Custom restoration of a historic Oakland landmark
The Leamington Building
1814 Franklin Street
The Leamington Building is a registered Oakland Landmark full of history. This Spanish-style neoclassical 12-story building was built in 1926 as a hotel that housed events such as nightclubs, rock concerts, and restaurants. It was converted into an office building in 1983. The extremely ornate concrete exterior was in dire need of restoration, as it had deteriorated after years of weather exposure to the point that a safety hazard from loose/falling concrete was a concern. Urban Waterproofing was called upon to completely restore the exterior.
The project involved recreating extremely intricate concrete ornamentations that required custom molding, forming, and in-situ hand sculpting. The repairs are truly a work of art. After the project was completed, the building was restored to the condition in which it was originally built.
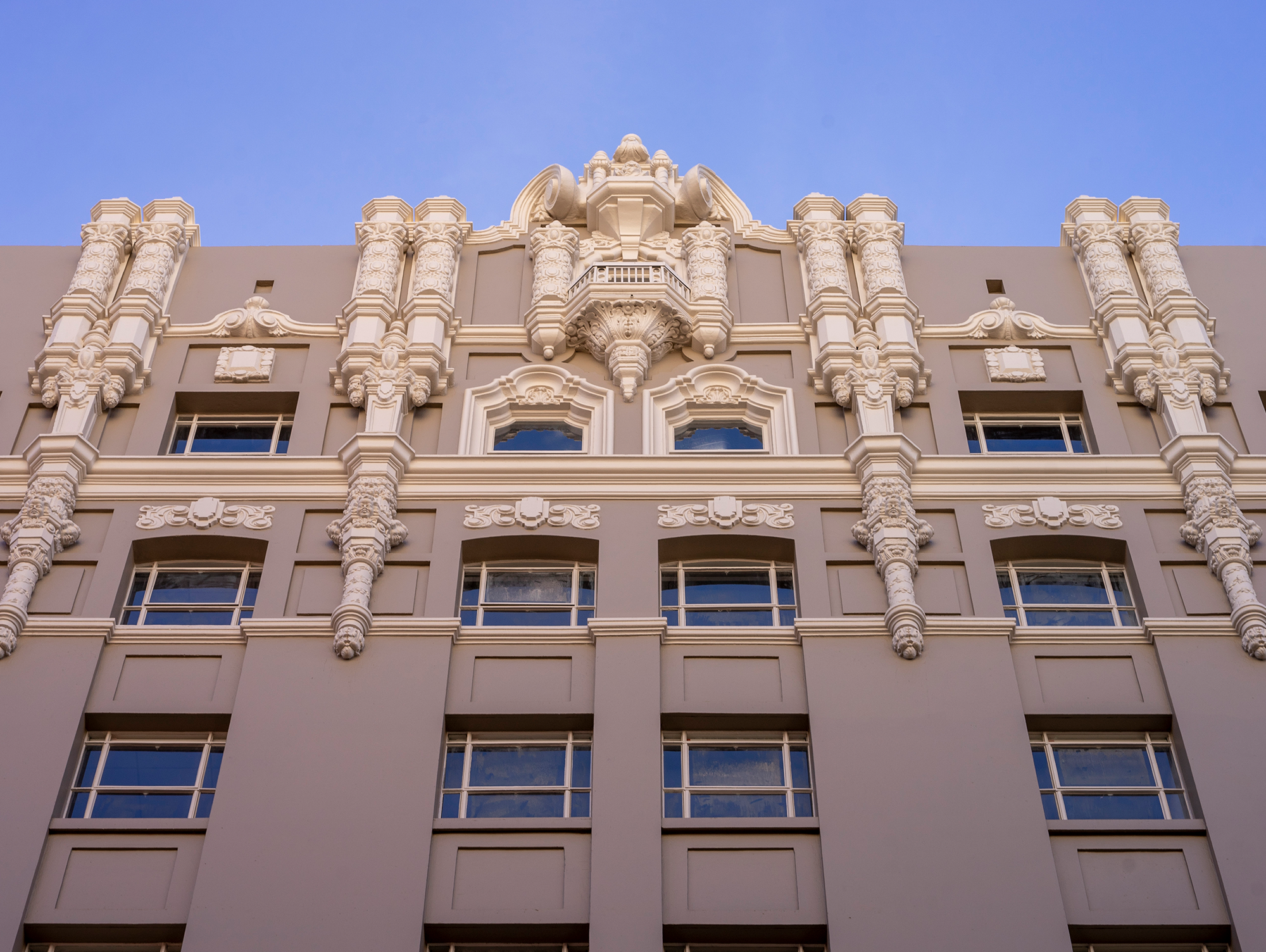
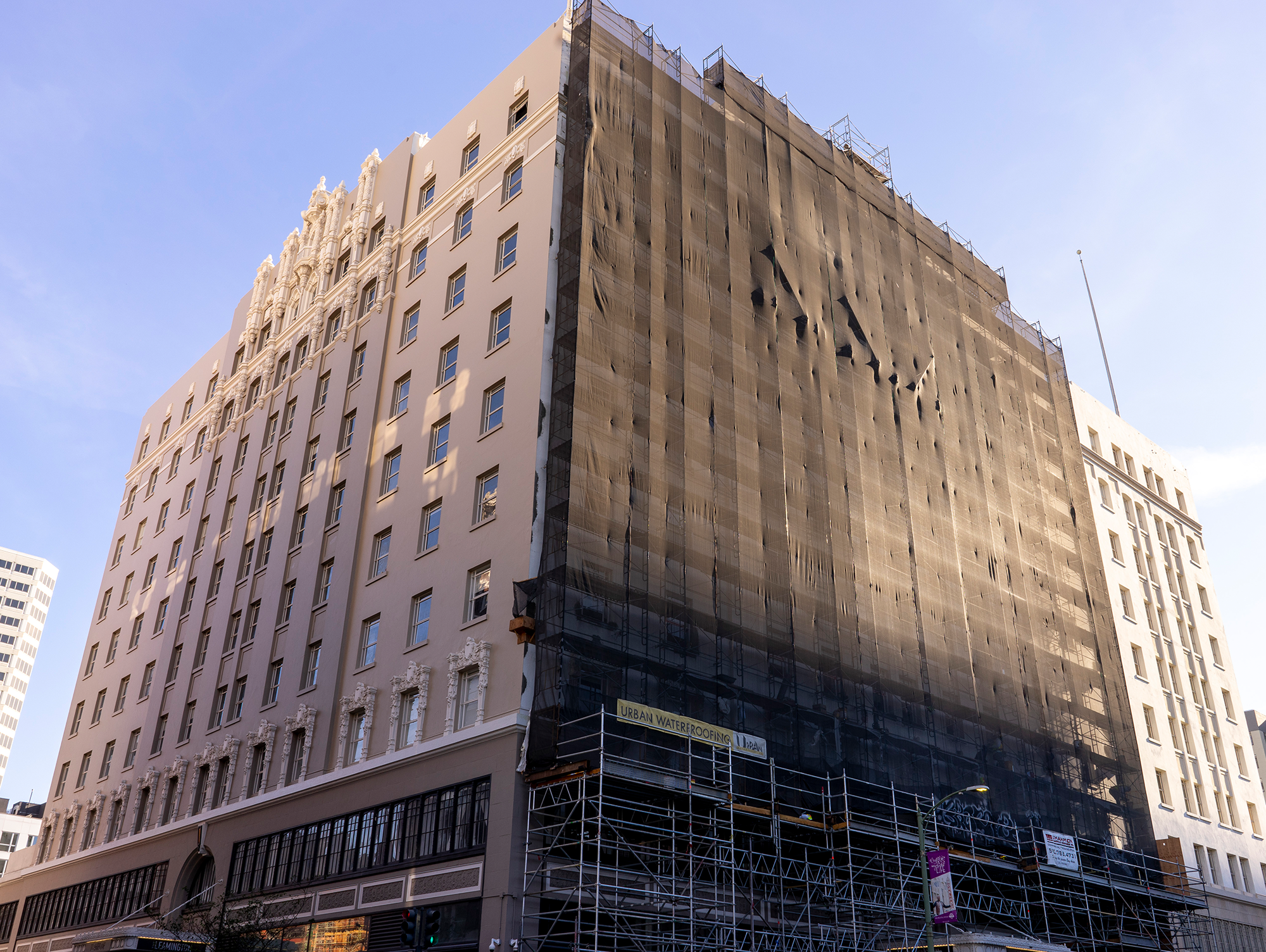
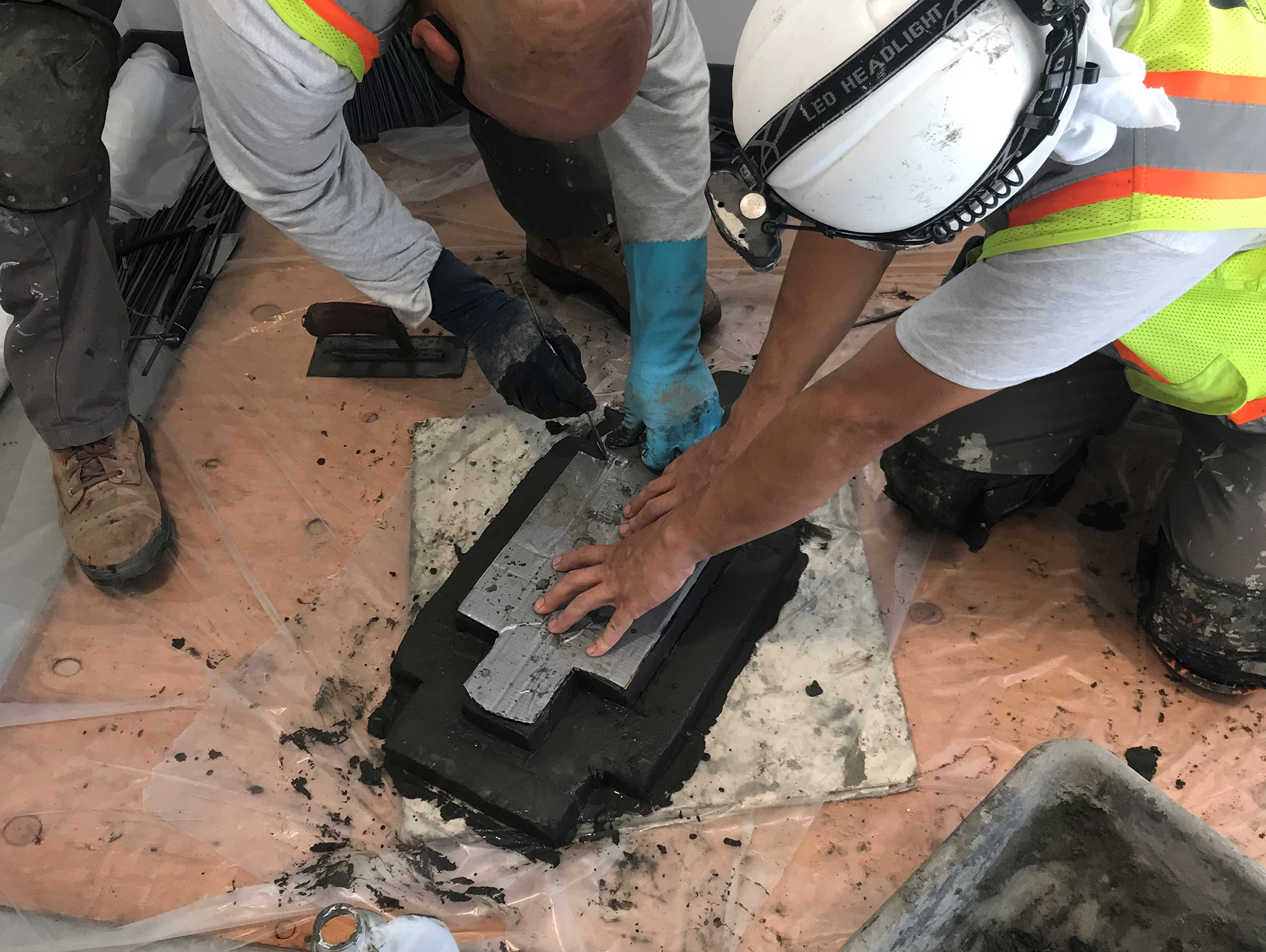
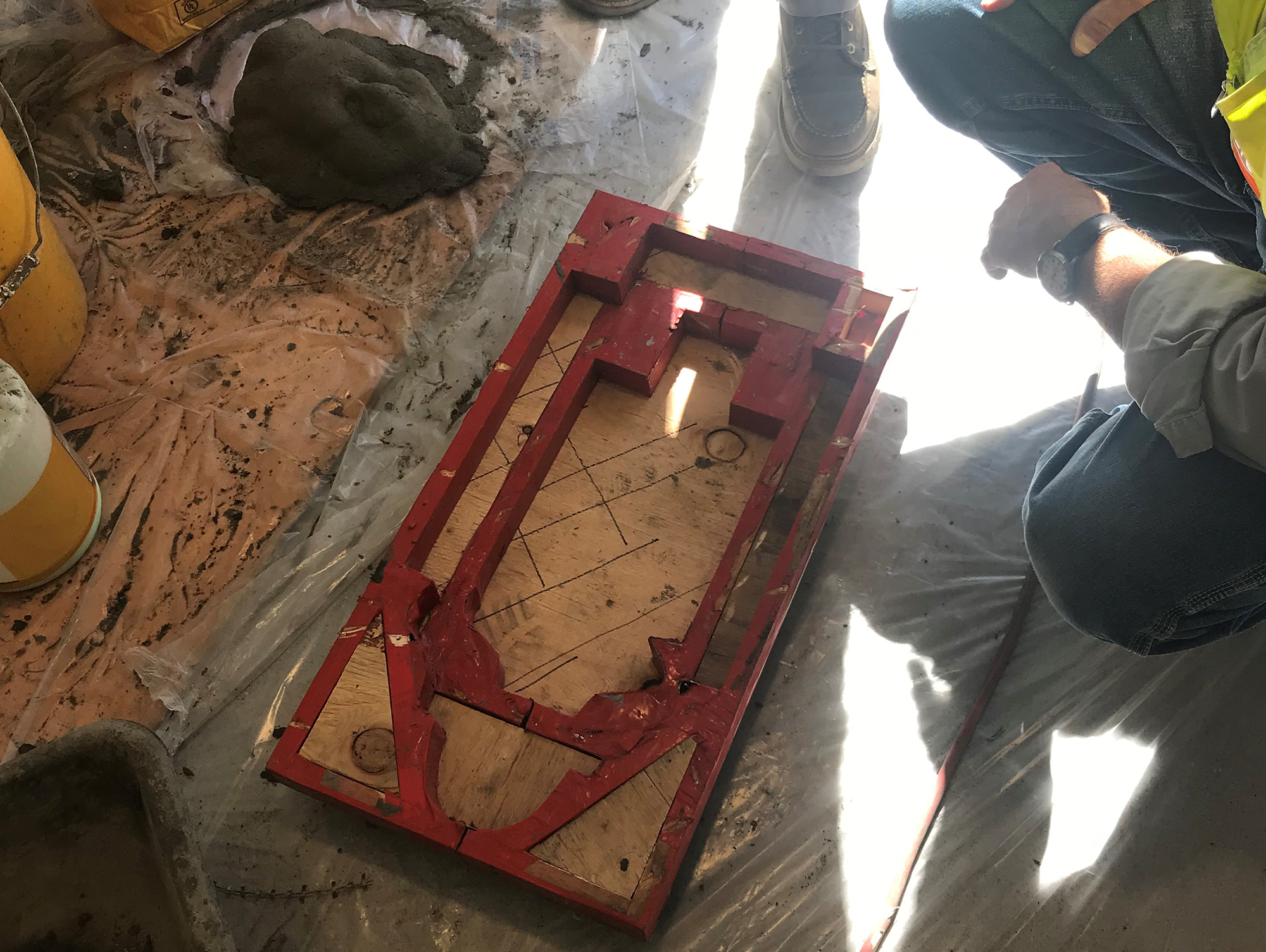
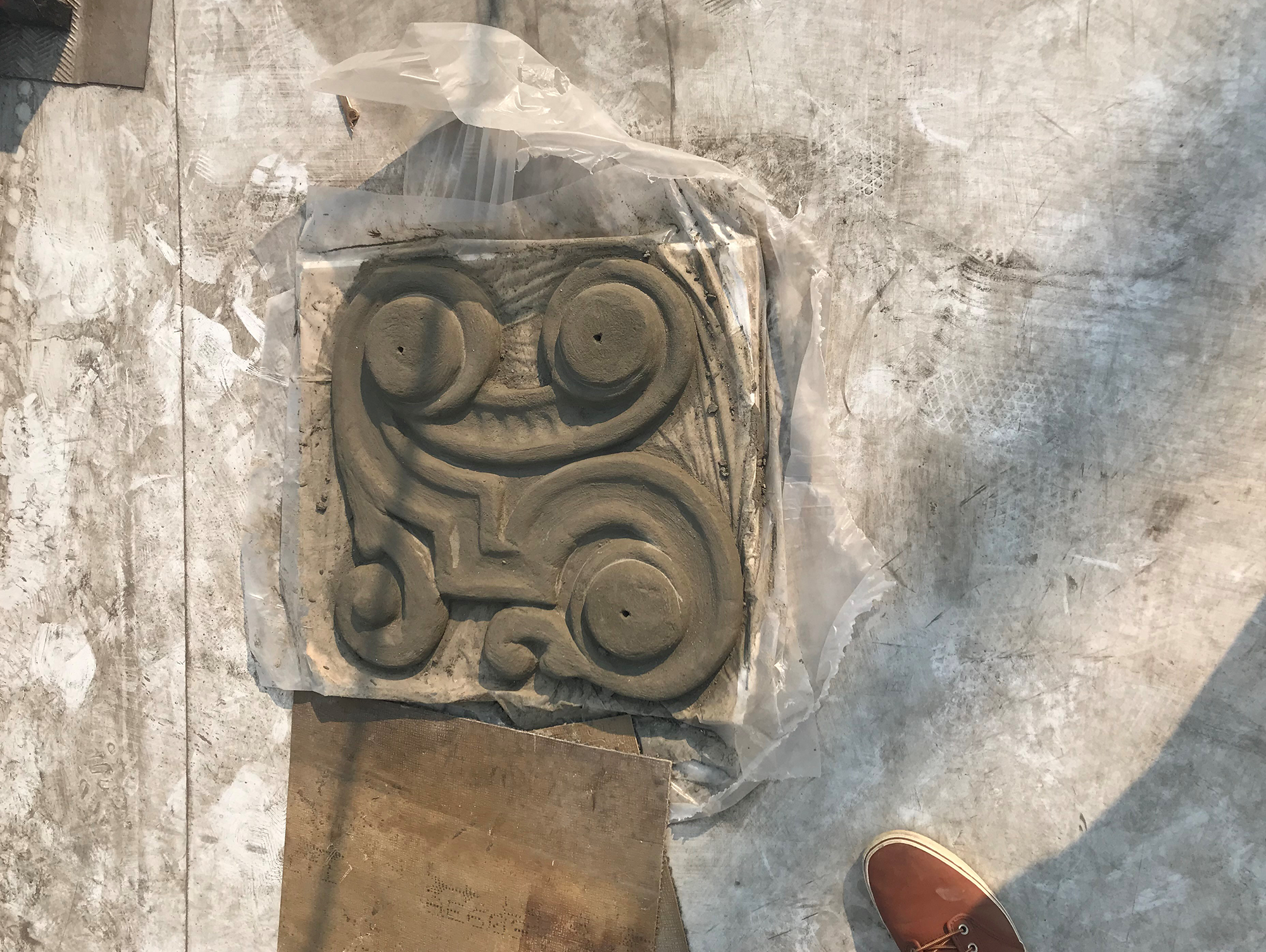
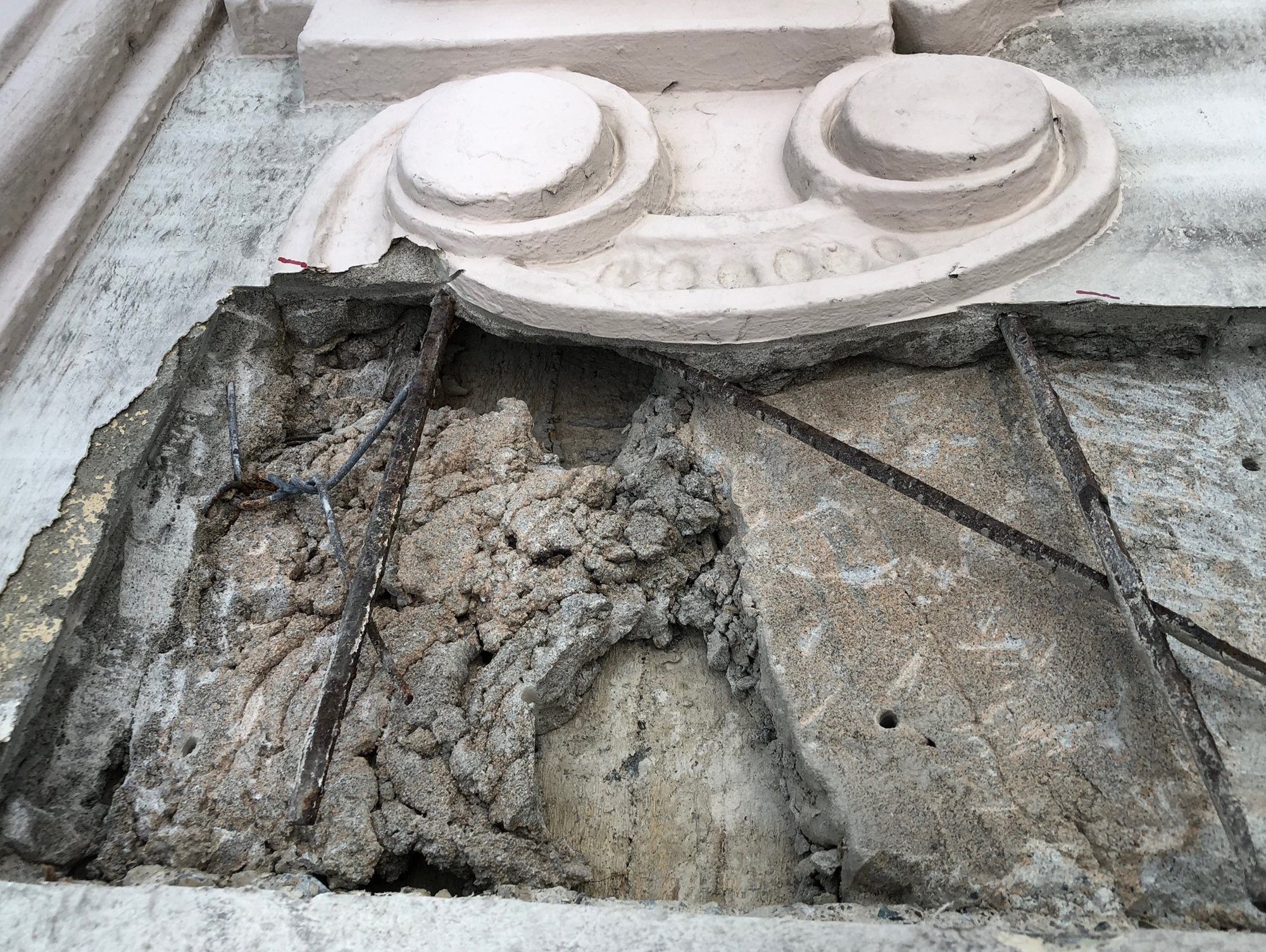
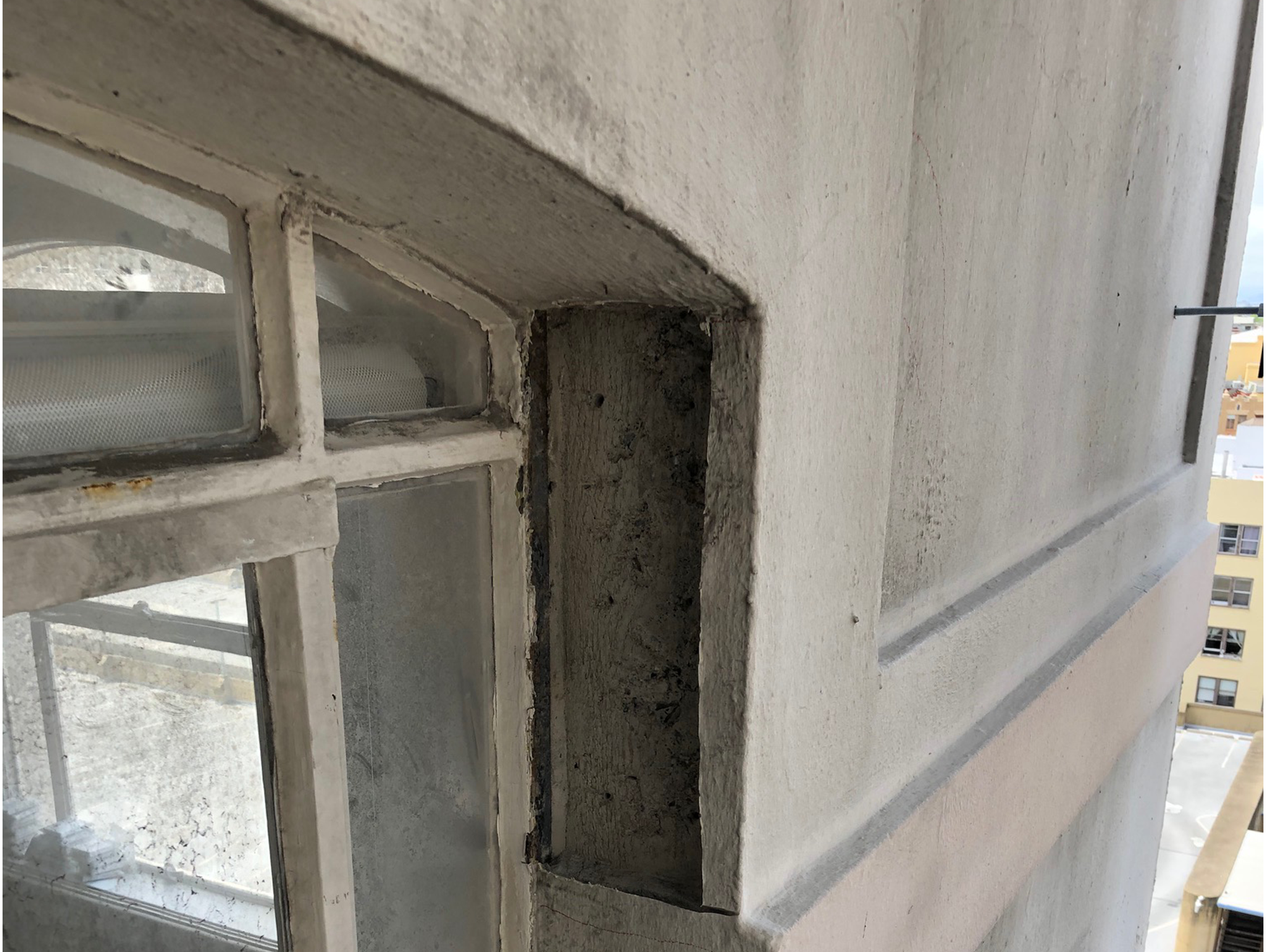
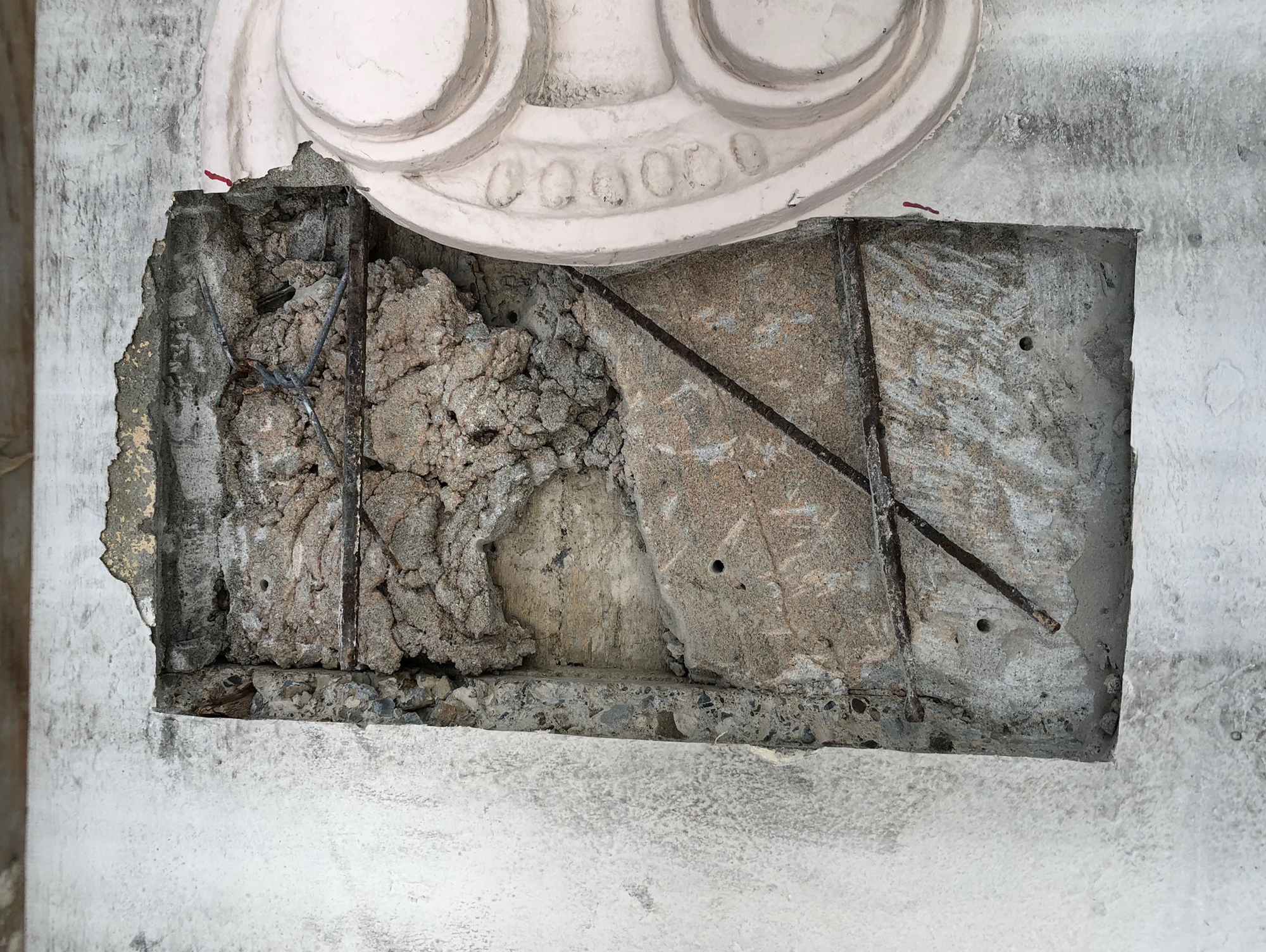
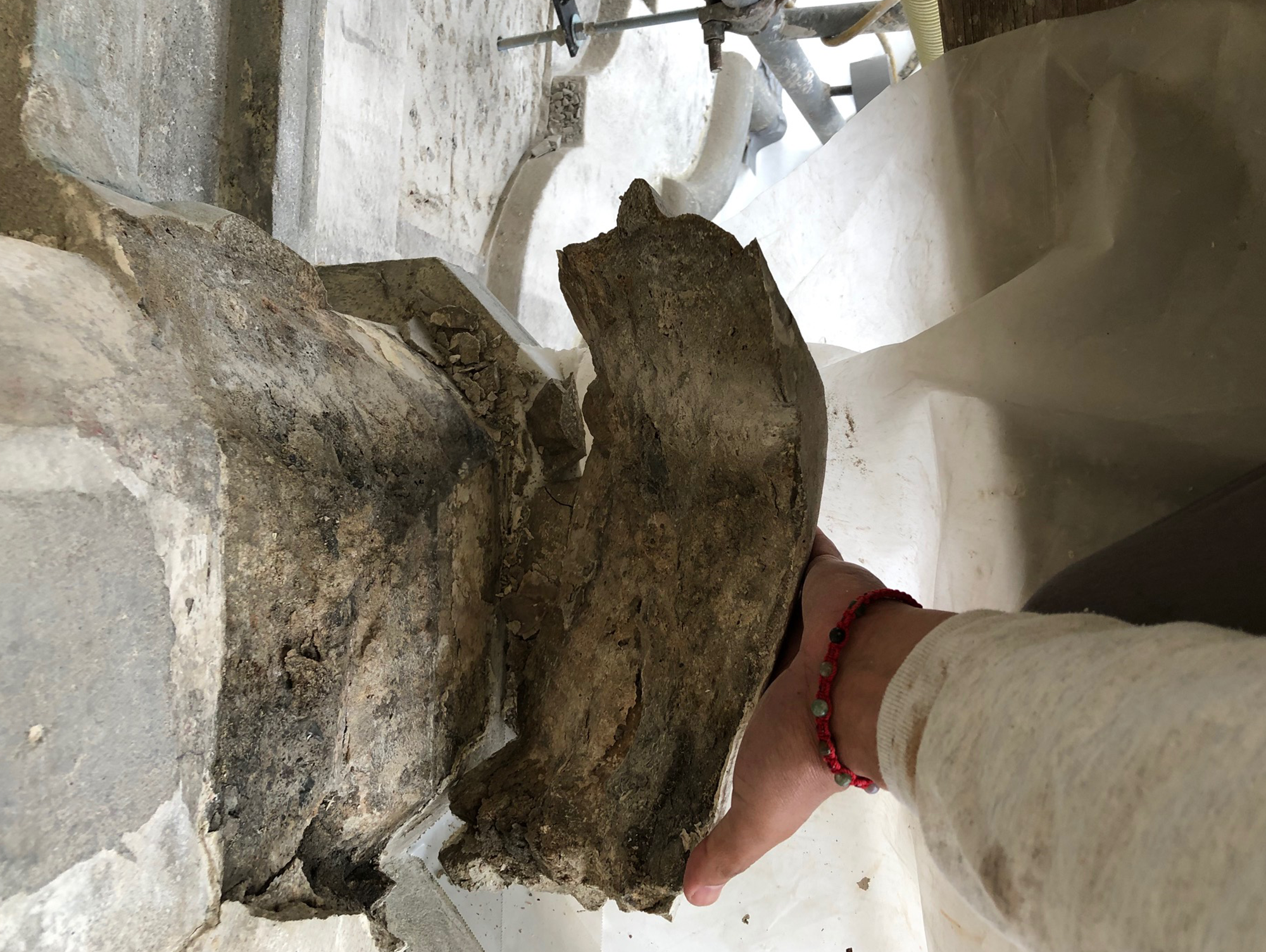
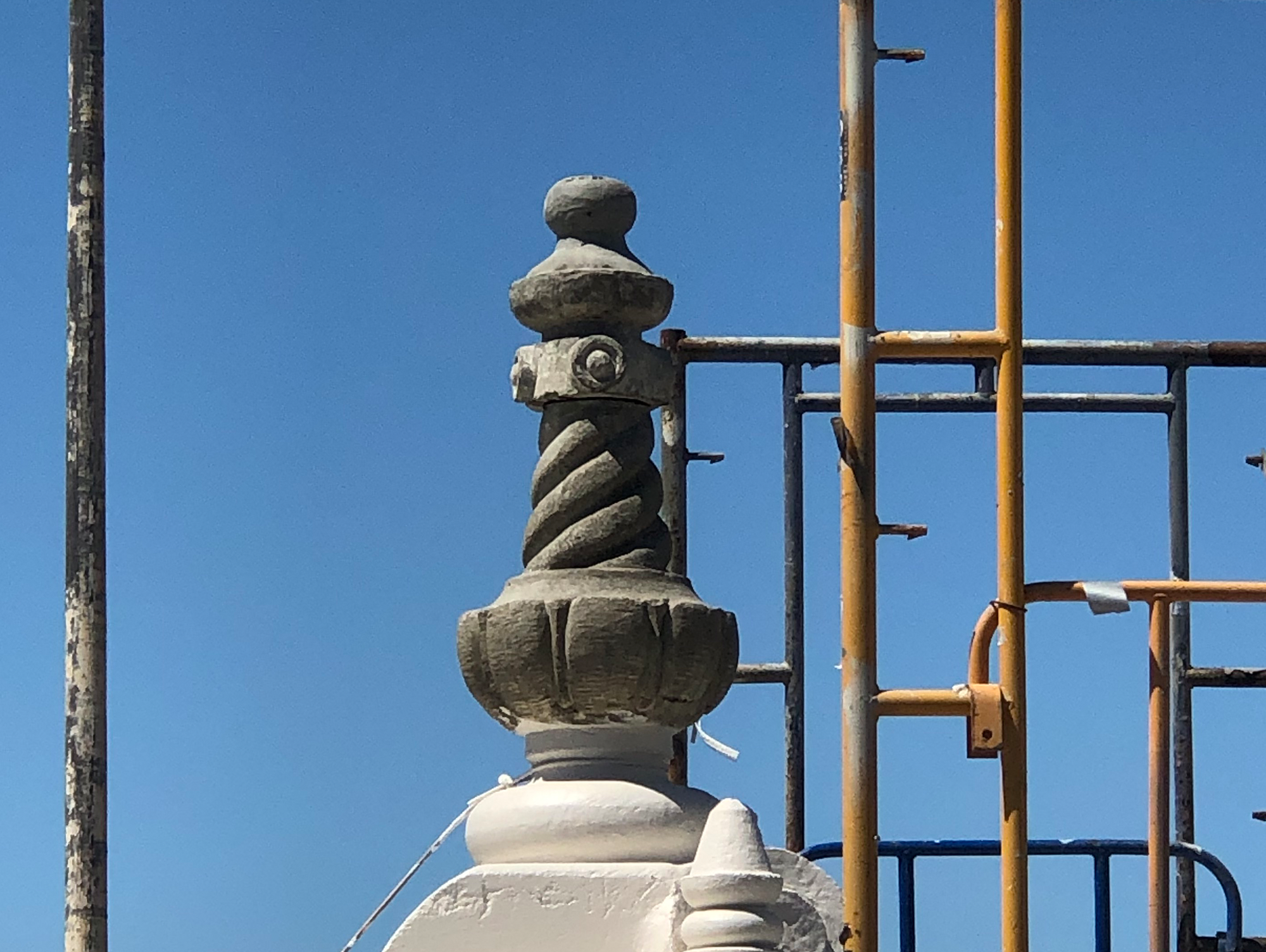
