Successful specialty installation in a compressed time frame
Rincon Center
The Rincon Center is a mixed-use office, residential, and retail complex located in a highly active area in the SOMA district of San Francisco. The building has both high-rise and mid-rise structures that abut one another and are tied together structurally by means of a seismic expansion joint system. Over the years, the seismic joint system had experienced extensive stress and movement that had caused numerous breaches and tears within the joint system below, resulting in significant leaks into the office space below. With a new high-profile tech tenant set to take the office space below, the owner and Urban performed a detailed forensic review of the problematic condition and ultimately determined that the joint system was well past its serviceable life and in need of replacement. While replacement of the seismic expansion joint system was the largest part of the work, along with that, Urban Waterproofing also repaired numerous concrete spalls, coated adjacent roofs and balcony decks with new high-performance traffic coating, installed new waterproofing membranes within the planter box structures, and replaced the exterior façade sealant joints—all combined, a comprehensive set of repairs to extend the life of an active commercial office, residential, and retail complex.
Accurately installing preformed, compression-fit expansion joints is a specialty service. First, it takes careful measuring along the entire width of the joint to get the proper width. With the high expense of the material, an error in measurement can be very costly. Experienced installers know that the joint widths can vary on a structure due to uneven settling or other factors; the measurement phase must be thorough and double checked in many locations. Achieving the inevitable right angles and turns and field-cutting miter joints is also an art; these areas are