New planter membranes prevent water damage & prepare for drought
Market Center Planters
Two large planter boxes at the base of the financial center highrises were placed over a critical electrical room below that supplied power for the two buildings. The original lush landscaping, containing more than a few trees, had grown over the years such that the roots had punctured the original waterproofing membrane and cracked the concrete shell of the planter box, compromising the integrity of the structural slab and allowing water to drip to the electrical room below. Urban was hired to remove all of the existing compromised membrane and install a new 120 mill thick waterproof membrane. While protecting the structural slab and keeping the electrical room dry was the main priority, The Owner took the opportunity to transition the landscaping to a more drought-tolerant species.
Planter boxes provide a way for Owners to spruce up the outside of their buildings, but care has to be put into what type of landscaping is installed; some trees can grow roots that can cause damage to the membrane and structural concrete, allowing water to enter and damage spaces below. Once these conditions are identified, the best repair is to install a new membrane for these planter boxes that see water all year long, with more advanced materials and techniques than were used with older, original buildings. This provides protection for valuable spaces adjacent and below.
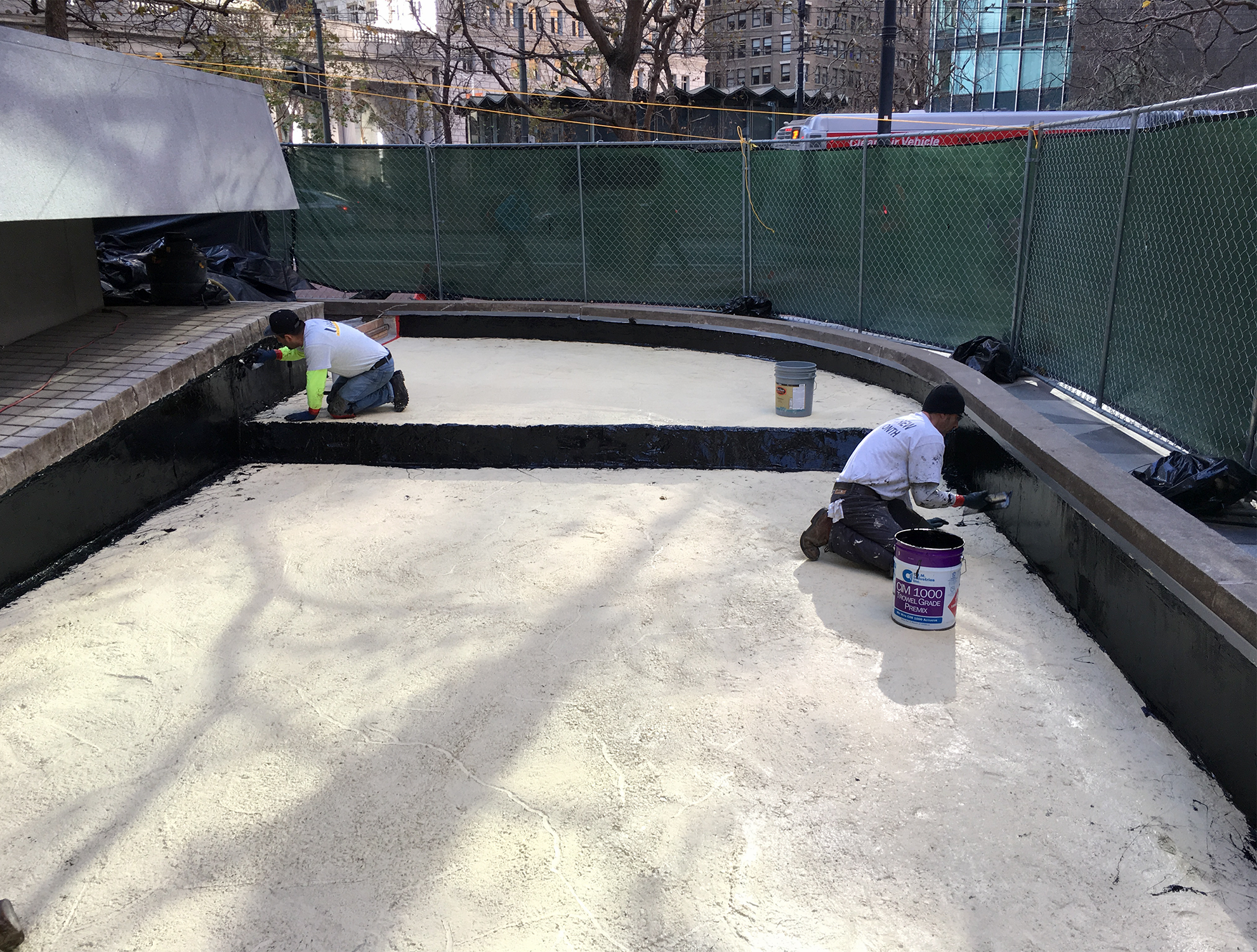
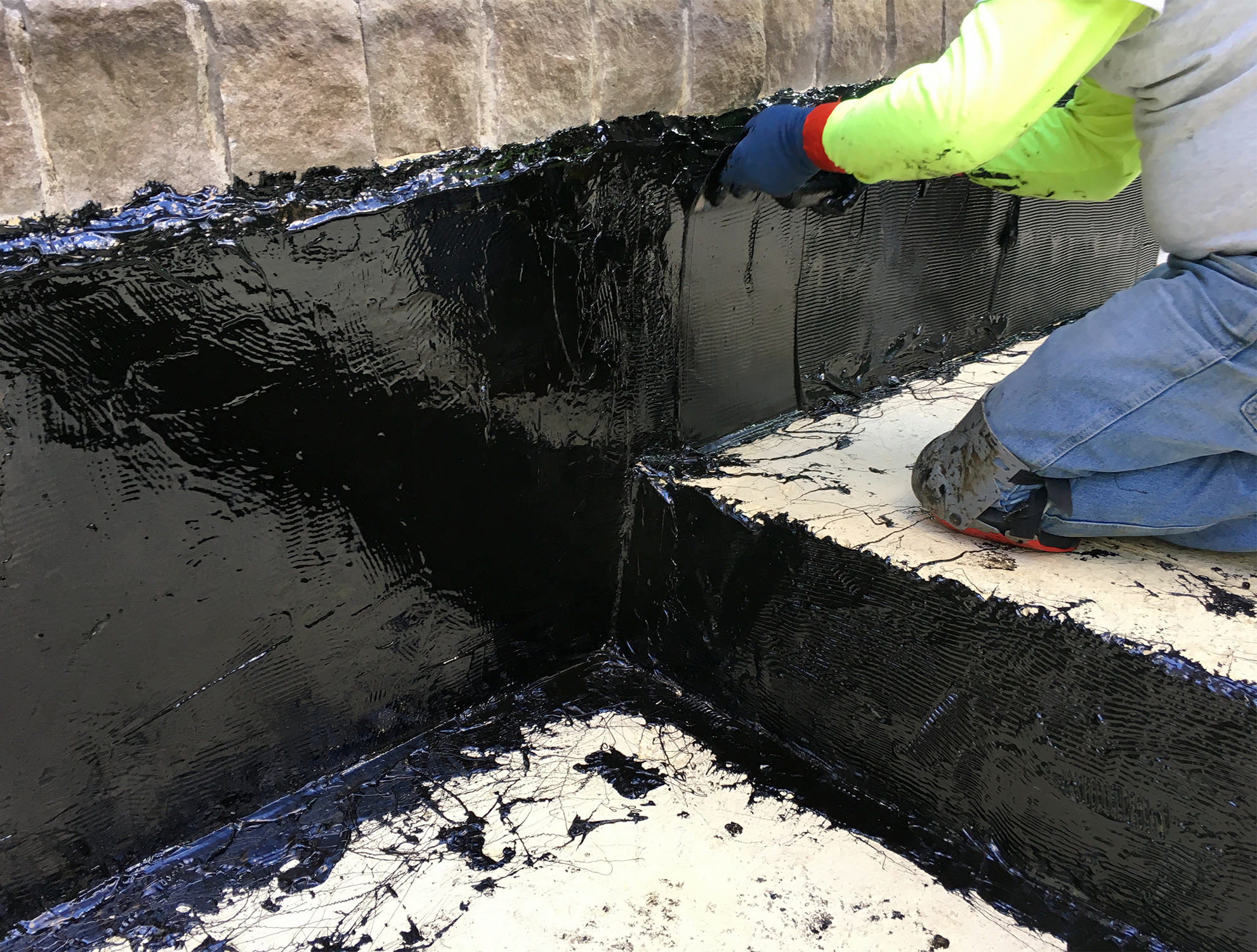
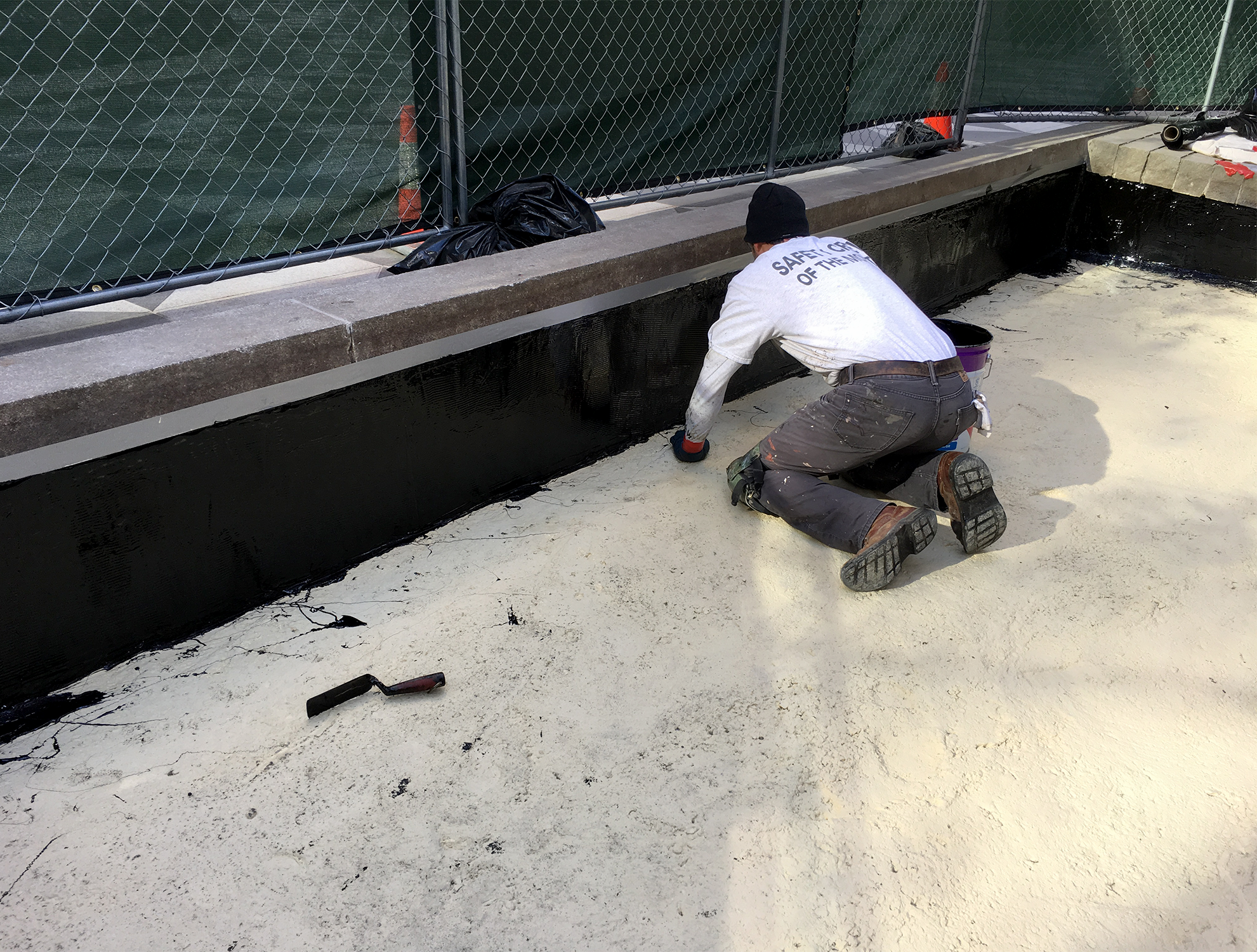
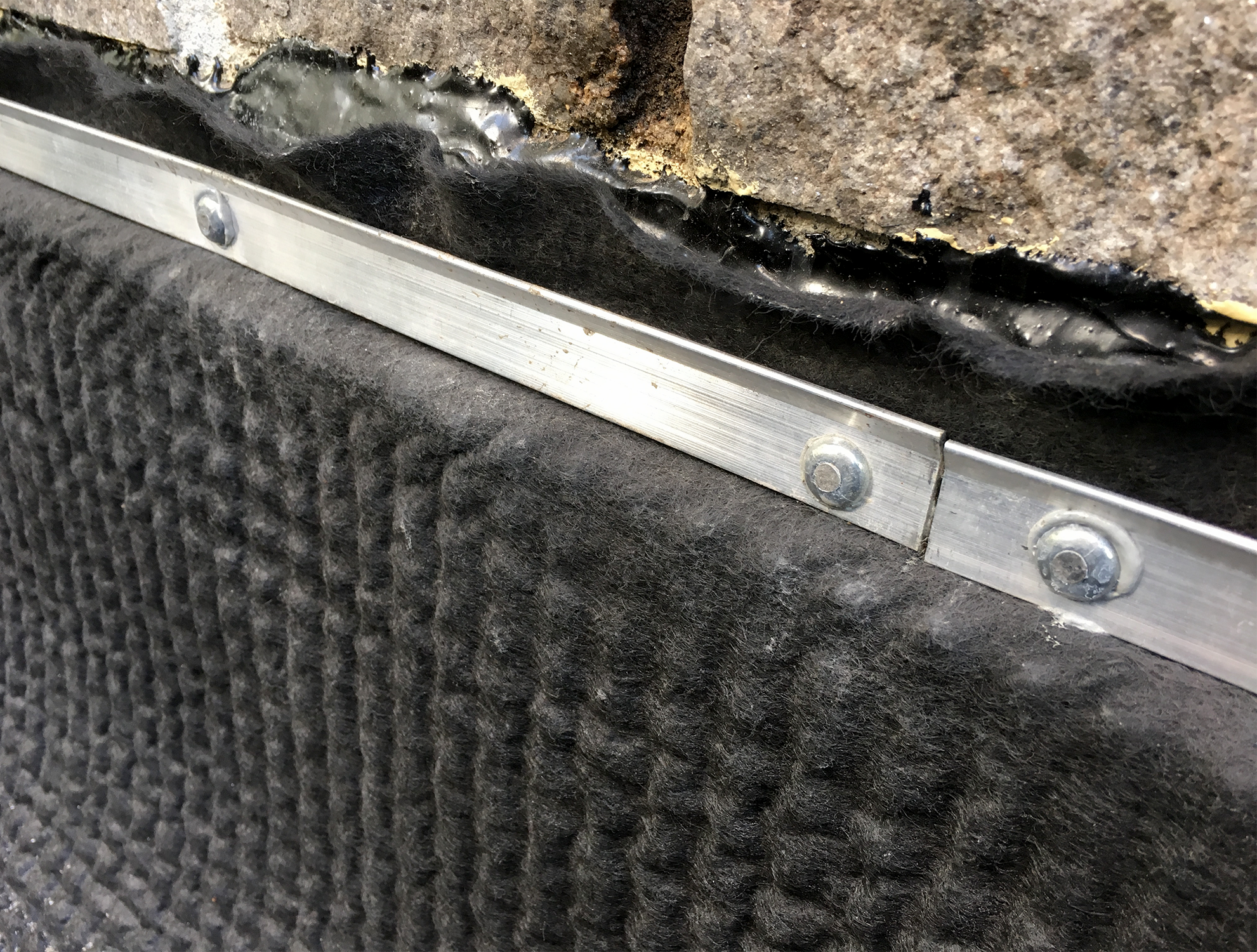
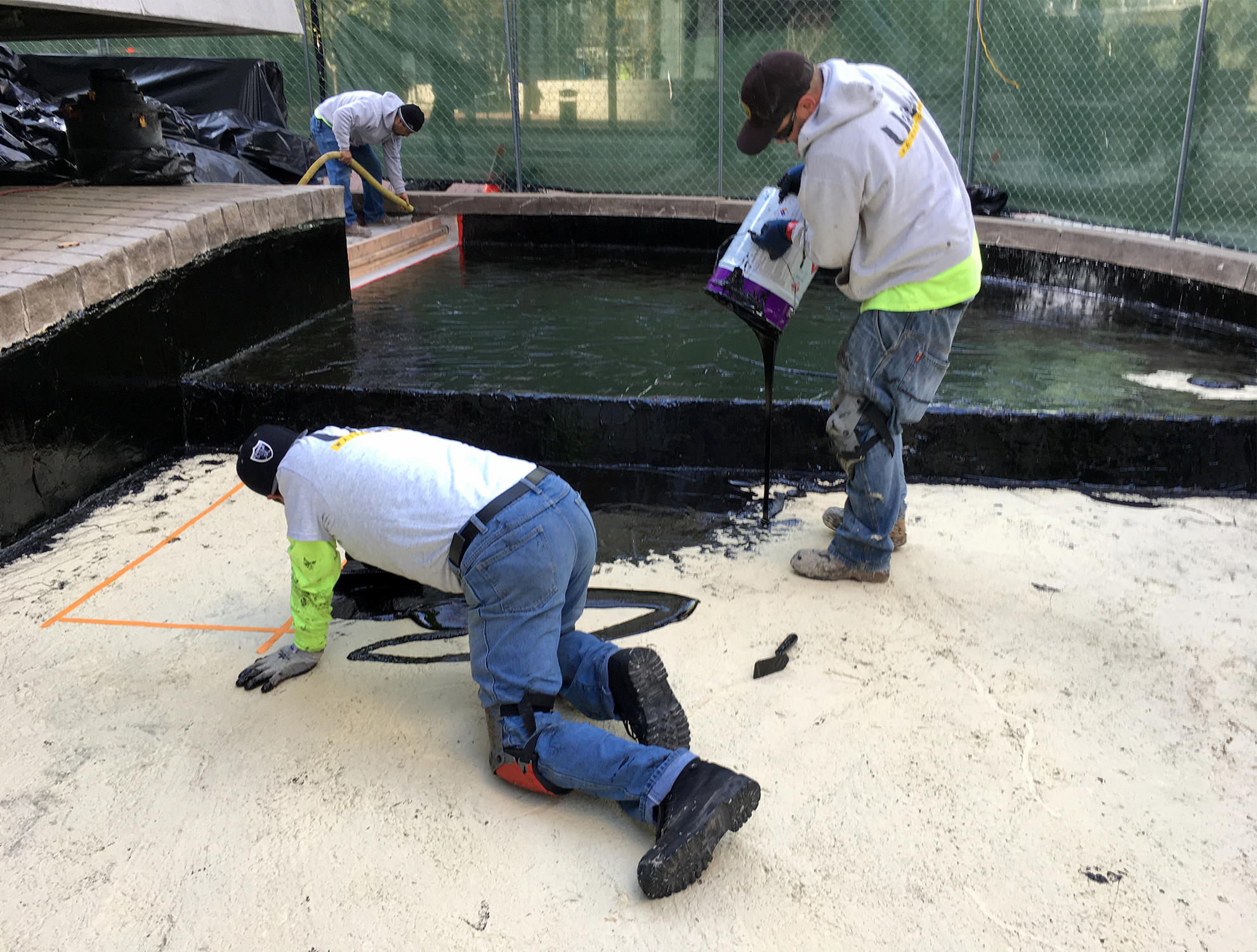
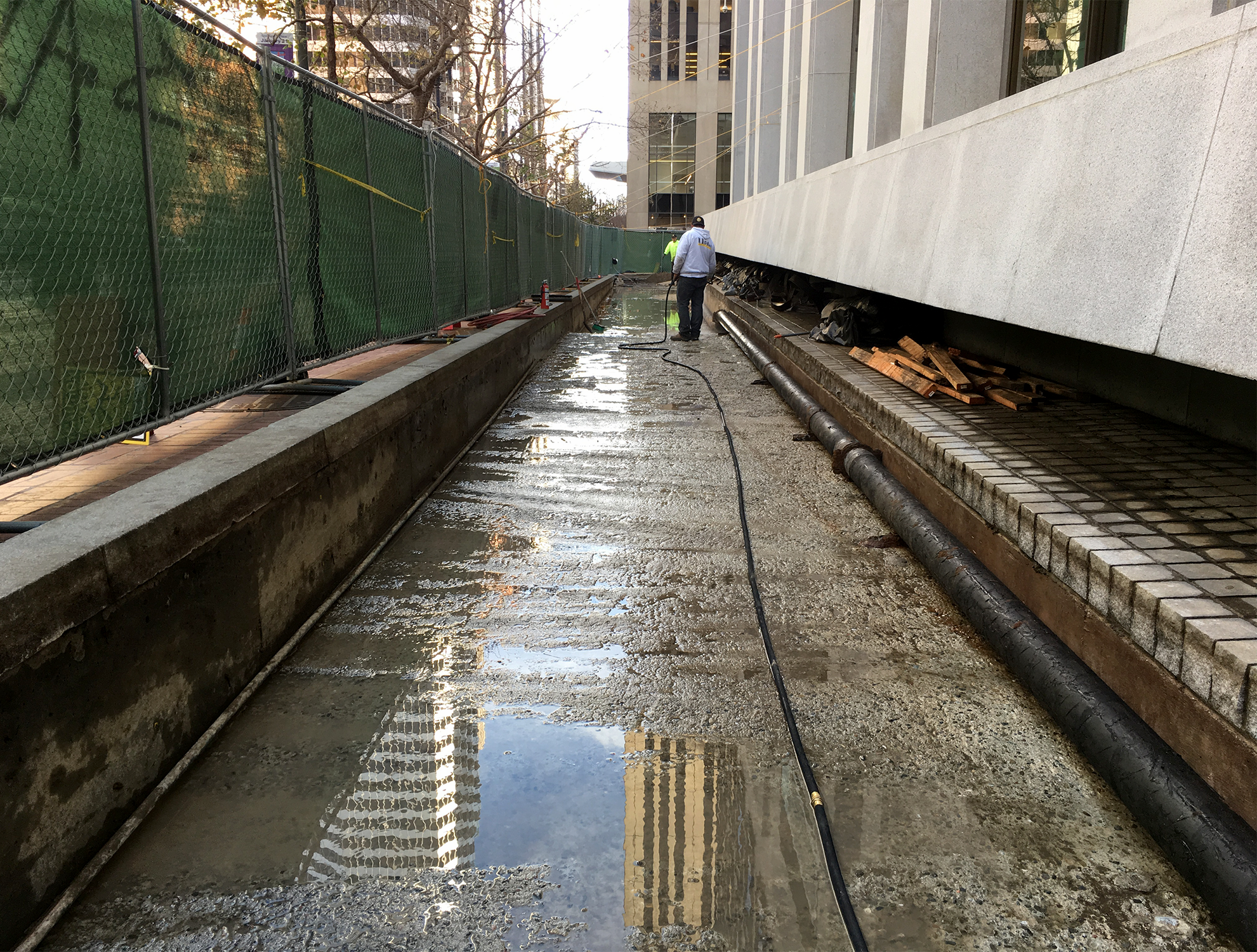
What We Did
Completely scraped off and removed over 4000 sf of the original asphaltic membrane