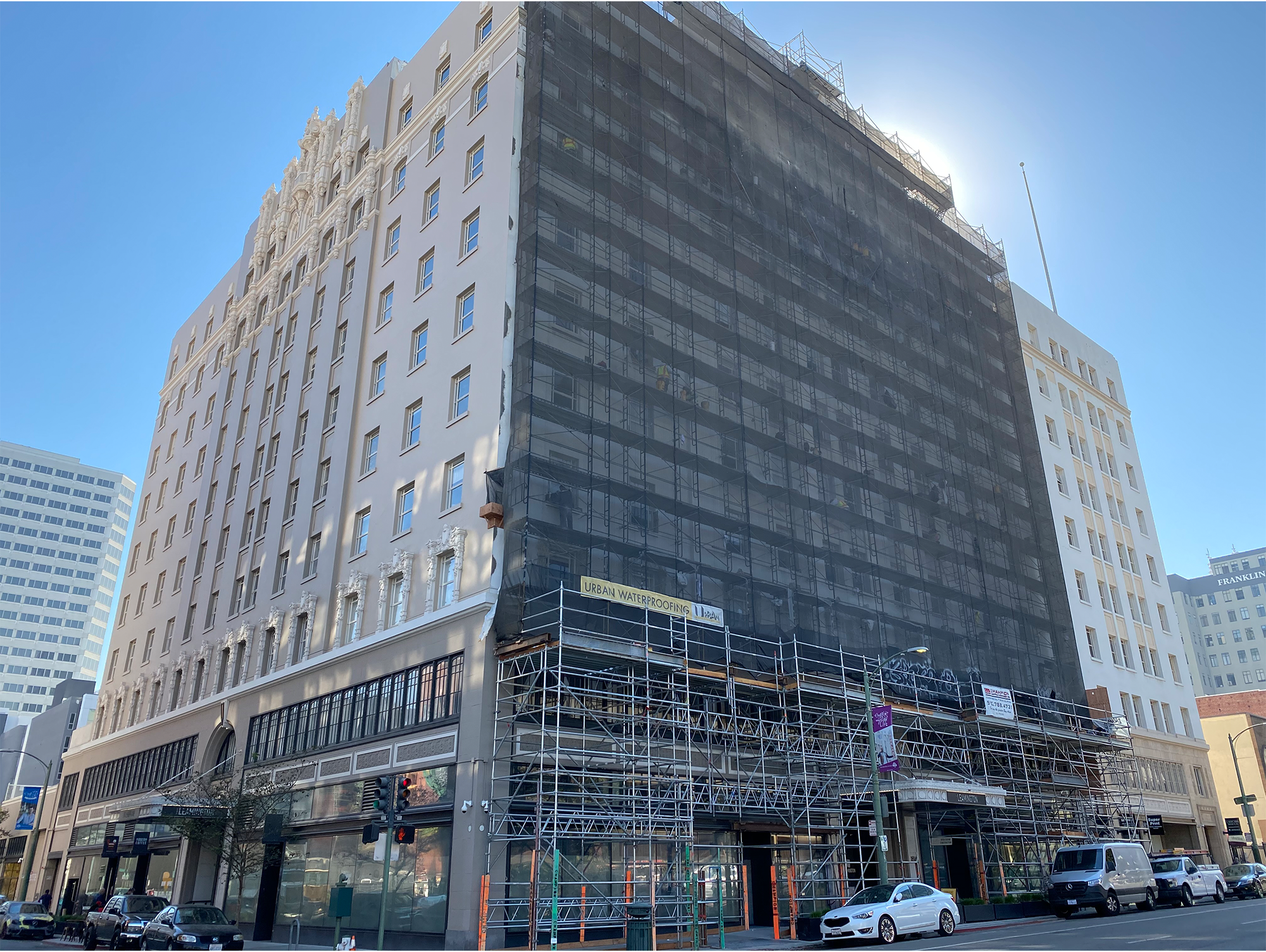
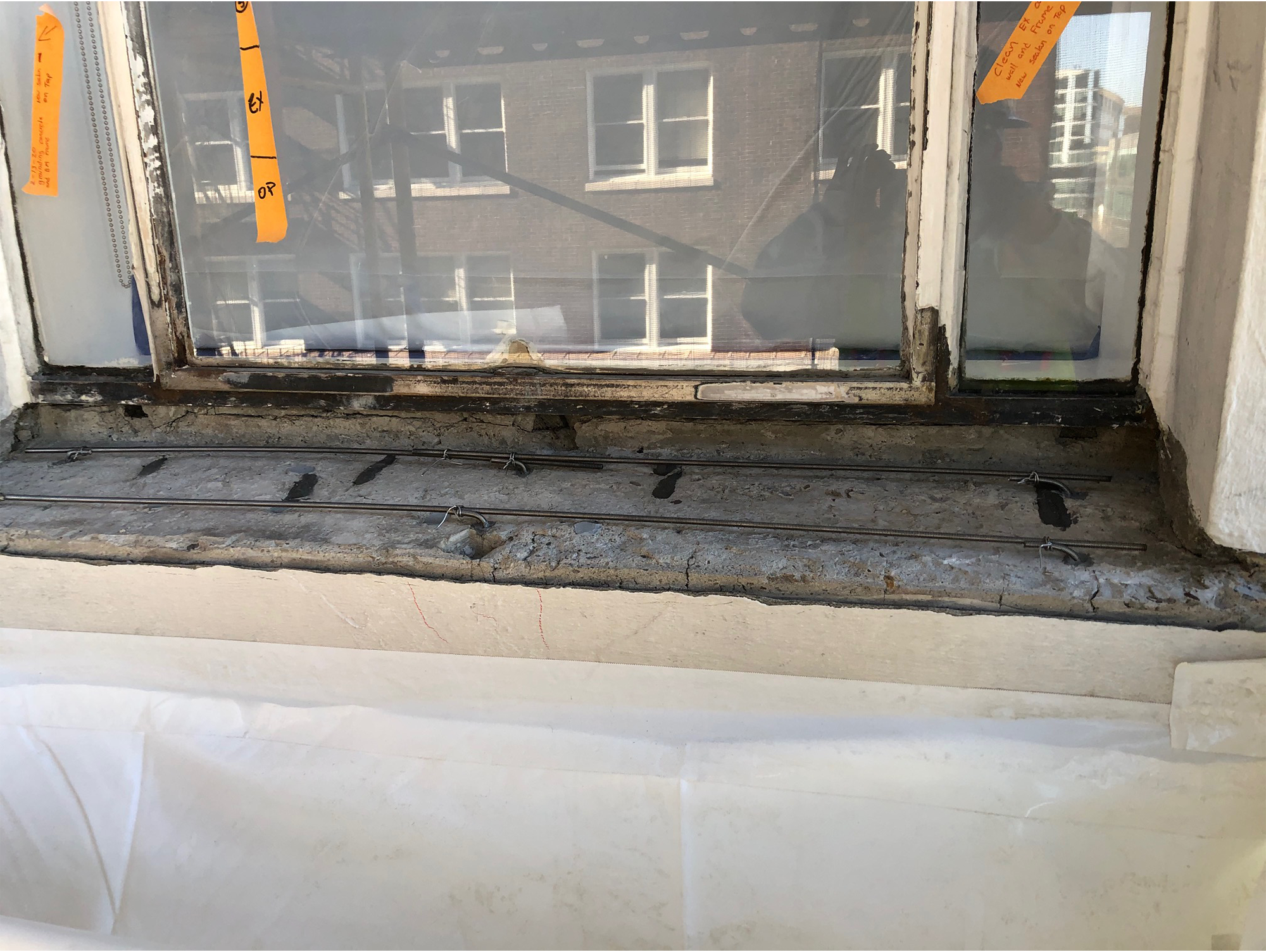
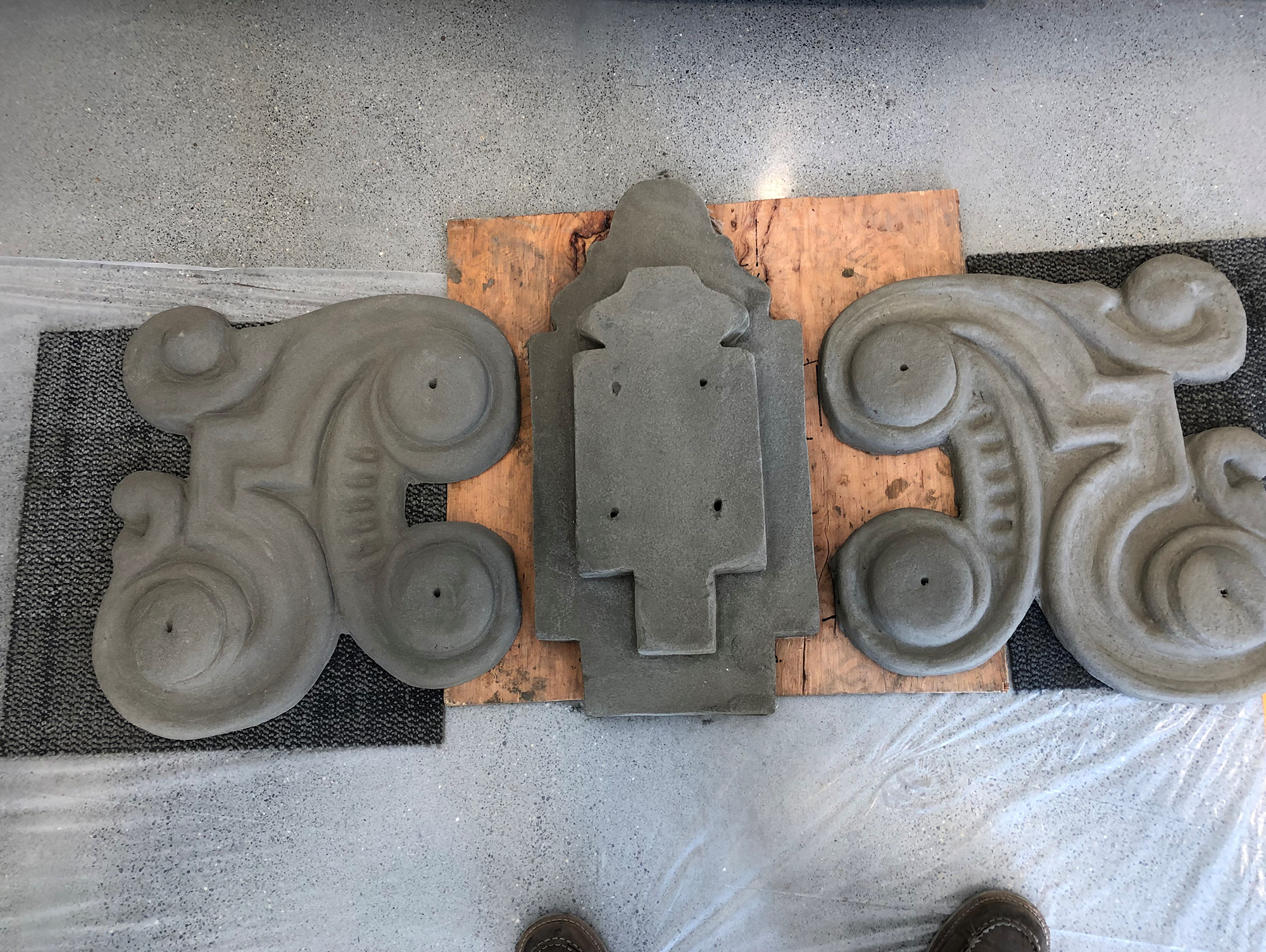
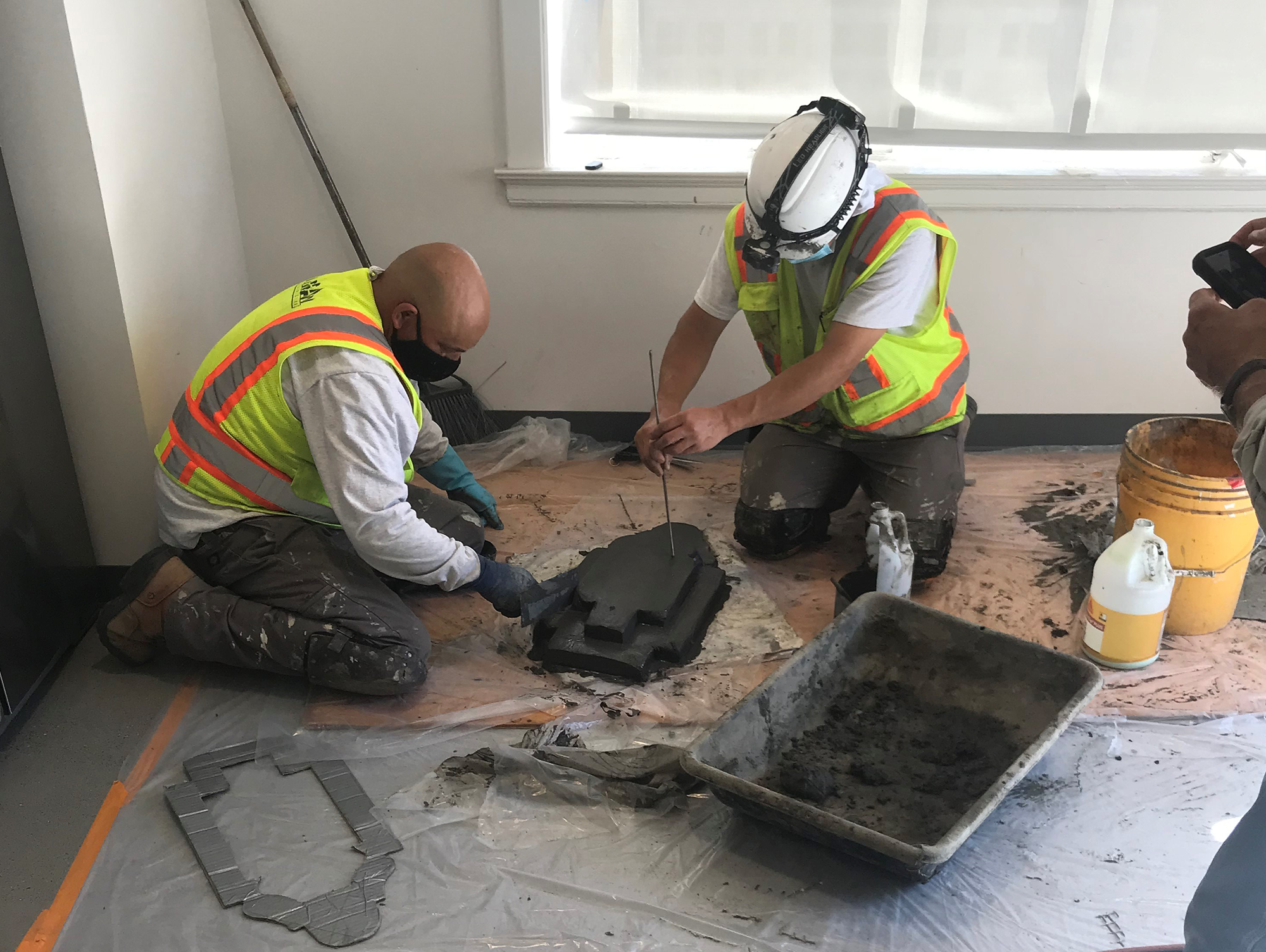
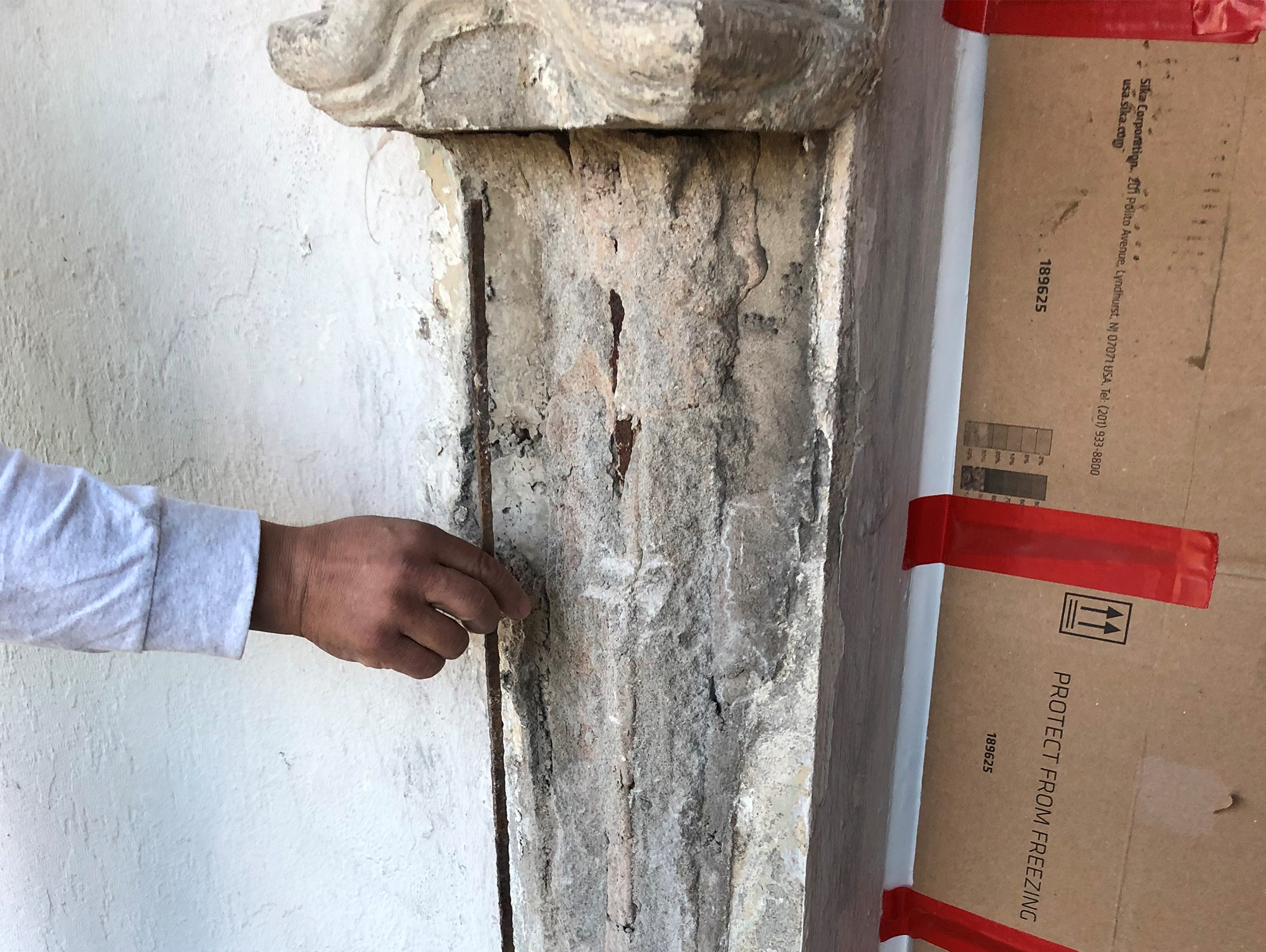
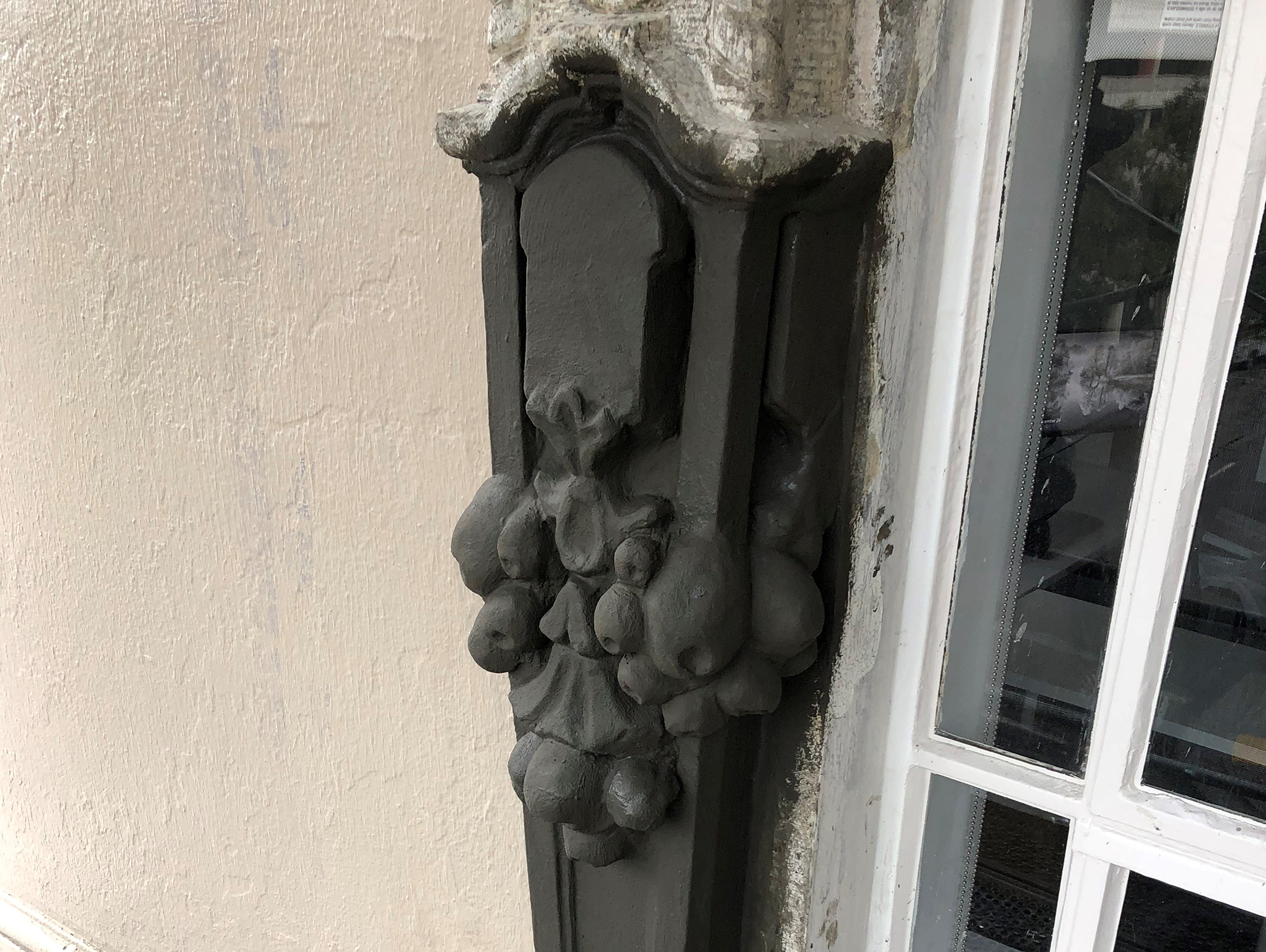
What We Did
1,200 square feet of concrete spall & ornamentation repairs
Complete restoration of 186 steel windows.
Replacement of all exterior sealants.
Installation of wall coating on the entire building facade.
