A long-term, high-performance roof coating system for ongoing leaks
343 Sansome St.
343 Sansome is a high-rise commercial office building located in San Francisco’s financial district. Over the years, the owner had made numerous attempts using various vendors to conduct costly spot repairs to the EPDM sheet ply roofing system on the roof level mechanically penthouse, but to no avail. After installing a new elevator system with associated expensive mechanical equipment in the room directly below, the owner ultimately realized it would be necessary and prudent to provide a long- term solution to the problematic roof above. Given that the owner had successfully used Urban in the past for various waterproofing issues on their building, they reached out to see if we could help.
Having experienced numerous leaks in the sheet roofing system gave pause for concern about going back with a similar product. Sheet roofing systems are mechanically fastened or heat-welded at the seams and set with adhesive in the field of the sheet. The long-term problem with these types of roofing systems is that when leaks arise, it becomes very difficult to pin-point the exact location of the point of entry as water can find its way in through a breach, migrate under the roofing membrane, and show up as a leak in different locations. To that end, Urban advocates installing fully adhered fluid-applied roofing and waterproofing systems, which typically have a much longer service life and are easily spot repaired or modified as necessary. After reviewing the scope with the owner, Urban assisted in sourcing a product vendor (Sika) and helped draft the spec & bid documents for the bid RFP. After reviewing the bids, the owner determined that Urban offered the best overall understanding of the project's special needs and was awarded the contract.
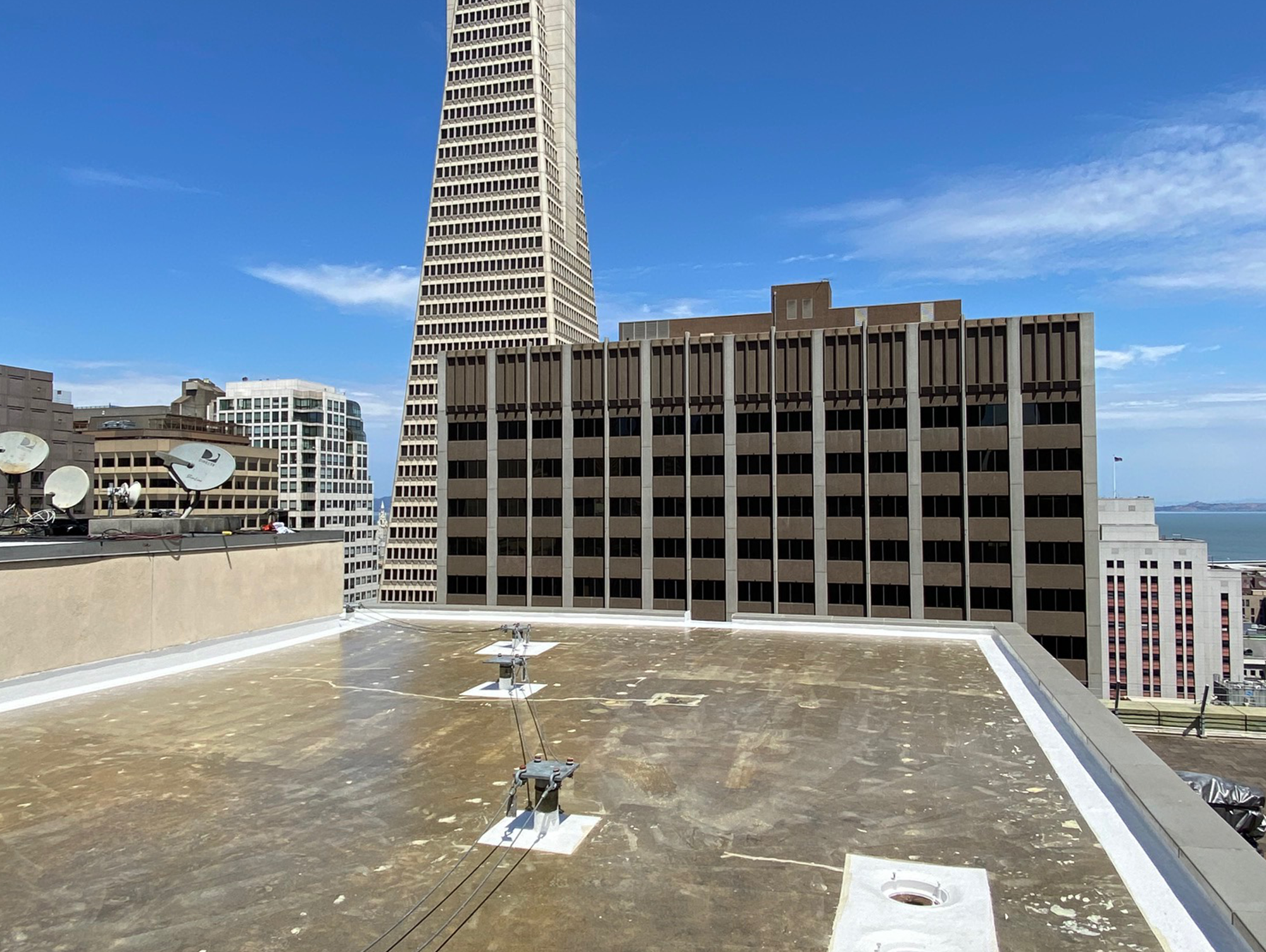
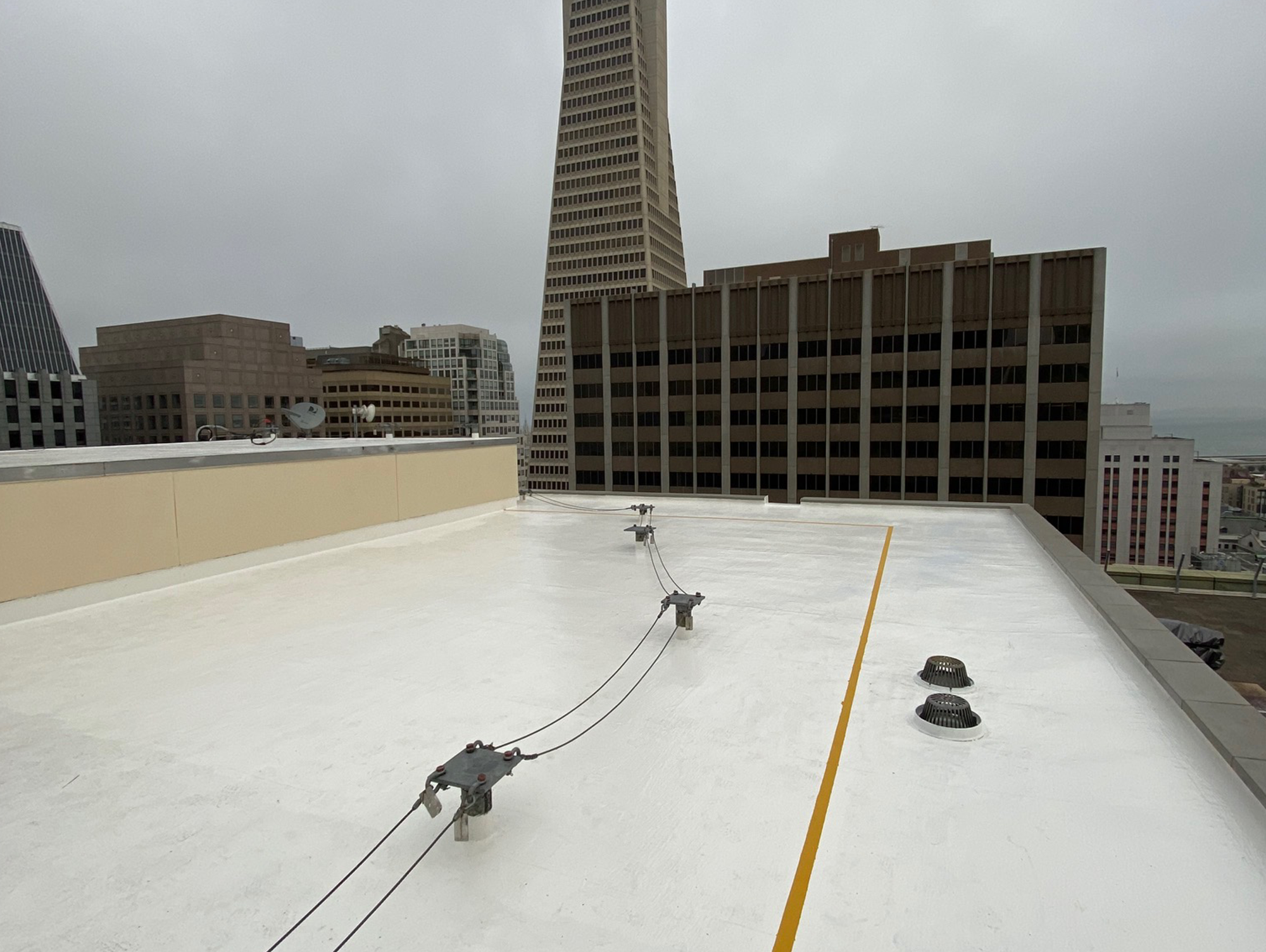
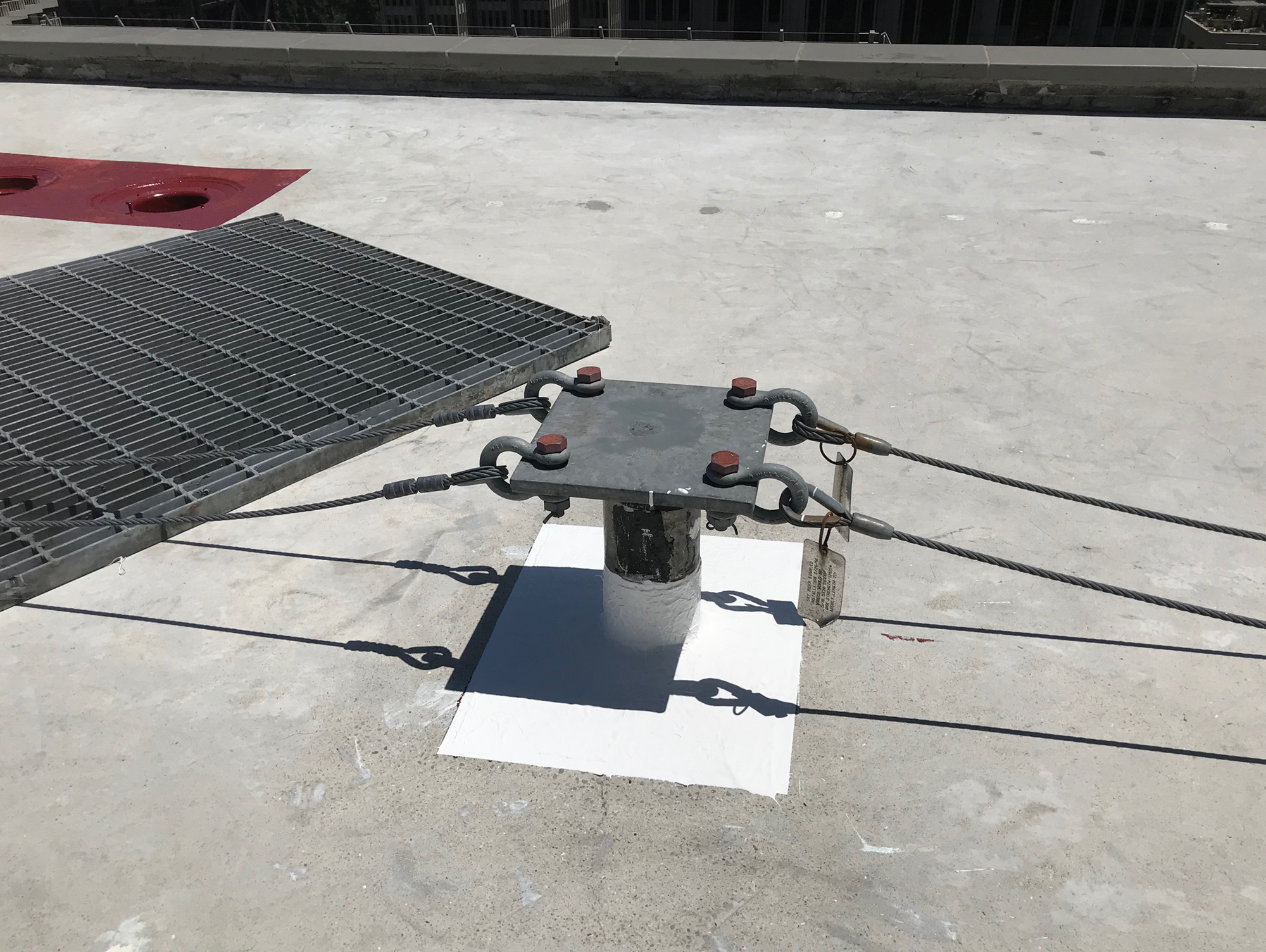
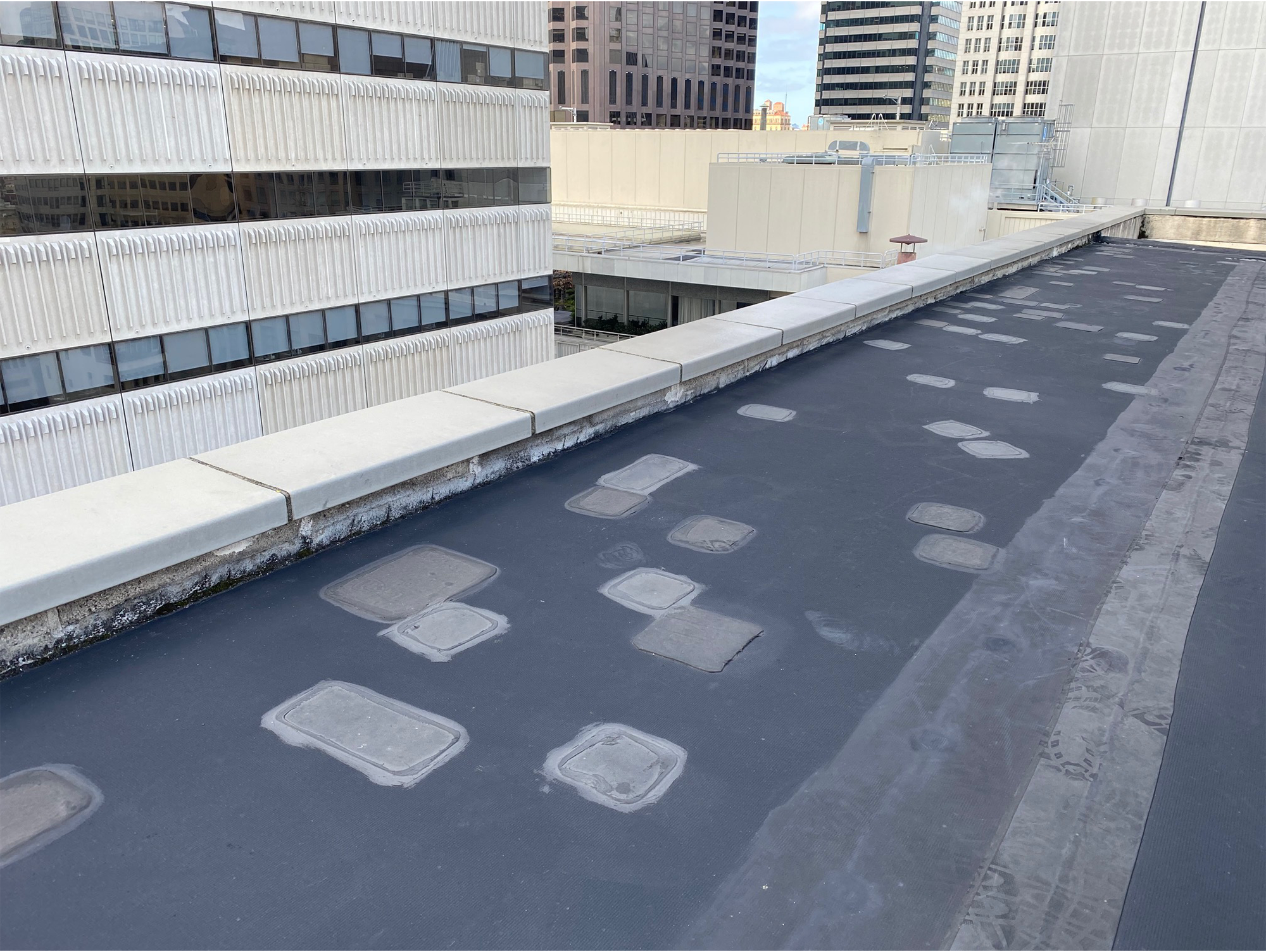
