Overcoming scheduling constraints to keep Biotech lab on schedule
Britannia Pointe
A careful phasing plan keeps the research lab on schedule during the extensive waterproofing project.
One of many biotech research centers in South San Francisco, Rinat’s and Exelixes’ buildings, originally built in the 80s, was due for a building envelope waterproofing upgrade. The original panel joint caulking was failing, as was the caulking at the window perimeters. The original window gaskets, now 30 years old, had lost their original flexibility and were allowing too much water into the window’s framing system. The EIFS shell has taken its share of bumps and dings over the years and needed to be patched and repaired.
EIFS building repairs, both the patching of the lamina and the replacement of the sealant, require expert care to make sure the soft foam on the inner part of the EIFS system is not damaged. Techs use knives and grinders but have to have a very light touch. In addition, this location was a research facility. There were strict scheduling constraints to make sure the noise and percussion from our work did not impact studies and trials years in the making.
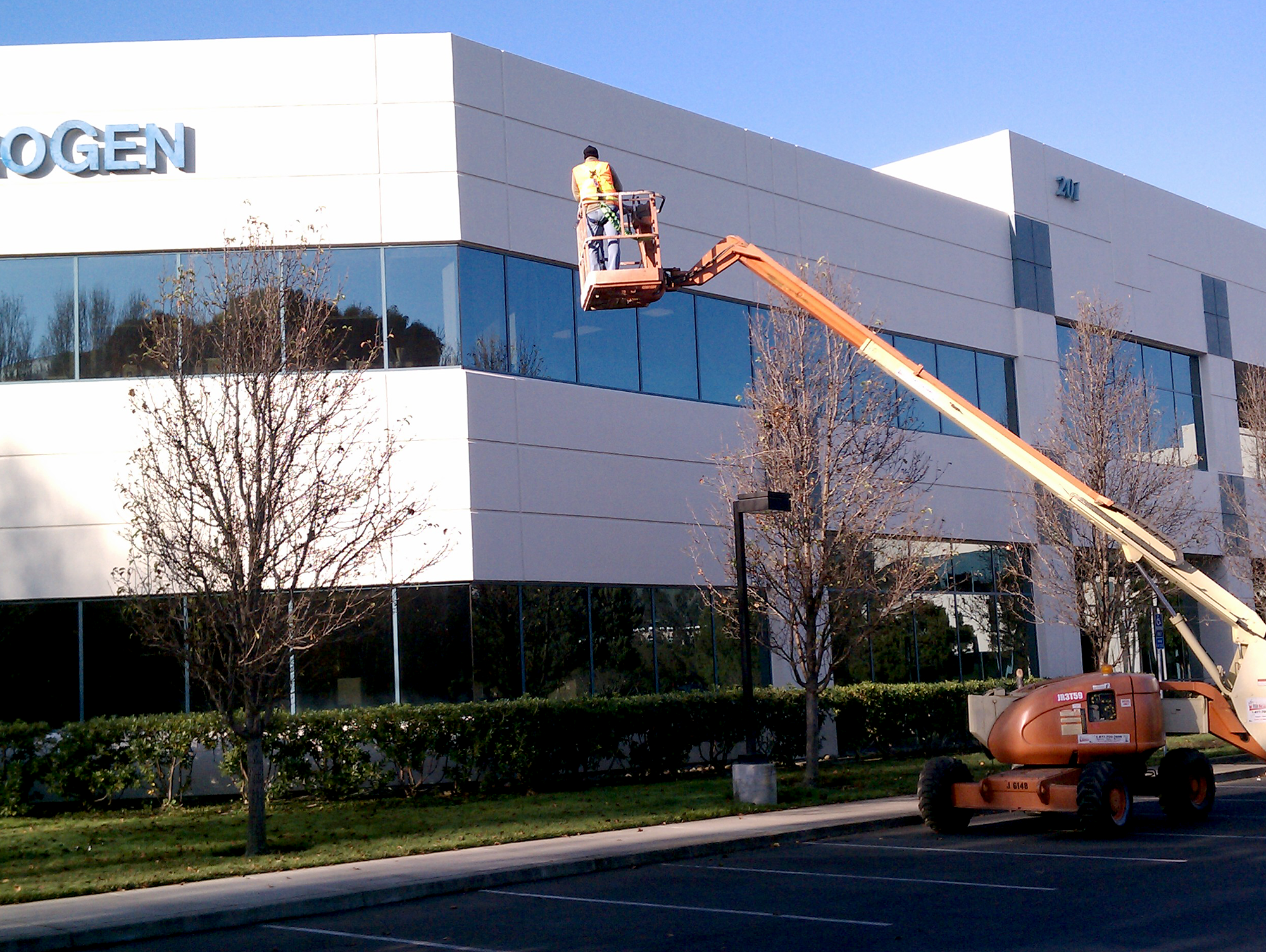
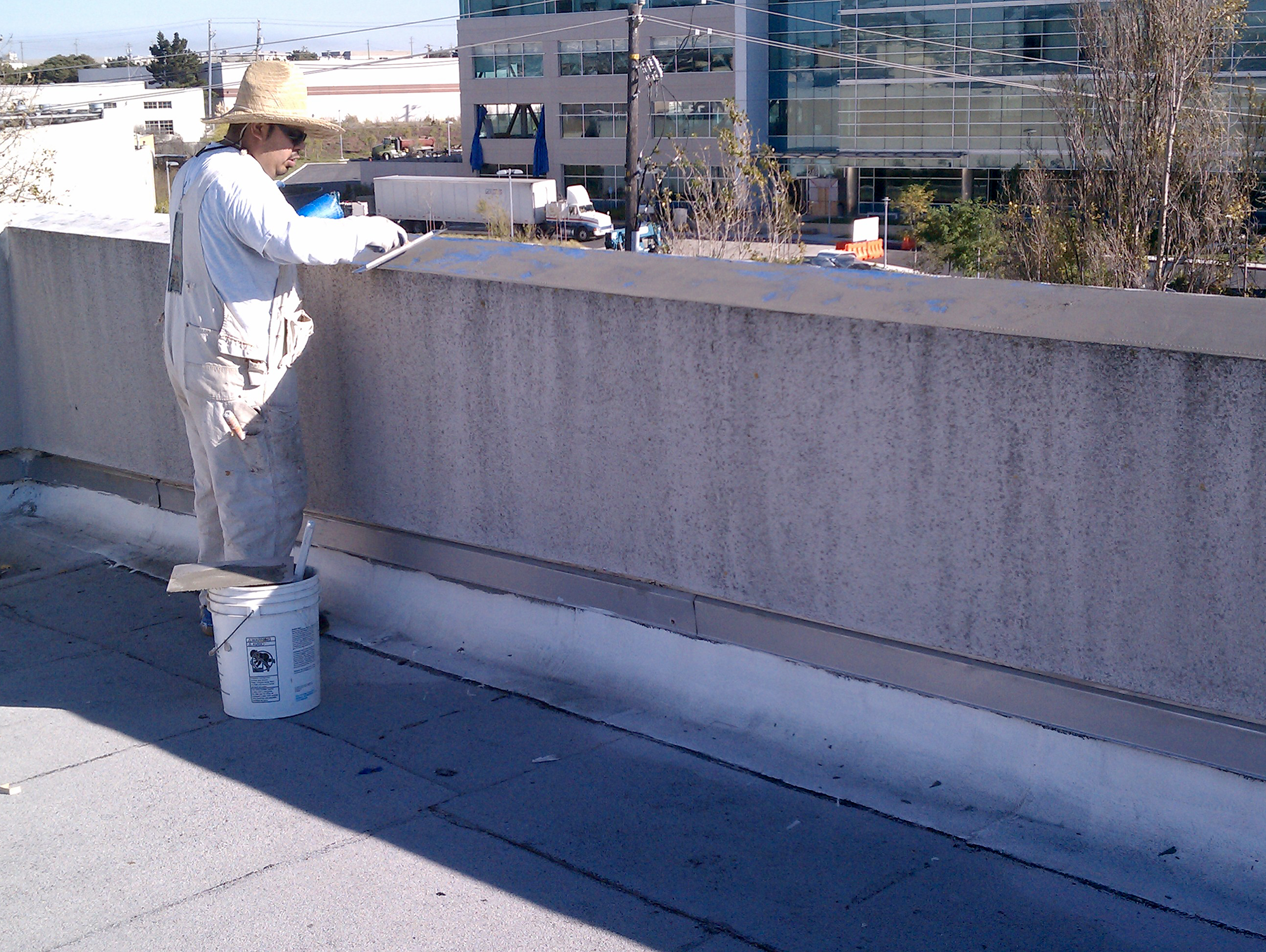
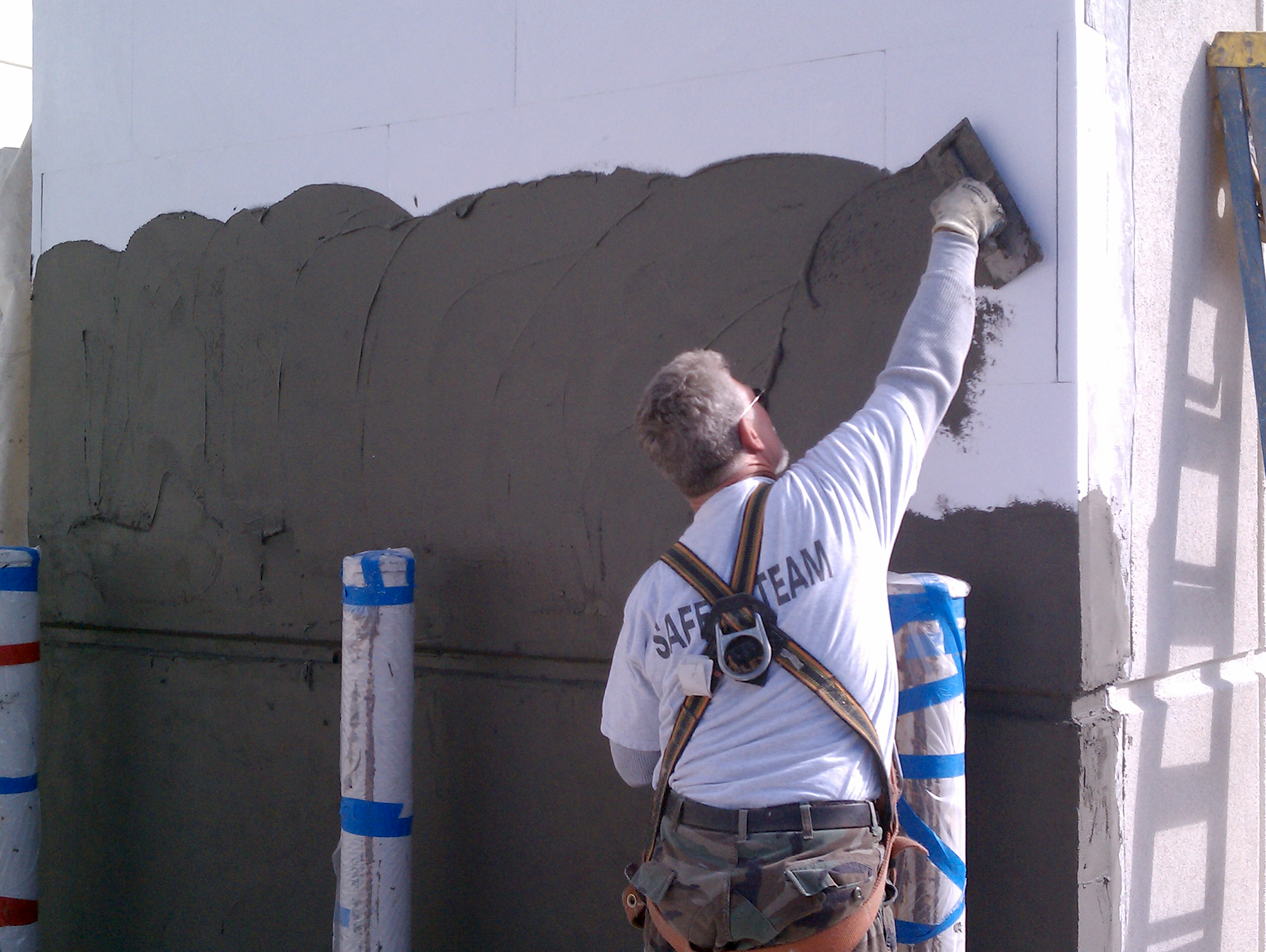
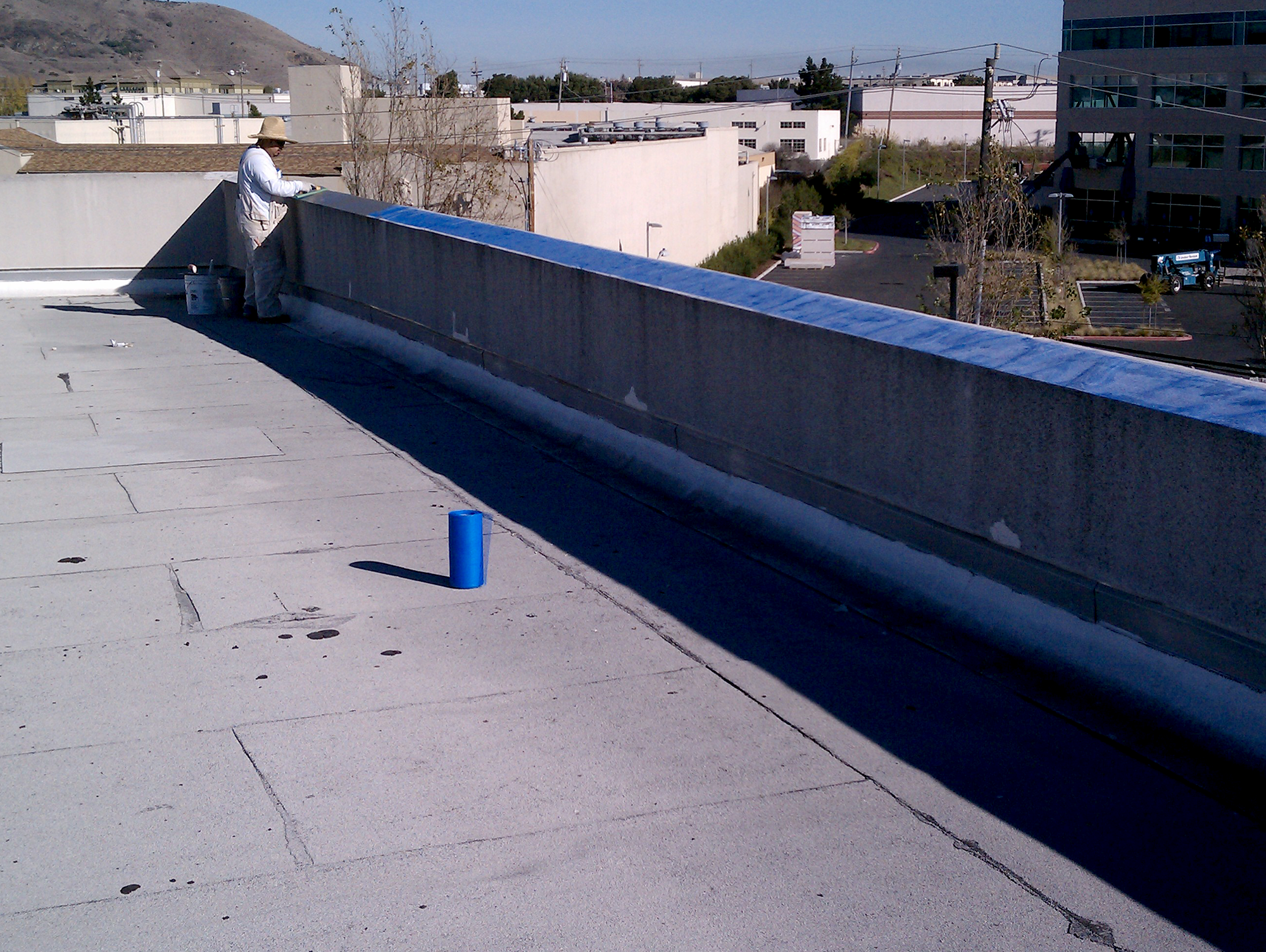
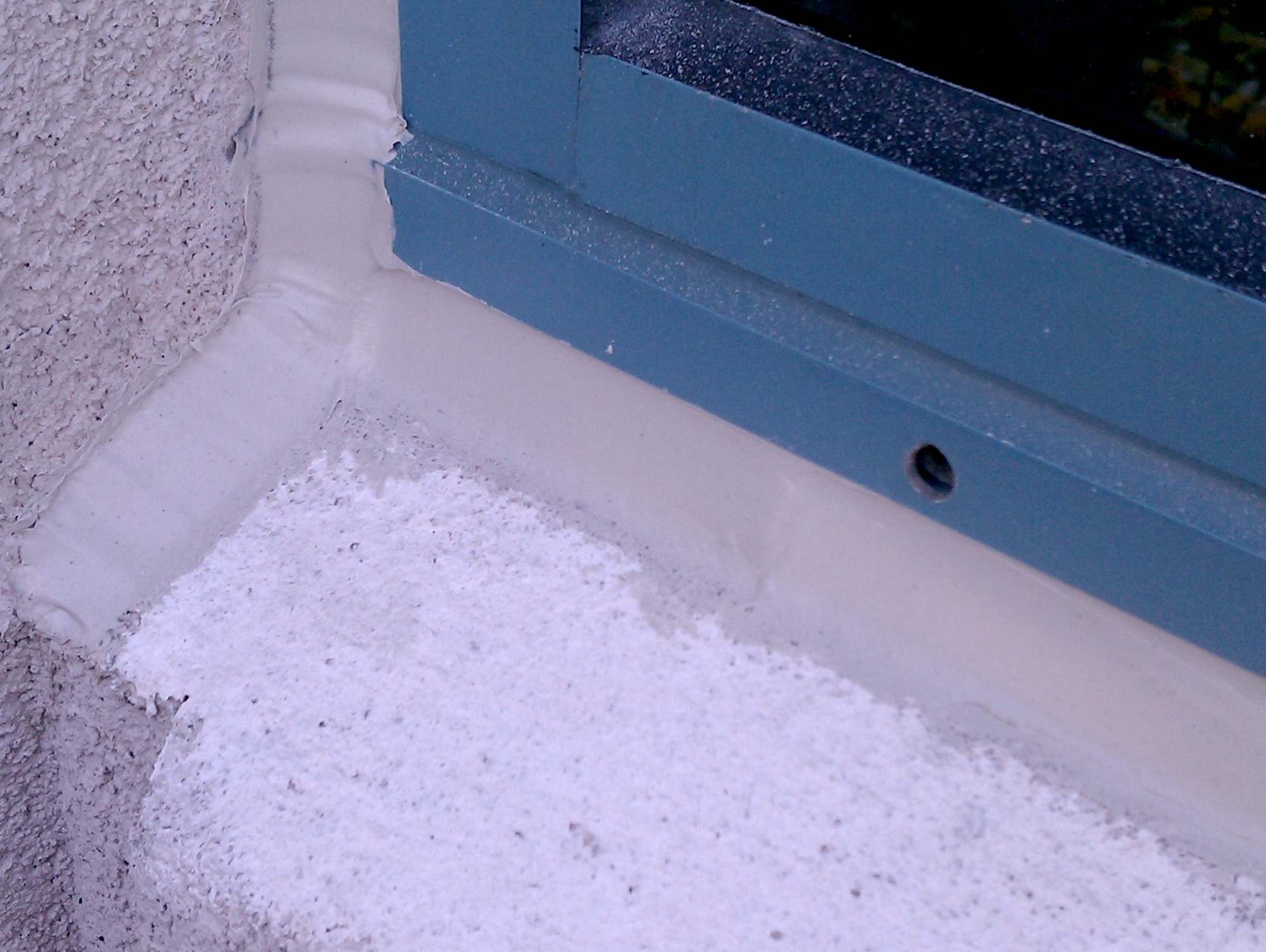