Abatement of various hazardous exterior materials.
Project Details
The extensiveness of the repair work required that full scaffolding be built to access the entire building facade. The scaffold needed to be shrink-wrapped and netted to ensure that the work could proceed unimpeded by weather.
This was not a run-of-the mill concrete repair project. One of the challenges was the variety and amount of intricate concrete ornamentation that are unique to this building. After removing loose / spalled concrete, various concrete patching techniques needed to be used. For elements that recur throughout the building, custom molds were created so the details could be duplicated without deviation. For unique, complex elements, in-situ hand sculpting with extreme craftsmanship was necessary; these were literally works of art.
The other major scope of this project was the restoration of all the original steel windows. Deteriorated glazing putty was removed and replaced. Loose paint on the steel frame was removed. The exposed steel frame was treated per SSPC standards to ensure proper bonding of the new coating. After all surface preparation was carried out, a new high-performance coating was applied to the steel frames.
After all the repairs were completed, an acrylic elastomeric coating was installed on all the wall surfaces to provide prolonged protection from weathering.
The success of this project required constant coordination with building tenants. As this is a concrete structure, any noise and vibration from demolition would reverberate long distances throughout the building. As such, demolition work can only occur during off-hours. This meant the work sequencing and logistics needed to be carefully planned out and communicated to the building management.
Want to know how we can help with your next project?