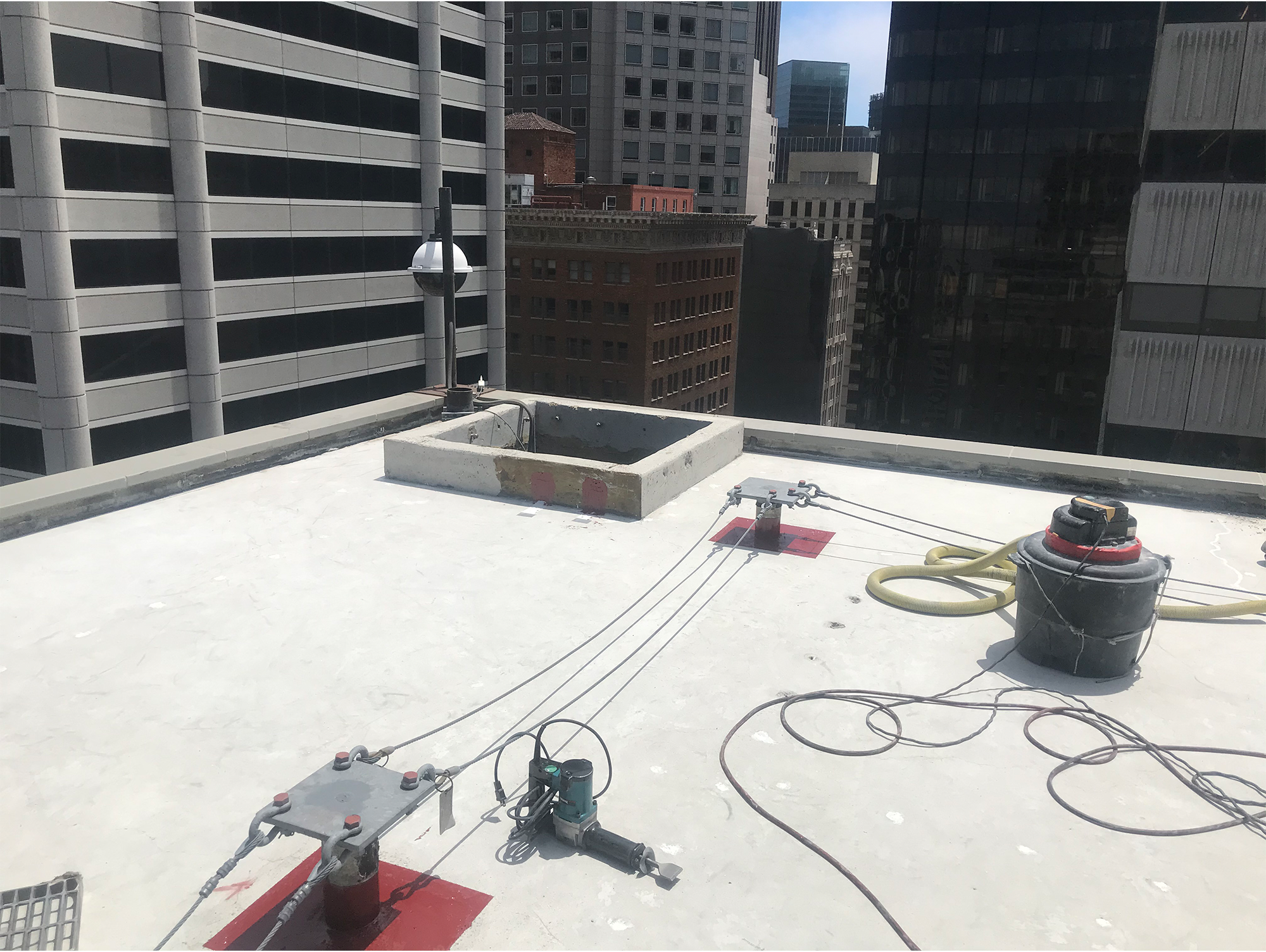
What We Did
Removed the existing roof system.
Prepared the exposed concrete deck (spalls & cracks).
Apply SikaRoof Pro 20 Full Reinforced System 2,500 sq ft
Installed new metal flashing
Project Details
To accommodate the owner’s equipment concerns, the project was broken into two phases to allow for the temporary relocation of telecom equipment from one roof level to another. In both phases, the existing roof system was completed removed and the exposed concrete deck could be surveyed and repaired (cracks and concrete spalls). After spot repairs, new metal flashing and protections were detailed and flashed in accordingly.
Once the detail work was completed, the bare concrete surfaces were fully primed with the system primer, and the roofing membrane application could commence. A base coat of the Sika 641 coating was applied, and a high-performance reinforcing fabric was fully embedded. Over the base coat, a finish coat of the Sika 641 system was applied, achieving an 85 DFT mils finish roof system. Additionally, areas of potential high traffic (mechanical service locations) were detailed with another coat and seeded with aggregate for further protection. The finish system will provide the owner with years of leak-free peace of mind…..
Want to know how we can help with your next project?