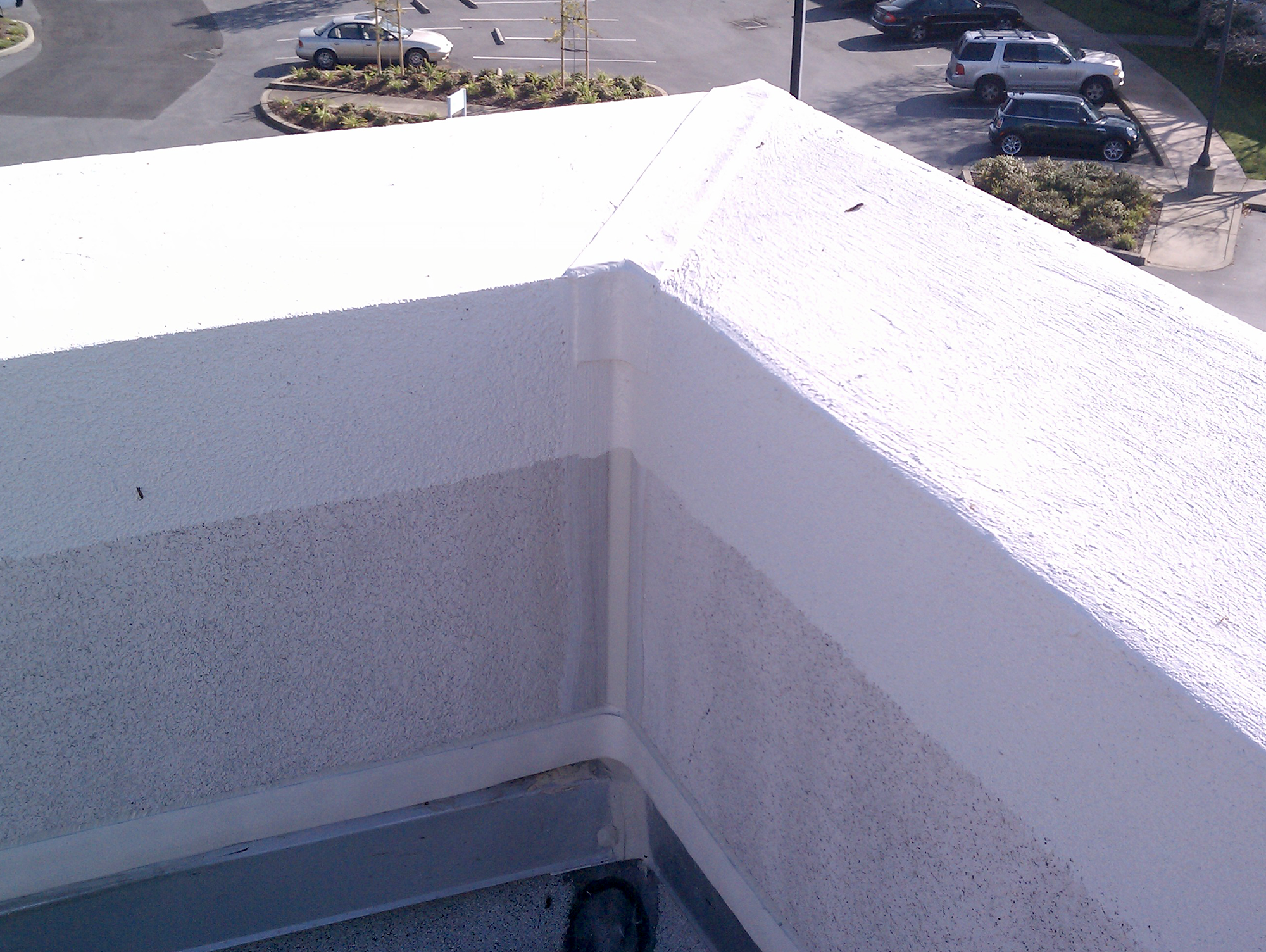
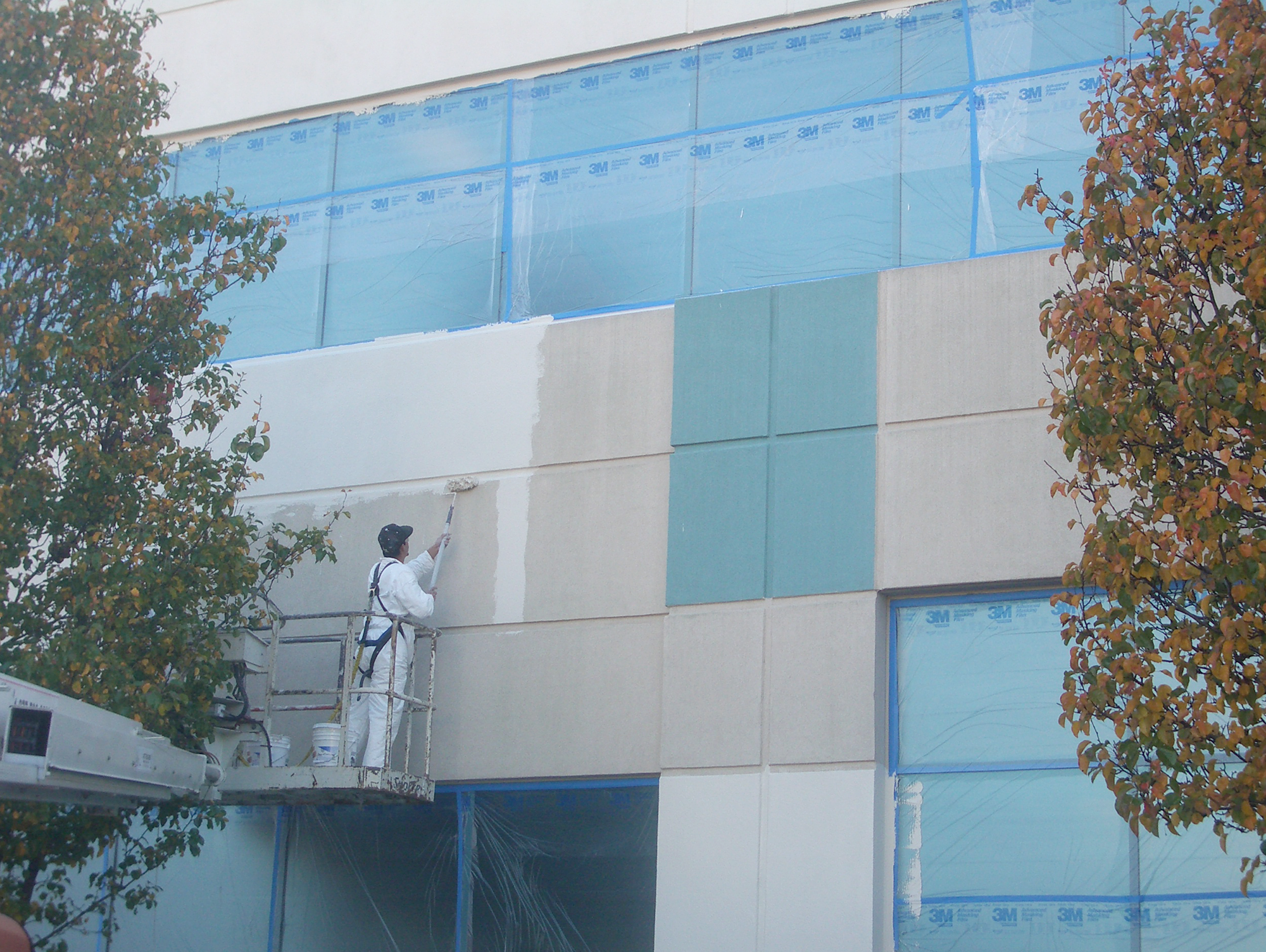
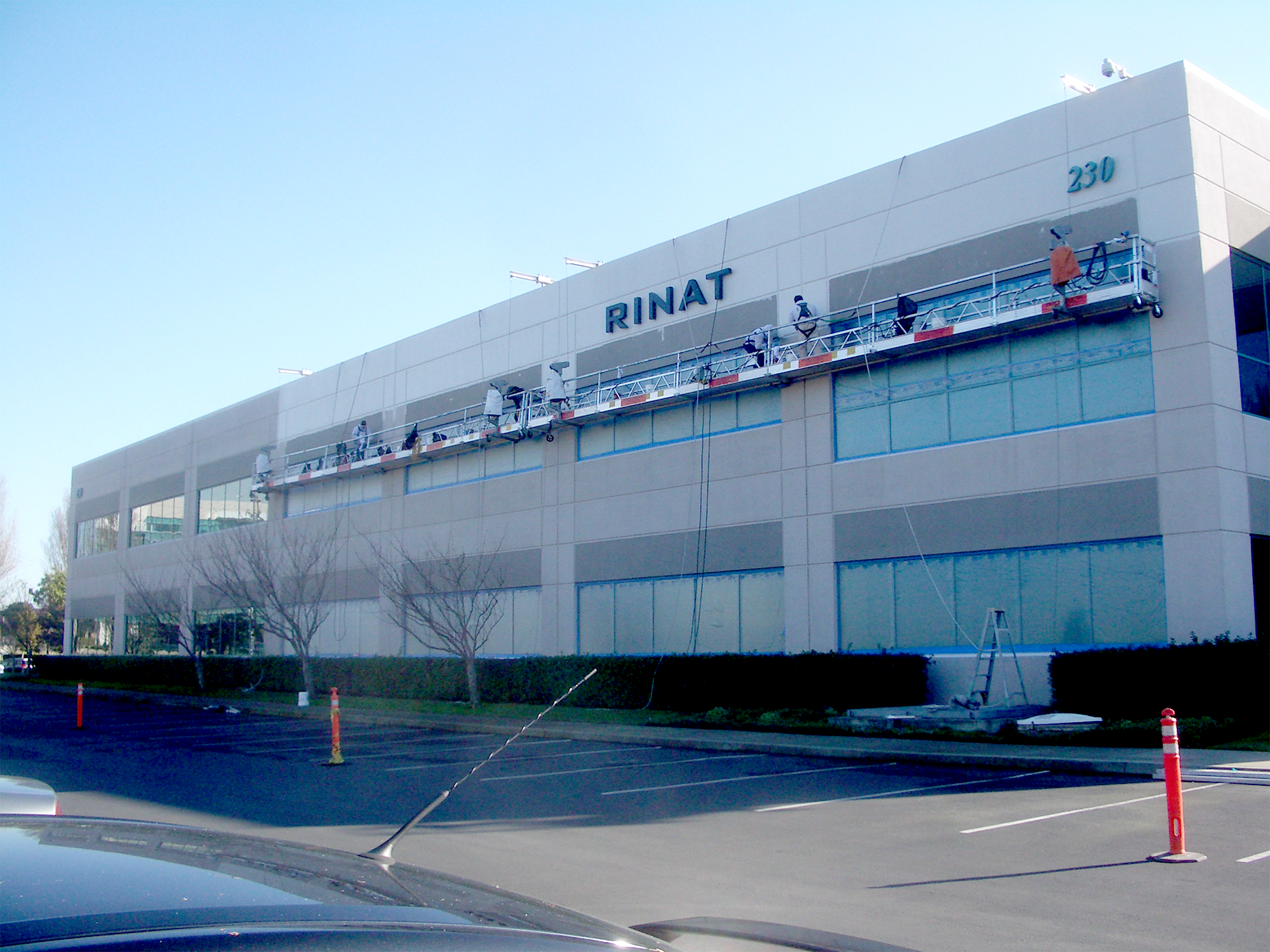
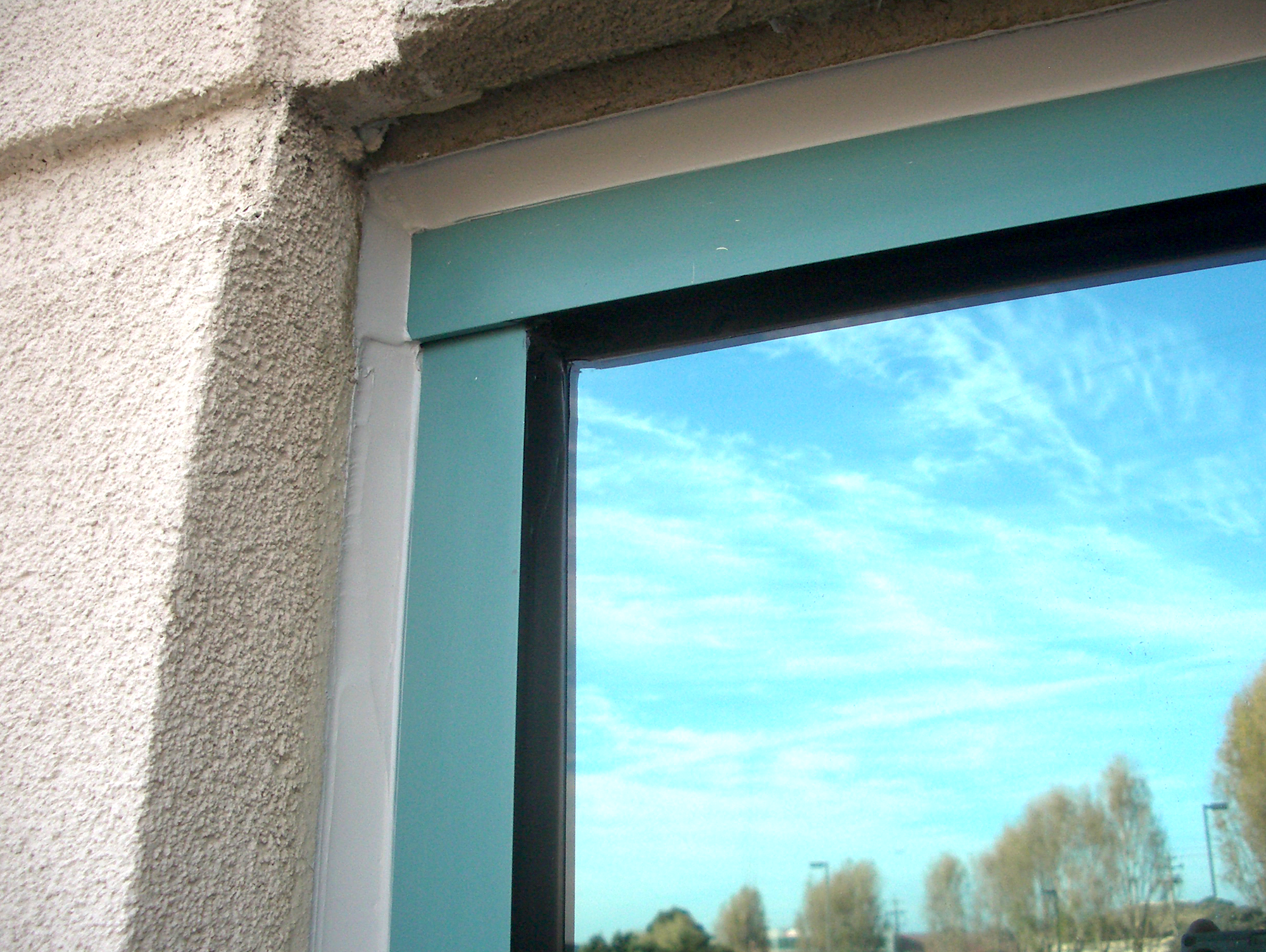
What We Did
Installed new EIFS lamina at all window ledges
Installed new EIFS lamina and silicone coating at all parapet caps
Replaced existing caulking at all building expansion joints and window perimeters.
Removed existing window gaskets and installed new silicone wetseal.