always the most vulnerable over time. Correctly installing expansion joints is not for the hobbyist or weekend warrior!
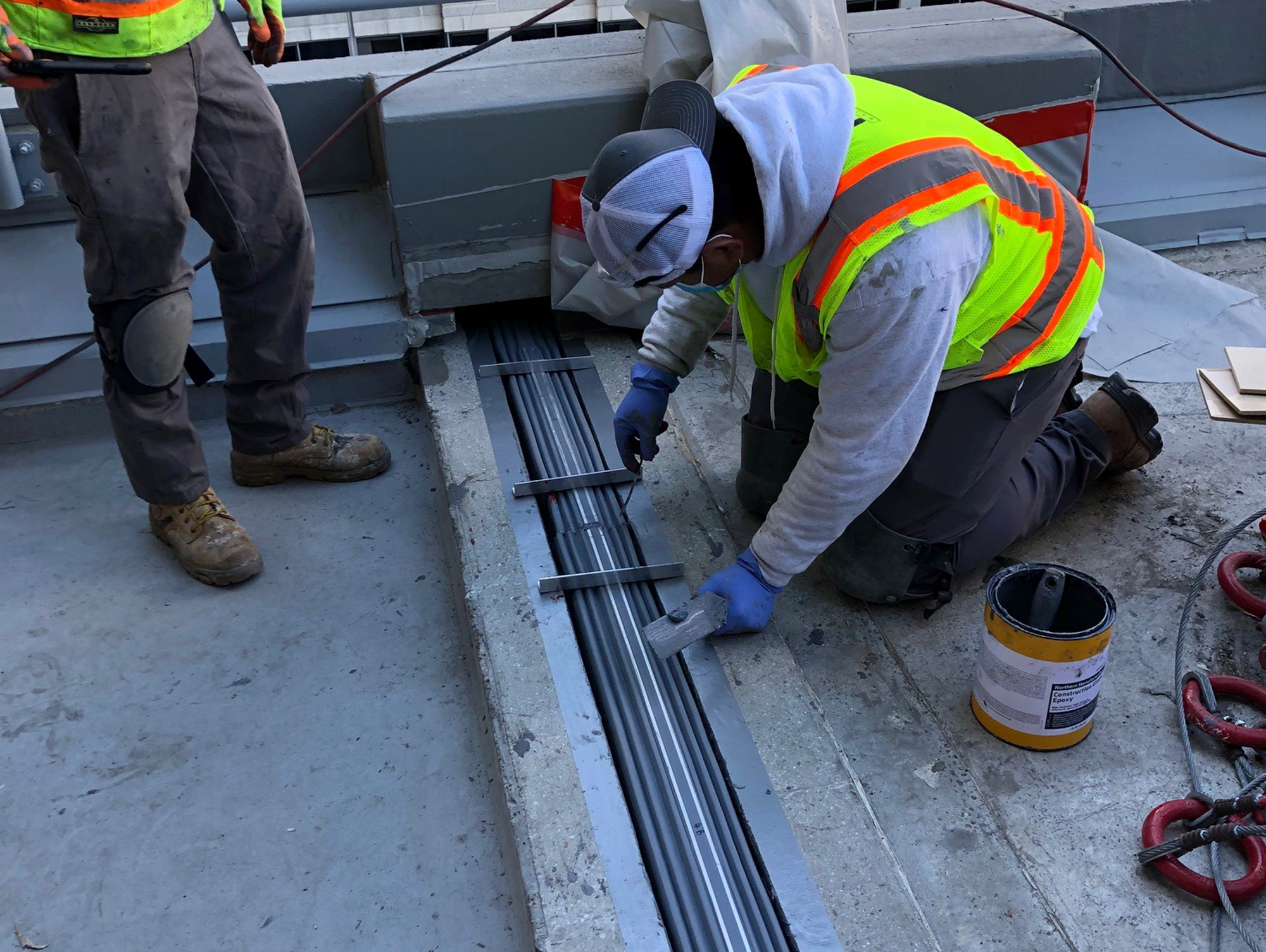
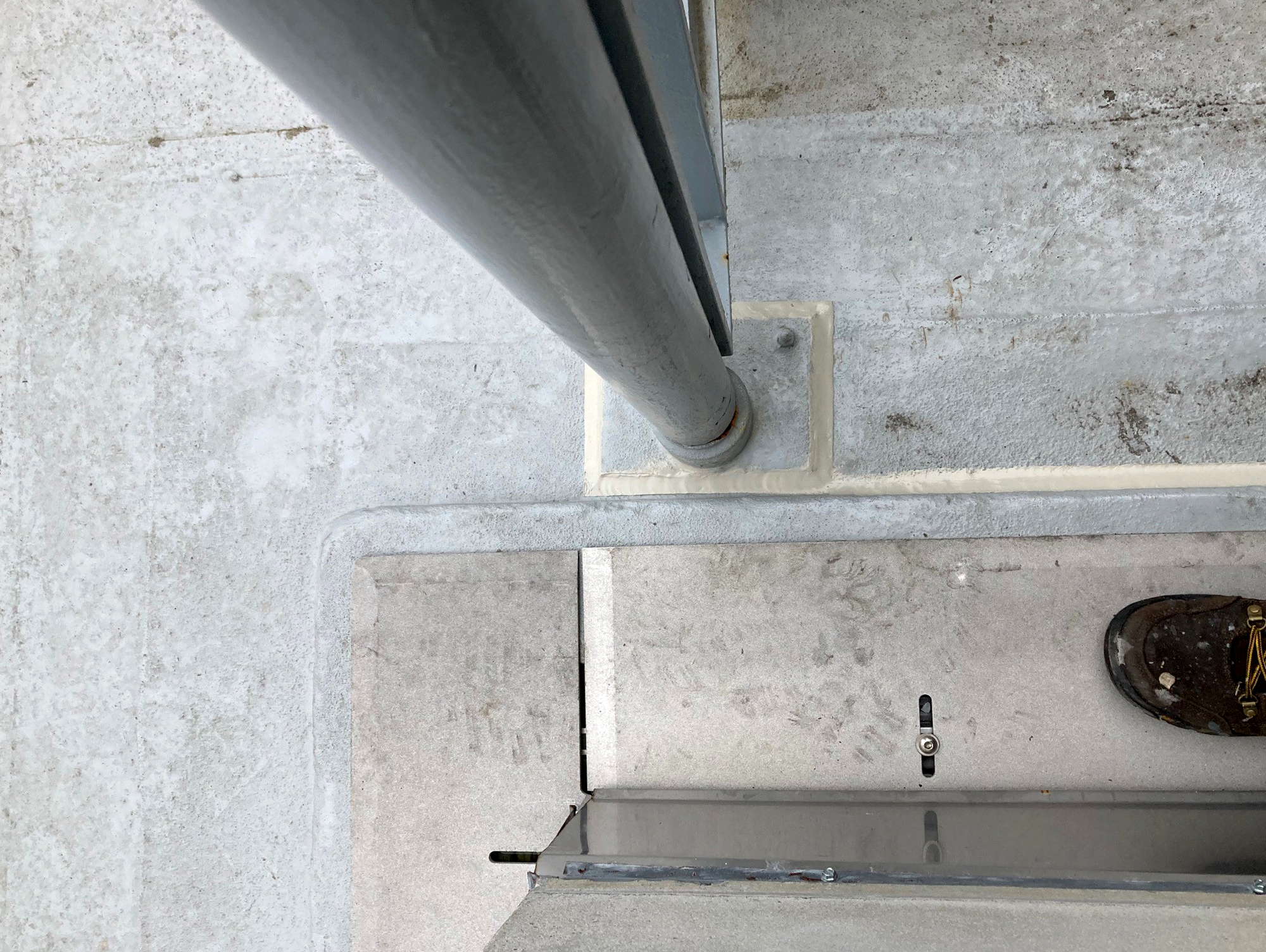
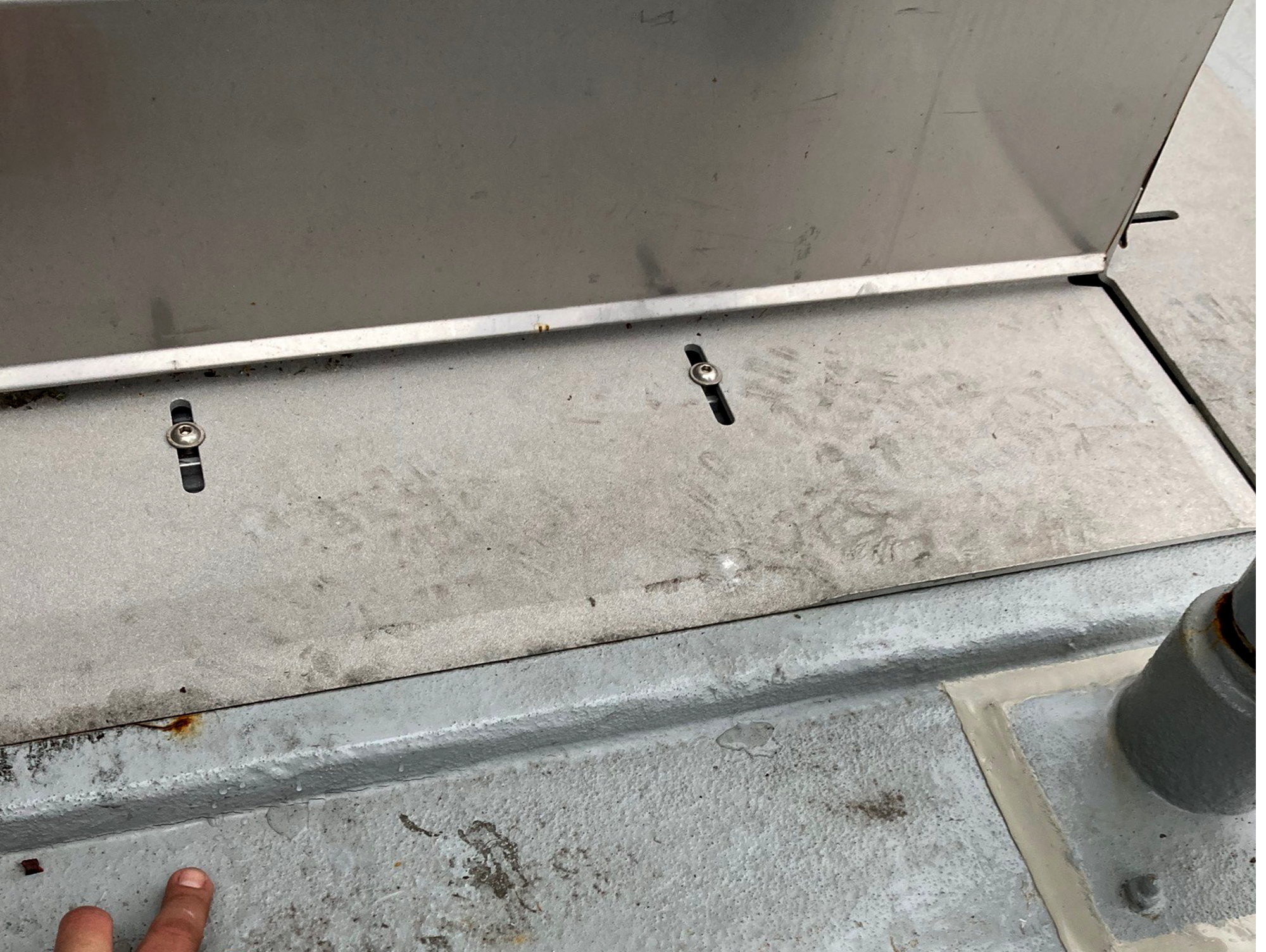
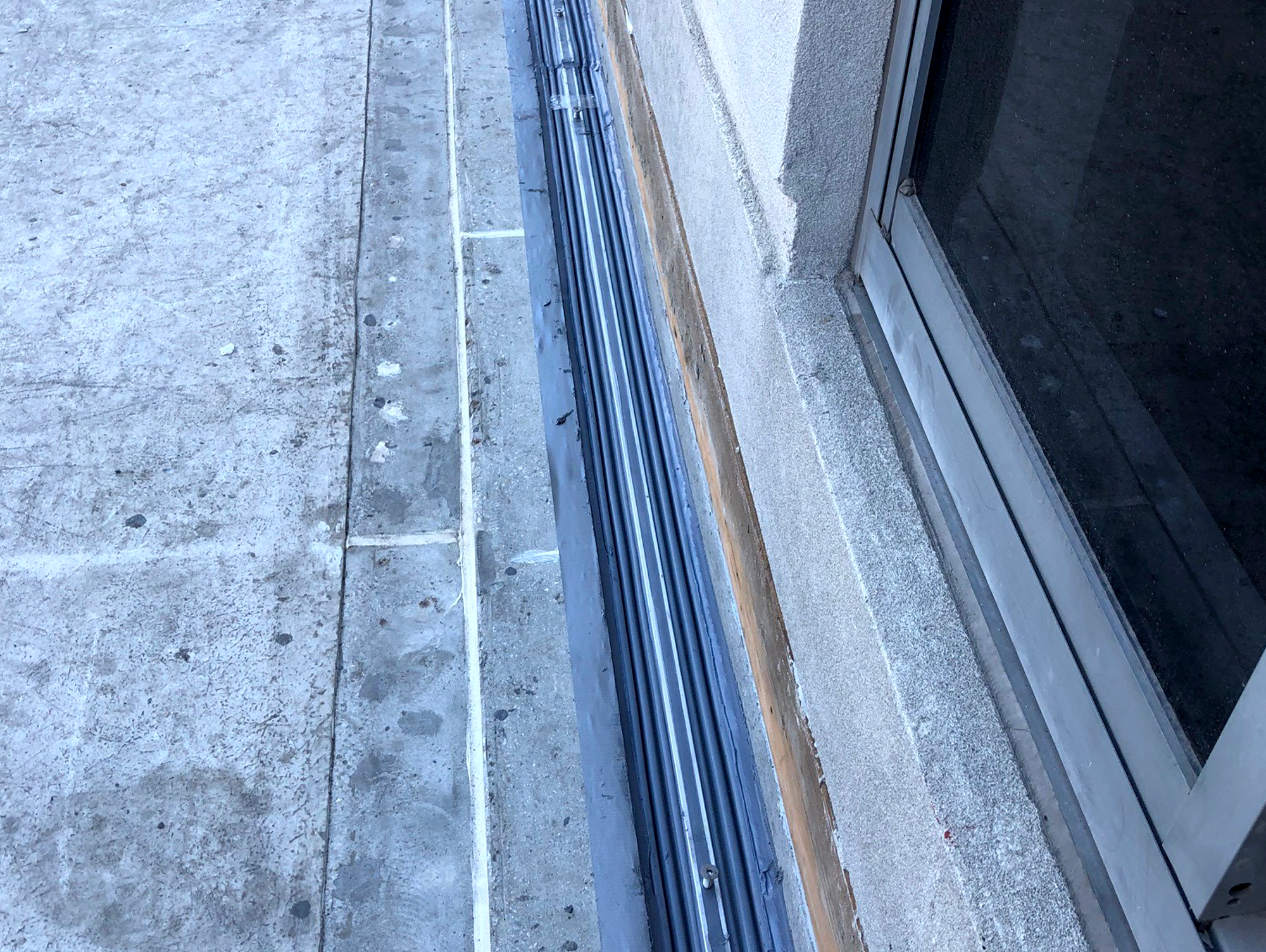
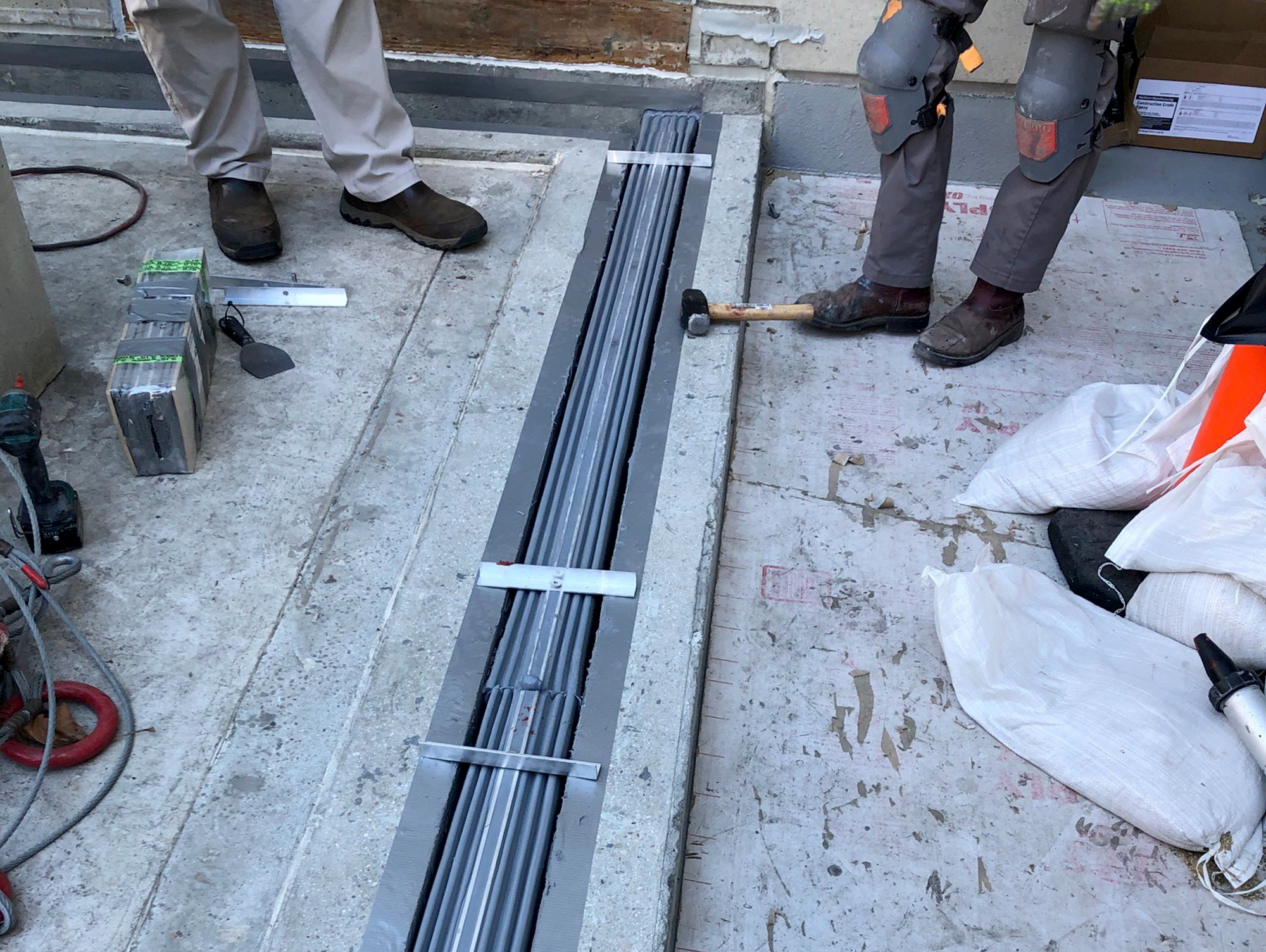
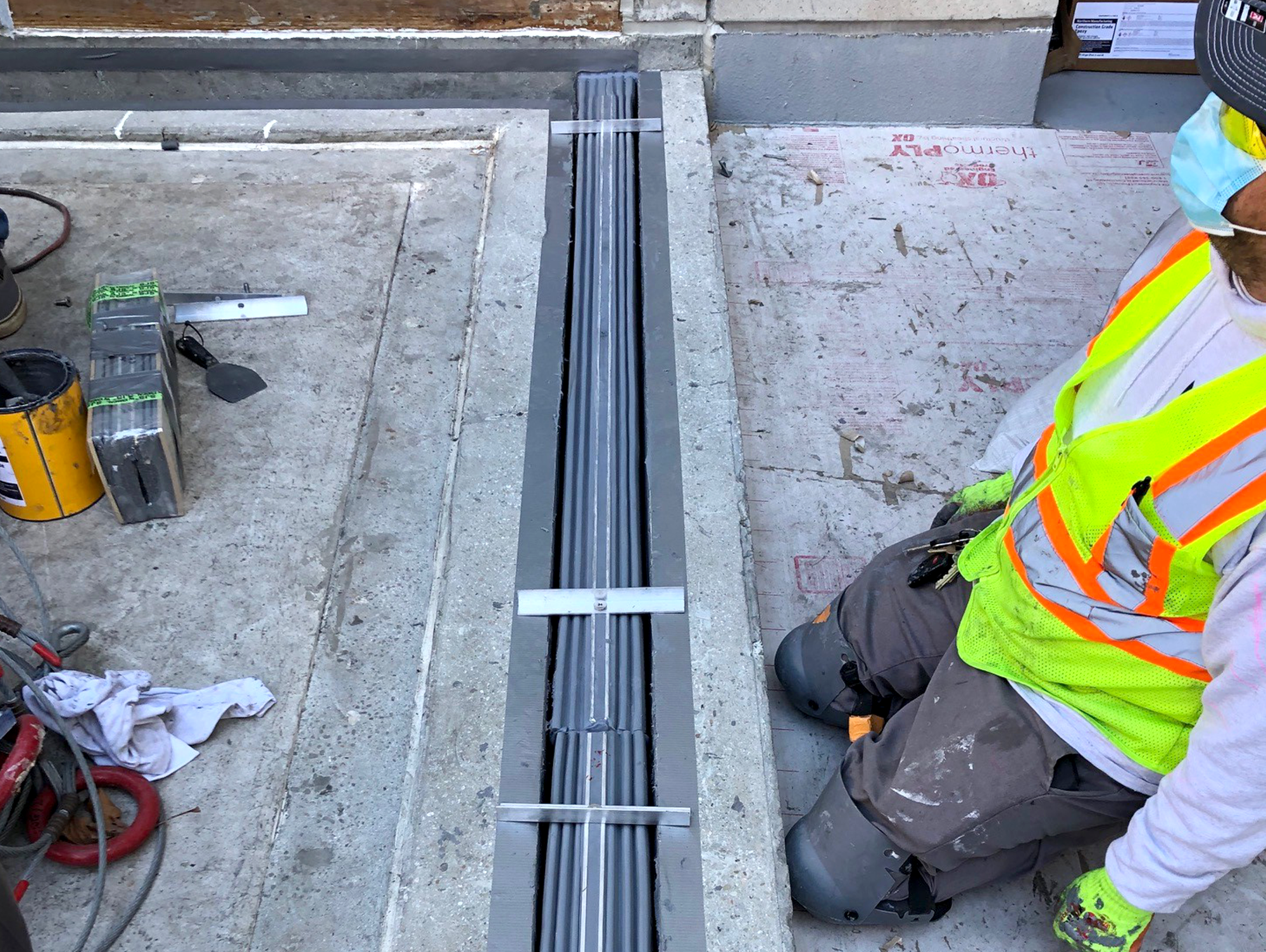
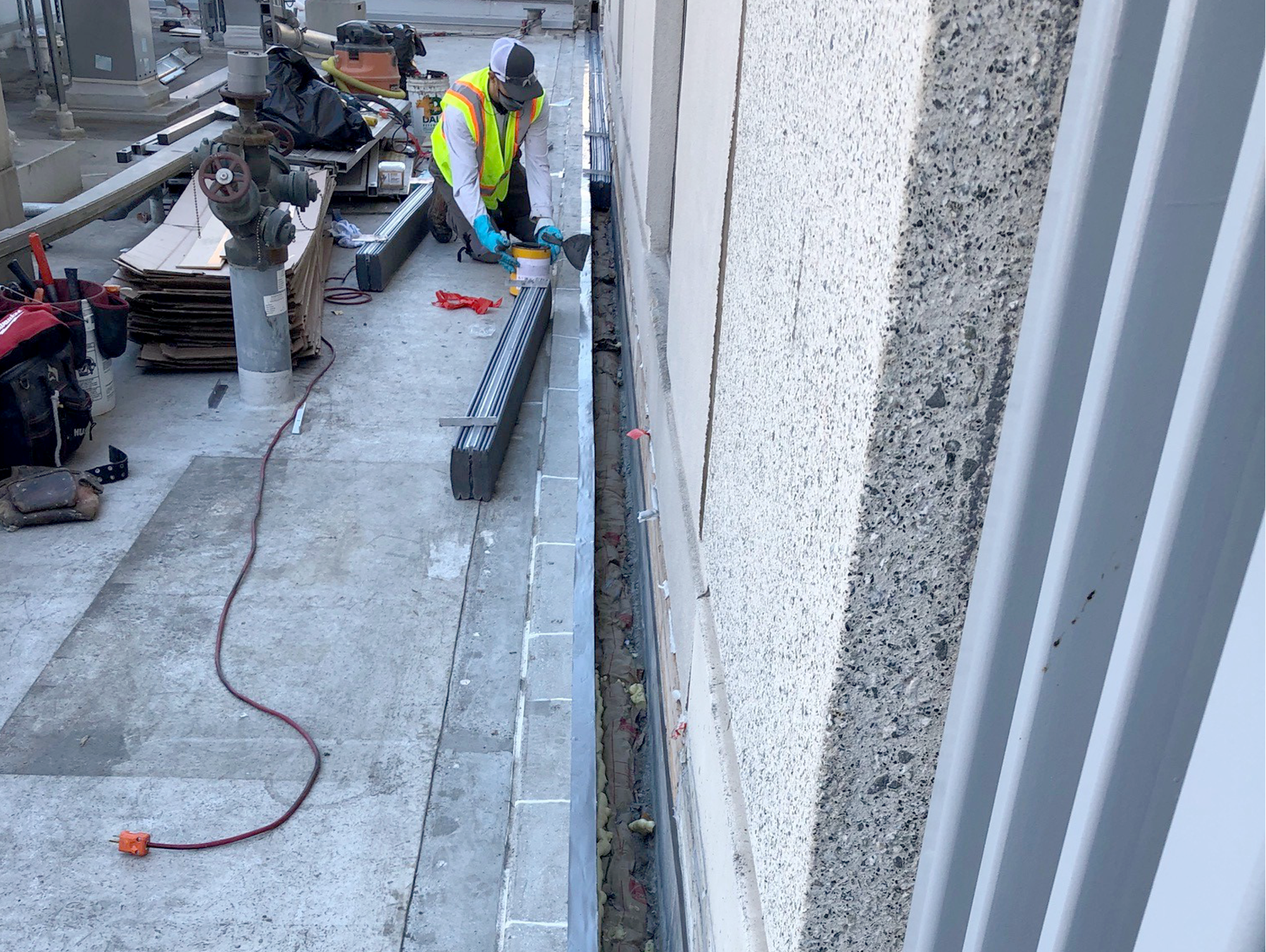
What We Did
Installed nearly 500 running feet of Emseal's preformed seismic expansion system.
installed a custom integral metal cover plate/flashing to protect the expansion joint.
Repaired numerous concrete spalls within the joint cavity
