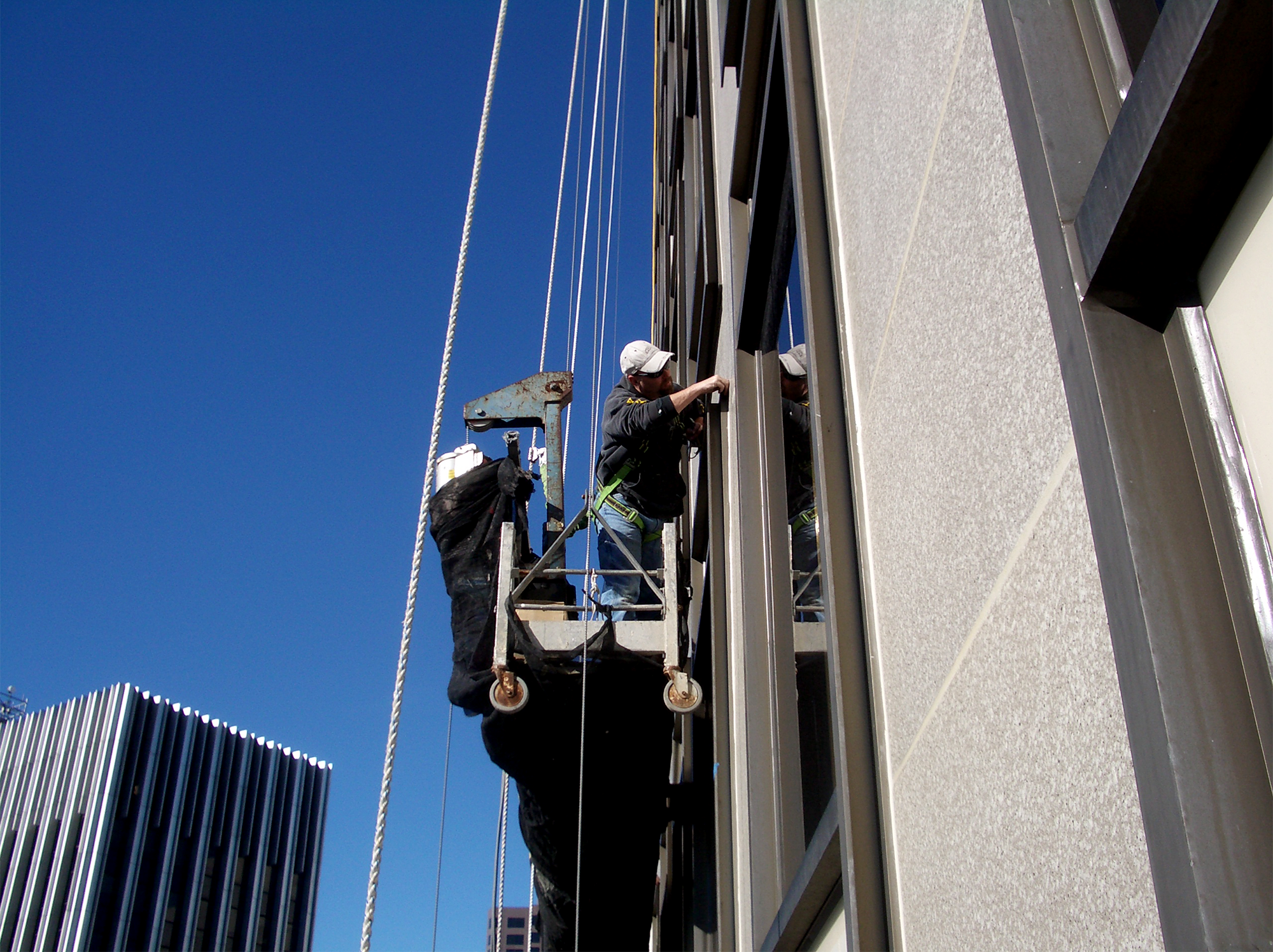
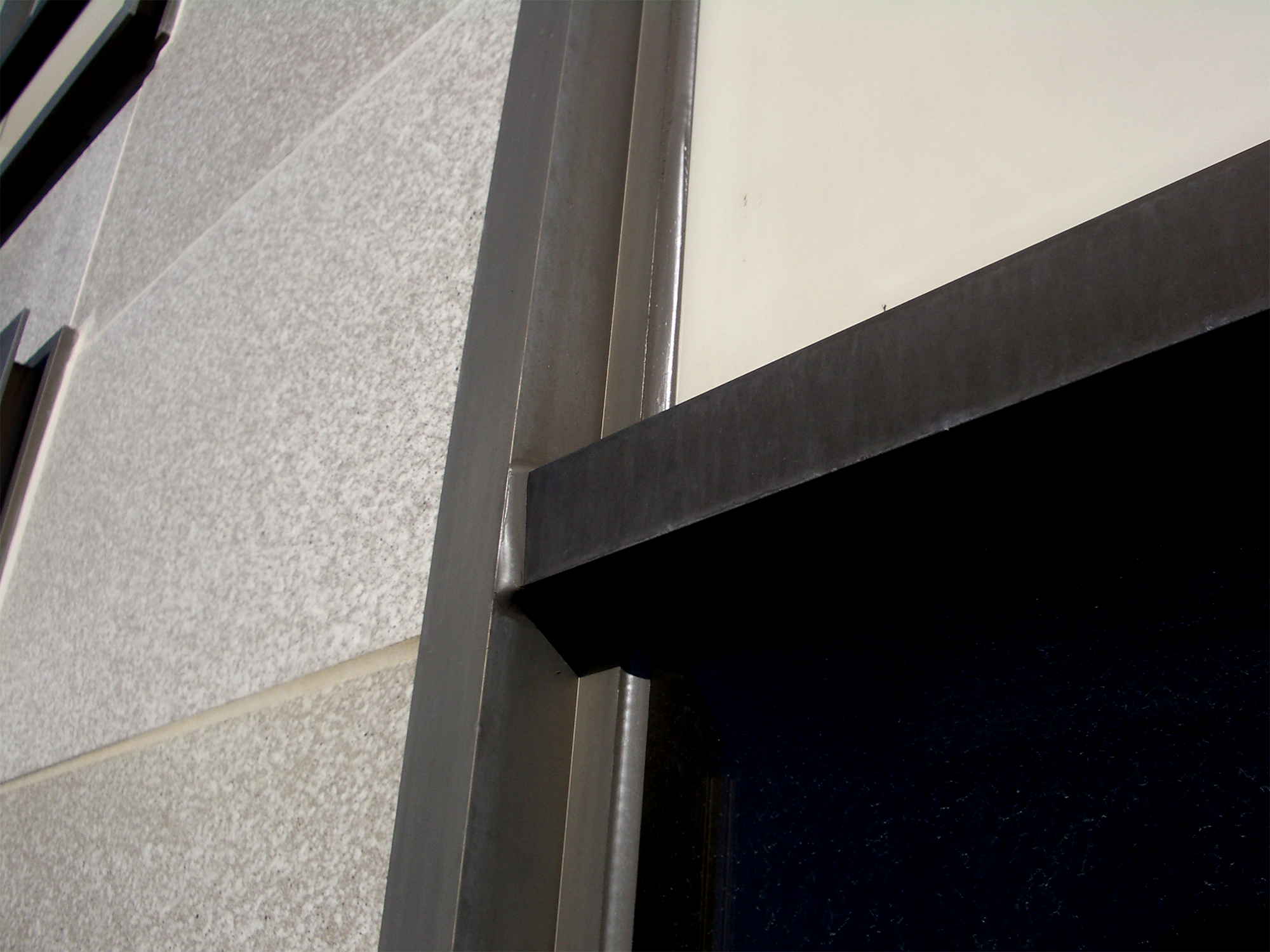
What We Did
Installed over 200,000 lf of sealant at building panel joints, window perimeters, and window wetseal.
Performed repairs with eight swing stages operating simultaneously.
matched the custom speckled finish and texture of terra cotta panels to repair terra cotta panel glaze spalls.
Replaced nearly 10,000 lf of granite panel mortar joints.
Project Details
Prior to the installation of the new Dow Corning 795 silicone sealant, the existing sealant containing PCBs had to be carefully removed and disposed of by an abatement specialist.
After this, new sealant backer rods were installed at all building component interfaces, operating from eight swingstages. Despite working overtime to meet the schedule, all repairs were completed by their target finish dates.
Existing deteriorated window gaskets were trimmed back and replaced with silicone sealant, known as "wet seal," a much longer-lasting and UV-resistant seal than the original gaskets.
Many large terra cotta spalls were repaired at the mechanical panethouse, where failure in the panel sealant joints above allowed water to leak down and collect at the base of the wall, causing the panels at the very bottom to crack and spall.
At the base of the building, mortar joints connecting large granite slabs were failing, again allowing water to get behind the large stone pieces and damaging the metal support members. The existing cracked grout was removed, joint band lines prepped, and new non-shrink grout was applied and struck flush.
For all areas where work was being performed overhead (almost the entire project), pedestrian canopies were erected down below to ensure the thousands of pedestrians who passed below each day were well protected. In addition, a rigorous tool tethering program was developed; all of the dozen tools each worker needed daily were attached to them using lanyards and cords.
Want to know how we can help with your next project?