Coated walls with Dow All Guard silicone elastomeric coating.
Accessed buildings using a combination of swing stage and boom lifts.
Project Details
The first step was to address and repair the sun-baked and compromised upward-facing ledges and parapets of these EIFS buildings. Allana Buick and Bers designed the repairs, which consisted of removing the existing textured topcoat, installing new basecoat and mesh, and applying a second basecoat to create a robust yet smooth texture that would shed water instead of the original textured finish that trapped dirt and grime. Techs had to work very carefully with the grinders to ensure the soft foam layer underneath was not damaged. Once complete, those sections were primed and ready for the application of the silicone coating to follow.
Removal of the caulking at the window perimeters takes an expert craftsman. Using sharp pipe and hook knives, the existing sealant had to be removed, but carefully so as not to damage the foam. After the pipe knives came the grinder part, which was used to remove the residue of the existing sealant and create a strong bonding surface for the new sealant. Once new backer rod was installed and bondlines primed, new silicone fillet beads could be installed for a watertight seal.
There were numerous EIFS repairs required, from smaller lamina layer and crack repairs to repairs involving removal and replacement of the foam underneath. Another expert-level repair to do right is making sure the edges of your patch extend out into the sound wall far enough for a good bite and that your texture coat is matched and blended in well to hide the patch.
With all substrate repairs complete, the two biotech campus buildings were finished off with two coats of Dow Corning All Guard silicone elastomeric coating.
Want to know how we can help with your next project?