Recoated over 15,000 sq ft of adjacent concrete roofs and residential balcony decks
installed a new planter box membrane system
Replaced over 70,000 lf of exterior sealant joints
Project Details
With the new tenant scheduled to take occupancy of the space in mid-winter and given that it was not determined to move forward with the project until early fall, speed and accuracy would be paramount concerns in getting the job completed in advance of the winter rainy season. With that as the backdrop, Urban proceeded in a rapid manner to conduct an extensive field investigation, detailed measurements, and precise quantification of what would be required to order and ultimately procure the custom joint material and associated accessories in a timely manner. Having extensive experience in successfully installing these joint systems in the past allowed Urban to leverage its strong relationship with the vendor (EMSEAL) and expedite material delivery to the jobsite within a compressed time frame.
In advance of the material's arrival, the job was laid out in logical phases so that critical areas could be focused early. Once the material was onsite, demolition of the existing joint and installation of the new Emseal system were performed in a highly controlled, phased manner in an effort to minimize any potential for moisture incursion into the newly constructed, high-end office space below. During the course of the work, Urban performed numerous adjustments and real-time field modifications to accommodate differing site conditions and the revised scheduling concerns of the owner without adversely affecting the desired finish schedule or budget. As a result of the extensive pre-job planning and dedicated field oversight, the project team was able to complete the job in advance of the winter rainy season and provide the new occupants below with a safe and dry environment.
Want to know how we can help with your next project?