Ground every inch of concrete to receive a new coating
Caulked all transitions with urethane sealant as a first waterproof layer.
Applied 120 mills of CIM 1000 waterproof membrane to all planter boxes—almost 400 gallons.
After the water test, we installed a drain mat and protection board.
All work was performed in the very busy financial district pedestrian area.
Project Details
After all the soil and landscaping were removed and stored, Urban got to work on the difficult task of removing the original asphaltic membrane. Always a challenge due to the "more is better" philosophy of original construction asphalt membrane installation, the team toiled for nearly a week, scraping off the existing coating by hand and grinding the substrate down to fresh, profiled concrete. All trends and irrigation stub-ups were carefully detailed, and numerous cracks in the bottom and side of the planter box were routed out, primed, and caulked with urethane sealant. Then, all edges and right-angle transitions were caulked with urethane sealant as well to ensure cold joints were reinforced with caulking and the new membrane coating had an easy transition from vertical to horizontal planes. As with the prep stage, the drains and stub-ups were detailed with cove beads of sealant. With all prep and caulking completed, the team installed over 400 gallons of CIM 1000, using heavy-body trowel grade on the vertical walls and self-leveling roller grade on the planter floor, marrying the two together for a monolithic impervious waterproof membrane.
With the membrane installed, a water test was conducted to ensure the new membrane was fully watertight before covering it with a drainage course and protection board and turning it over to the landscape team to install new landscaping.
Want to know how we can help with your next project?